It is common to use graphical techniques to determine the performance of multiple centrifugal pumps operating in series or in parallel. These methods are often time-consuming and rely on the good eyesight of the person making the measurements and a steady hand while drawing the combined performance curves. Numerical techniques can be employed to determine the same overall performance of centrifugal pumps operating in series and in parallel. This article will identify the steps for using numerical techniques within an Excel spreadsheet to achieve this goal. It will provide sample calculations of those numerical techniques with detailed cell formulas so that end users can reproduce this technique in their own pump applications. For this article, it is assumed that each pump is a two-stage centrifugal pump that has different performance for the first stage compared to the second stage. These techniques can easily be extended to accommodate multistage pumps that have more than two stages.
Steps for Numerical Techniques
The individual steps are summarized below: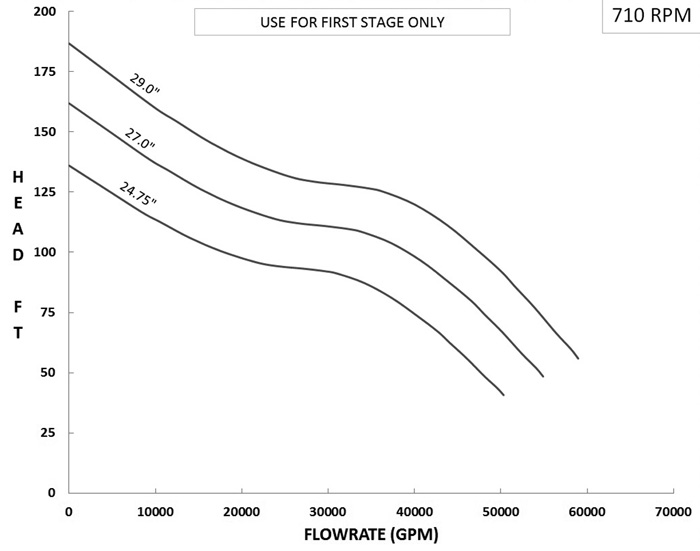
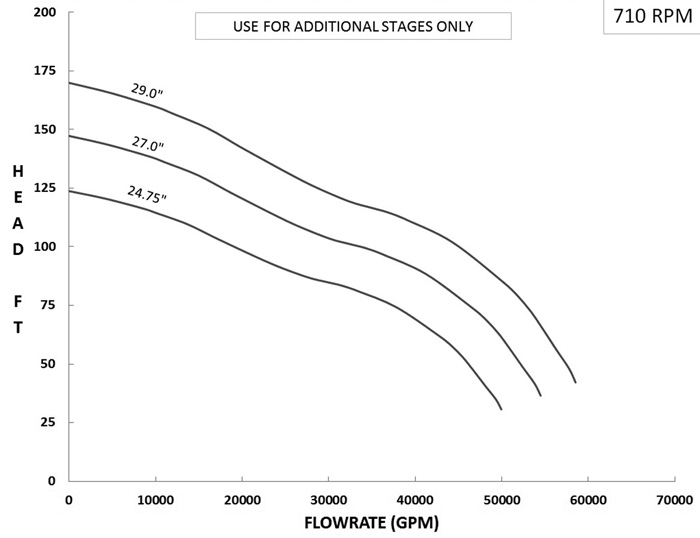
- Digitize or make “rough eye” estimates to measure 10 or more (Q, H) points from shutoff to runout conditions for the first stage pump performance curve of head versus flow. Enter the array of first stage head versus flow data into spreadsheet columns.
- If necessary, use numerical methods to extend the head versus flow data beyond runout. This step is done primarily to prevent subsequent numerical methods from going off into the weeds.
- Curve fit a polynomial function to the first stage head versus flow data, which may include extrapolated data down to zero head rise.
- Duplicate steps 1, 2 and 3 with measurements of the second stage head versus flow data. Although it is not essential, it is convenient and recommended that both polynomial curve fits be of the same order.
- Determine the function of head versus flow for both stages operating together in series. This is done by adding the coefficients of the same ordered terms of the polynomial functions for each stage to establish the applicable coefficients of the polynomial function for the multistage pump.
- Determine the polynomial function for the combined performance for multiple (and identical) pumps operating in parallel. The set of coefficients for the polynomial will vary depending on the number of pumps running in parallel.
