The mechanical seal system, among other features, reduced downtime at the Wisconsin plant.
07/31/2015
For more than 100 years, Wisconsin sand has been prized for industrial applications—including metal casting, construction and consumer products such as iPods. Now, the sand has found new applications in hydraulic fracturing, or fracking. During fracking, pumps open up deep rock formations using a high-pressure mixture of solutions such as sand and water. The sand opens the rock, releasing oil and gas deposits for extraction. White Wisconsin sand works well in hydraulic fracturing applications. The large grains and round shape better open fissures, allowing more successful extraction of fossil fuels.
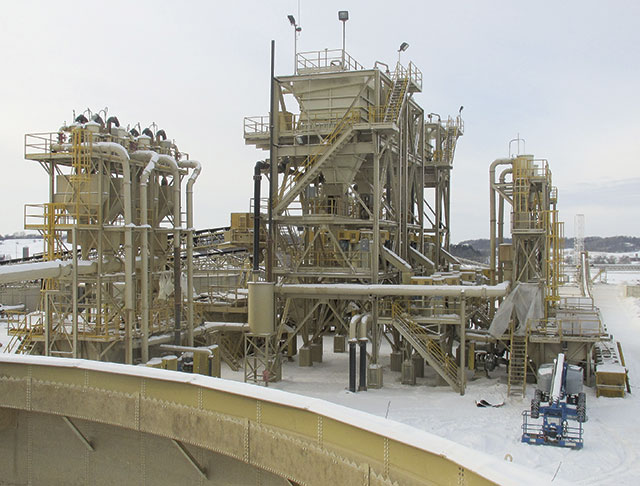
Challenges
A remote Wisconsin sand mine experienced pump deterioration from the abrasive sand. Because of the harsh Midwest winters, the mine only operates from April 1 to Thanksgiving. During operating season, the plant is scheduled to run 24 hours per day to maximize production. Initially, the plant used vertical turbines on the wet side of the process, where the sand was washed, scrubbed of impurities and sized. The wash removes metals and small particles of silica. Afterward, the sand moves to the dry side, where it dehydrates in specific storage areas based on its composition. The sand is inspected and tested after drying. Rail cars transport the sand to frac sites for mixing and injection. The process water is recycled, reducing the plant's costs and water needs. While the process removes the large particles for sale, the fine particles remain suspended in the recycled water. Over time, this microscopic slurry attacks the bronze-fitted vertical turbine. Particle accumulation around the seal leads to failures, and the residue eventually reduces pump flow. The grit forces openings in the rubber bushings, allowing water to escape. Eventually, the turbine shuts down, ceasing all operations. Because of constant operation, the turbines failed frequently as fine particles accumulated quickly. The sand mine incurred major expenses from repairs and lost productivity.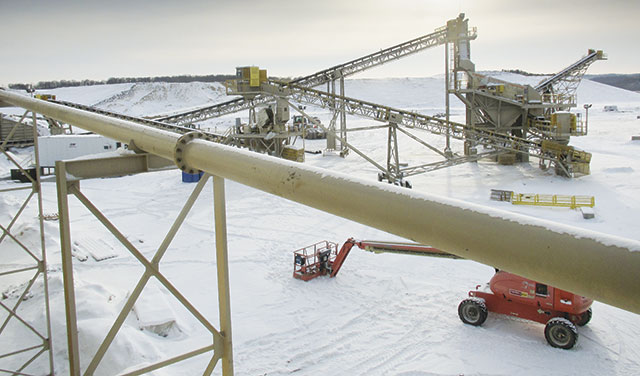
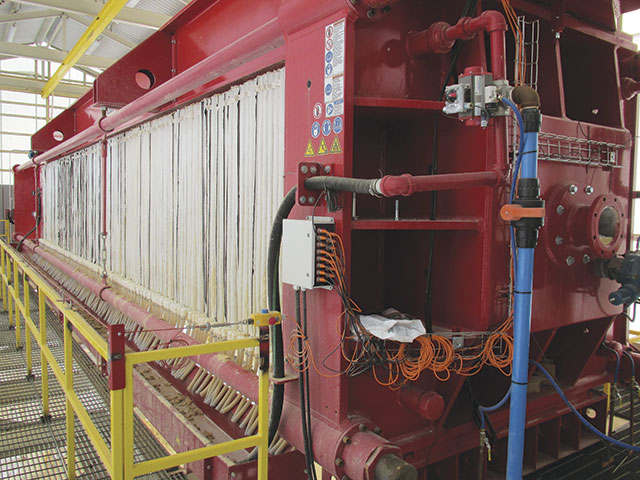