A thermoplastic composition in abrasive applications helped bearings meet end user specifications.
08/14/2015
One of the largest electric power generation companies in the U.S. conducted an upgrade project of their water pumps at their nuclear plant facility. The pump original equipment manufacturer (OEM) was contracted to produce a series of vertical circulating water pumps. The vertical pump model is designed to pump high volumes of seawater and has an external flush provided to each of the four composite bearing locations. The bearings are composed of a proprietary thermoplastic material, which is designed specifically for use as bushings, bearings and wear rings in pumps handling abrasive media up to 250 F (120 C). Its properties make it a more reliable material than traditional rubber, ceramic or bronze.
The Challenge
The nuclear plant engineering team requested that the pump manufacturer add a low-flow/flush alarm to the upgraded pumps. The alarm would trigger when the flush drops below 5 gallons per minute (GPM) of flow to the bearings. The bearings in the pump must survive 15 minutes of low-flow/flush conditions to give the operators adequate time to respond.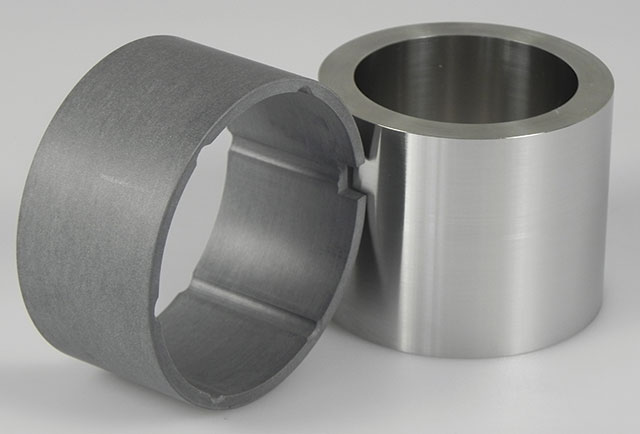
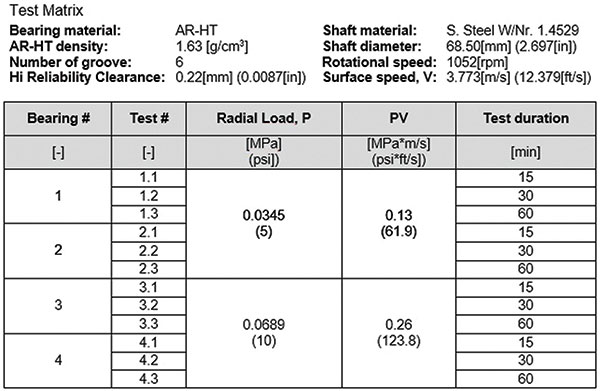
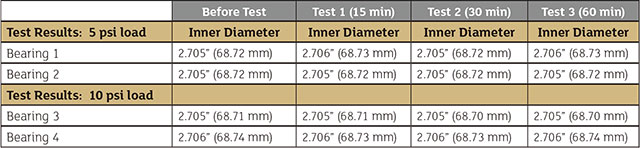
The Solution
A test program was developed to confirm the bearing's ability to survive in the end user's condition. The program's objective was to verify that the running clearance would remain within an acceptable limit (less than two times the original clearance) after a 15-minute dry run, using the same operating conditions as the vertical pump.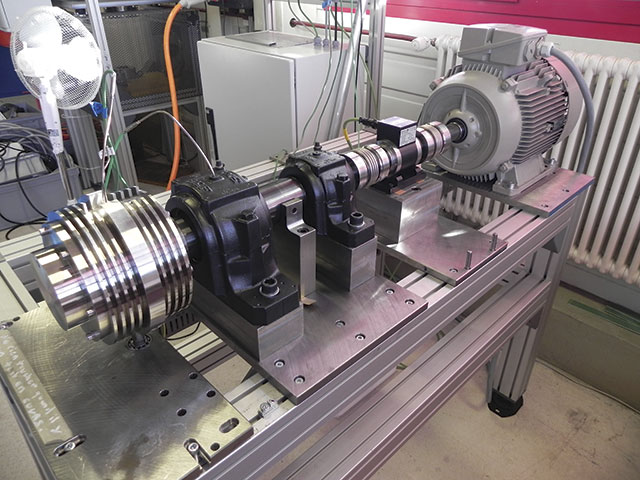