- Determine the second order polynomial function, which characterizes the resistance (head loss versus flow) of the system piping.
- Determine the polynomial function that defines overall parallel pump performance minus the system resistance function.
- Determine the derivative of the polynomial function from the previous step. The derivative function provides the slope of the head versus flow curve, which is needed in the next step.
- Use iterative numerical methods to solve for head and flow operating points of multiple parallel pumps operating within the specified system. This method uses consecutive rows of spreadsheet calculations to perform successive iterations of the Newton-Raphson method. Results of each iteration eventually converge to the solution of flow rate.
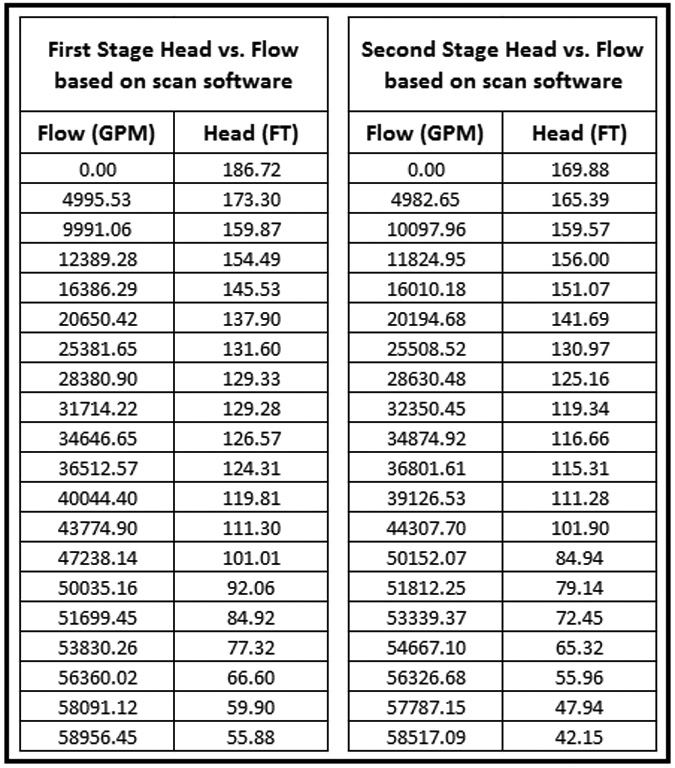
Sample Calculations
A set of sample calculations is provided in this section to demonstrate these steps. Assume that multiple, two-stage centrifugal pumps in parallel are used. Assume that the first stage performance is shown in Figure 1, and second stage performance is shown in Figure 2. Assume that both stages of each pump are equipped with a 29-inch impeller, corresponding to the top head curve shown in Figures 1 and 2. The head curves for each stage were digitized, and the resulting arrays are provided in Table 1. This same data could have also been determined by visual inspection and likely with fewer decimal places. It should be noted that the number of decimal places shown does not imply any more or less accuracy of the calculations based on such data, because the native spreadsheet stores more decimal places than those that are shown. The head versus flow arrays (see Table 1) for each stage can be fitted with a polynomial function that has sufficient order to provide a reasonably accurate representation of the data. For demonstration purposes, assume an eighth order polynomial that has the form shown in Equation 1 that gives the head rise in feet (FT).

