One unique design transmits torque across the disc pack assemblies purely by friction, helping to prevent issues associated with stress concentration, backlash and chatter.
08/04/2016
API 610, 11th Edition, is one of many standards written and regulated by the American Petroleum Institute (API) to ensure maximum reliability in critical applications. This regulation focuses on the minimum safety, reliability and maintainability requirements for centrifugal pumps used in petroleum, petrochemical and natural gas applications. API 610 pumps can be found in various locations including offshore oil rigs, onshore oil production facilities, oil refineries, petrochemical and natural gas processing plants, and power stations. In addition to regulating pumps, bearings, guards and mechanical seals, the standard includes key requirements for the flexible shaft coupling mounted between the pump and motor.
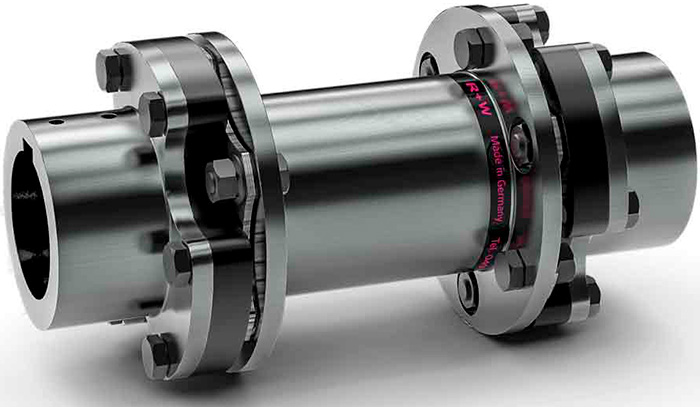
Coupling Requirements
Because safety and reliability of a pump system in the oil and gas industry are critical, detailed requirements of all components are needed. If end users do not carefully select and design these pumps, catastrophic failures may occur. API 610 pump packages should be designed for a minimum service life of 20 years and at least three years of uninterrupted service. Downtime could potentially cost operators millions of dollars per day, so component selection is extremely important. From a maintenance standpoint, many requirements are in place that allow for a quick and simple overhaul of an entire system.API Specifications
An API 610 coupling is an all-metal, flexible element spacer coupling designed in accordance with American Gear Manufacturers Association (AGMA) 9000 Class 9 standards for balance quality to reduce vibration. If operating in excess of 3,800 revolutions per minute (rpm), this equipment must be balanced in accordance with International Organization for Standardization (ISO) 40441.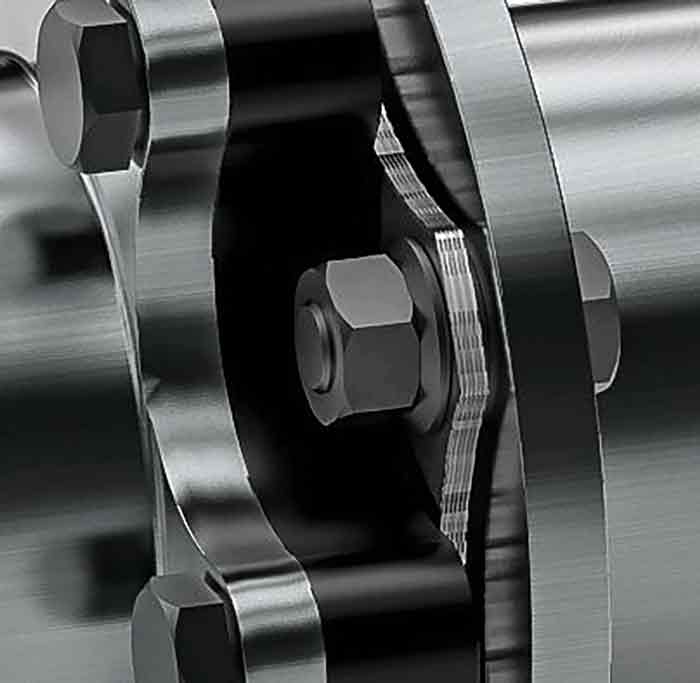