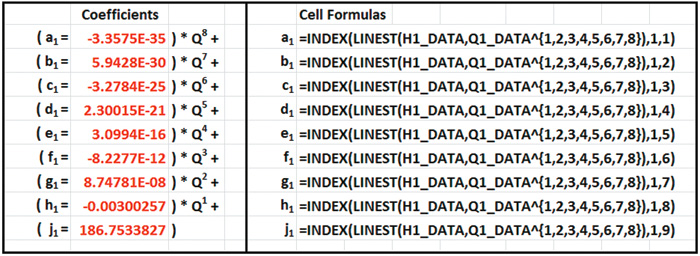
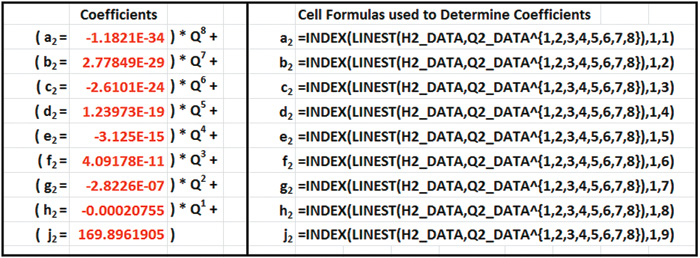
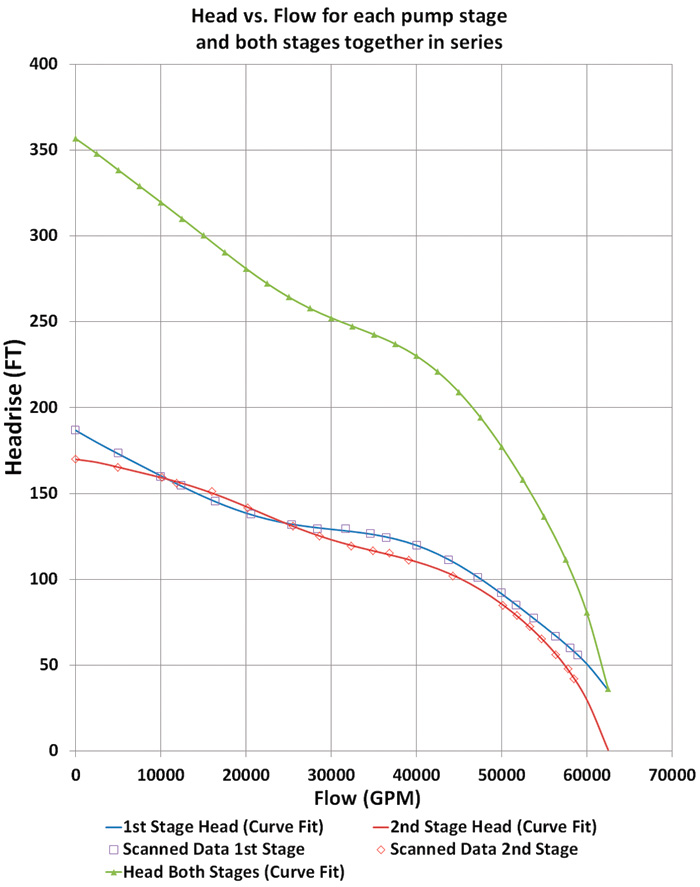
- Range name of “Q1_DATA” will be assigned to the first stage flow rate values shown in the first column of Table 1.
- Range name of “H1_DATA” will be assigned to the first stage head rise values shown in the second column in Table 1.
- Range name of “Q2_DATA” will be assigned to the second stage flow rate values shown in the third column of Table 1.
- Range name of “H2_DATA” will be assigned to the second stage head rise values shown in the fourth column of Table 1.
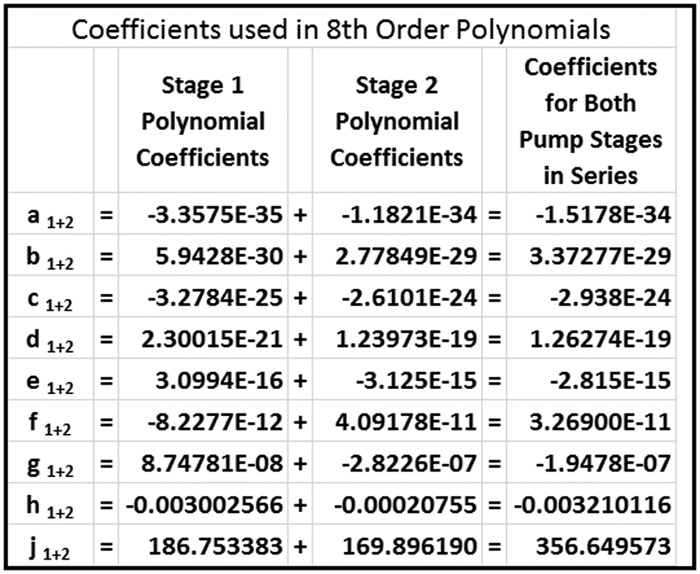

Multiple Pumps Operating in Parallel
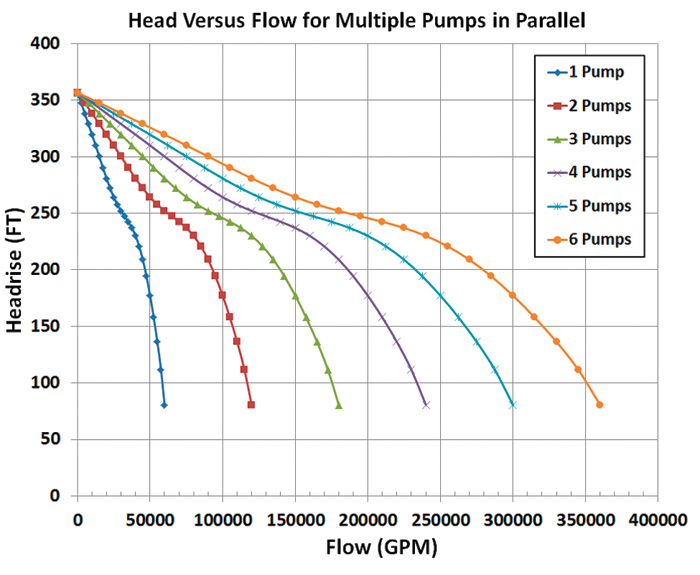

Characterizing System Resistance
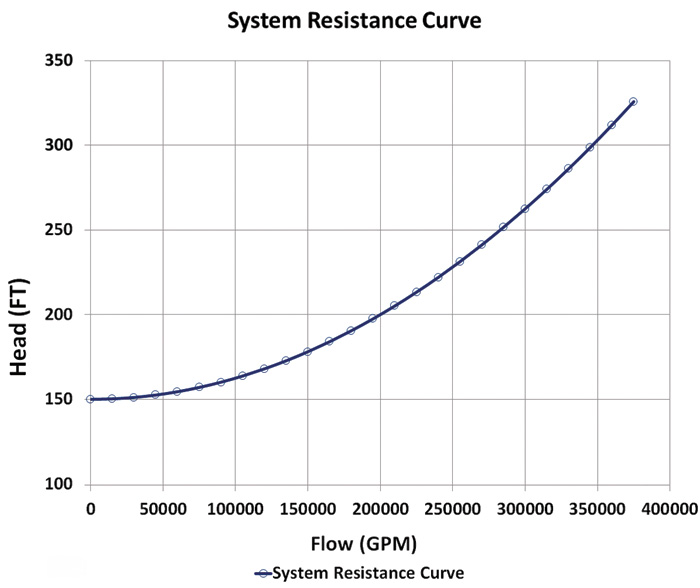
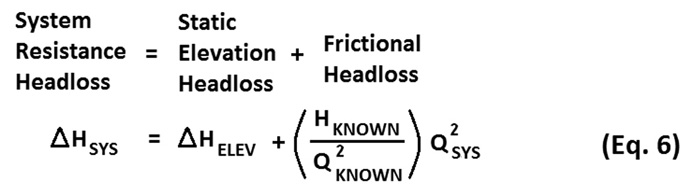
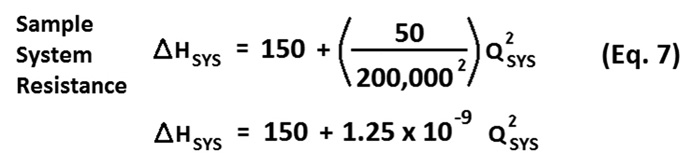

Combining Equations
If end users plot the system resistance curve and overall pump curve on the same graph, the point at which the lines cross will designate the operating point for the pumps. For example, if six pumps run in parallel and their combined performance is shown for six-pump operation in Figure 4, then the operating point could be determined graphically (see Figure 6). If end users can develop a function of ΔHead versus flow, which quantifies the vertical displacement between the two curves as depicted by the two-headed arrow shown at a flow rate of 100,000 gpm (Figure 6), then end users can mathematically solve such a function for the point at which the two curves intersect. The applicable head difference function is obtained by subtracting the system resistance parabolic function (Equation 8) from the overall pump curve polynomial function (Equation 5). This results in Equation 9.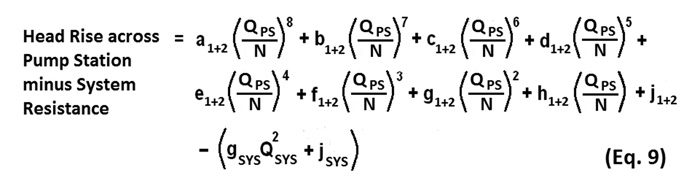
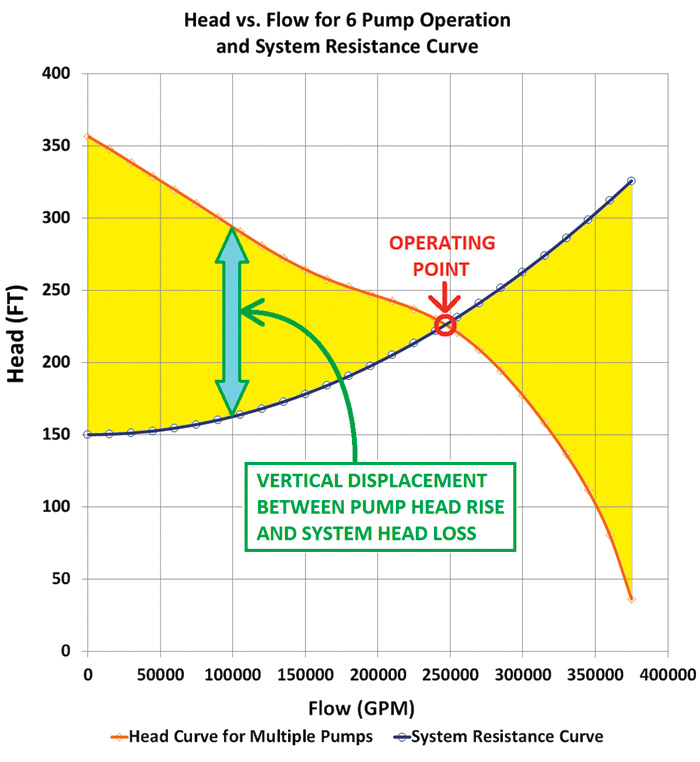
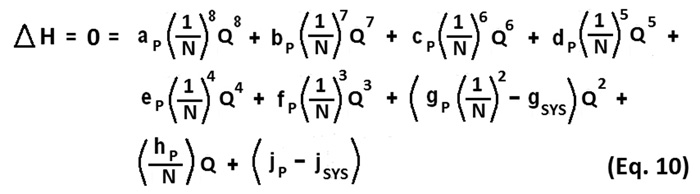
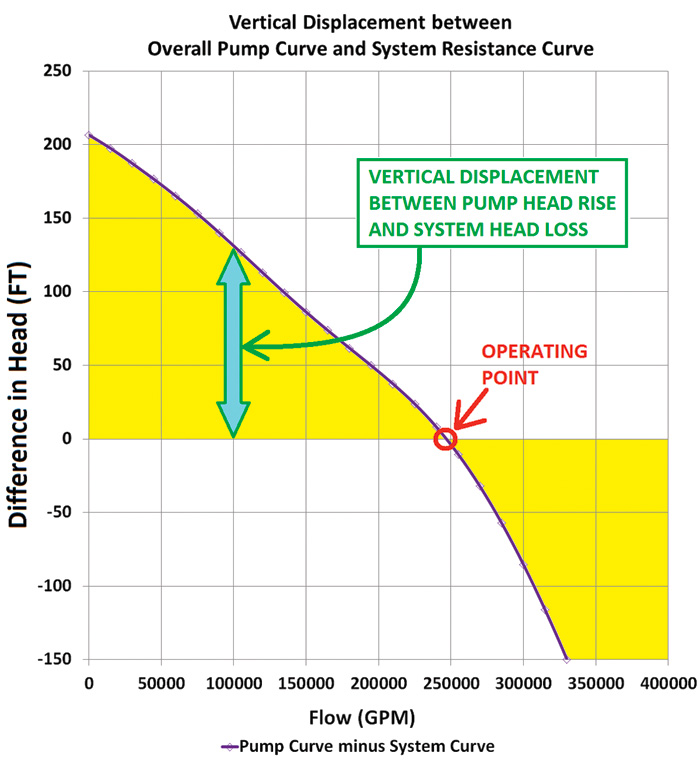
Numerical Solution of Flow Rate
Flow rate can be determined by solving Equation 10 for a specified number of running pumps by using numerical techniques. A solution within an Excel spreadsheet is achieved by using “GOALSEEK,” in which an initial guess at flow rate is input into one cell, and another cell contains the formula shown in Equation 10. Within the “GOALSEEK” pop-up window, the user chooses to seek a value of flow rate, for which the computed head difference is zero. In rare cases, more than one mathematical solution is found. This situation may only occur if two conditions are met—the overall pump curve contains a droop such that head versus flow is not monotonically decreasing, and the system resistance curve is flat, as when comprised almost exclusively of elevation head loss with minimal friction losses. In general, it is not a good idea to design a pump station with parallel pumps that have a drooping head curve. However, if both these conditions are met and more than one solution exists, then the mathematical solution of flow rate will usually—but not always—converge on whichever value of flow is closest to the initial guess.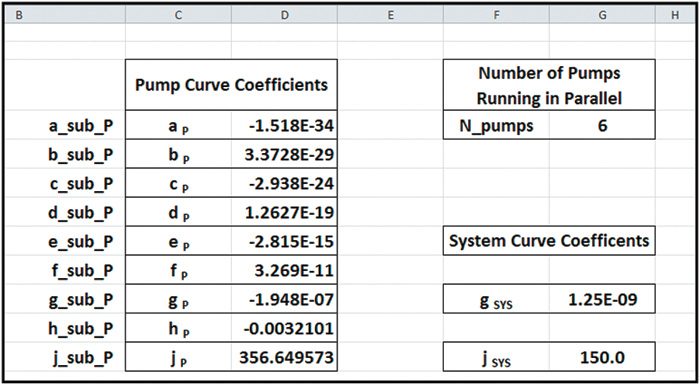
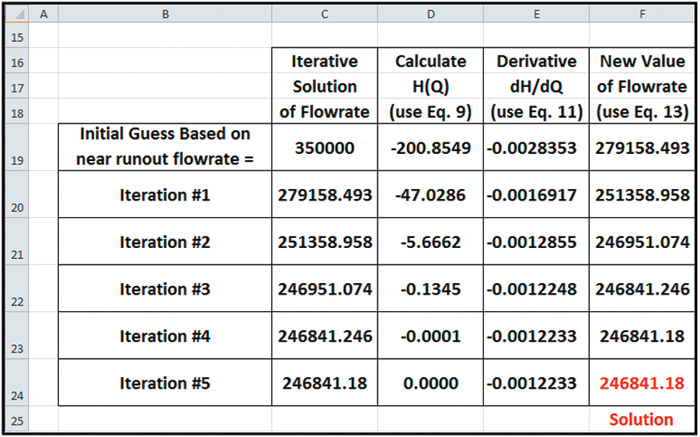
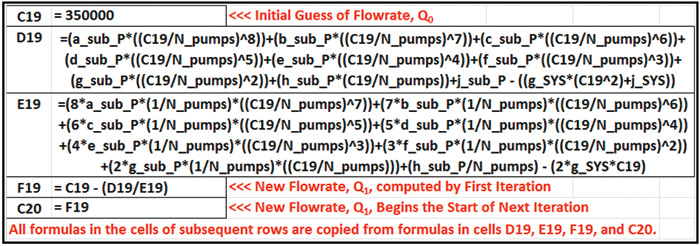
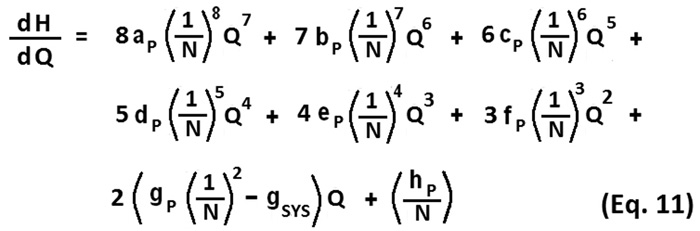

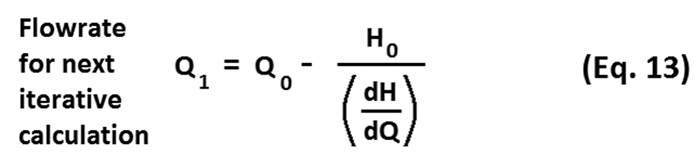