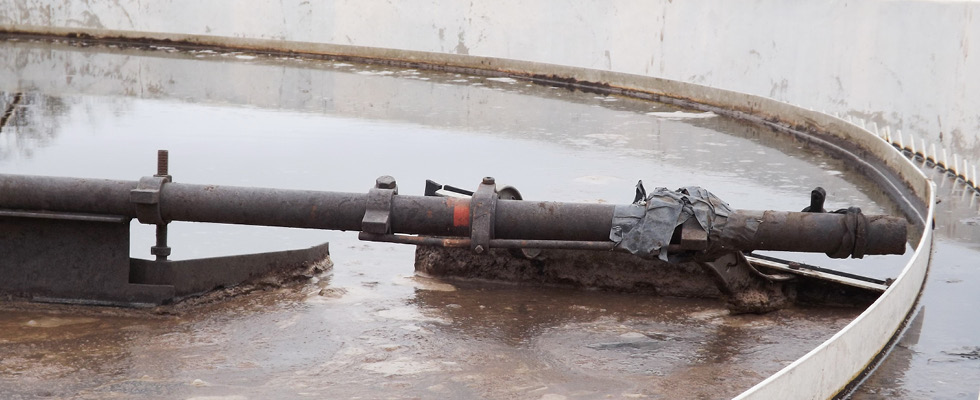
Water + metal + oxygen = corrosion. It is an inevitable natural process, especially in wastewater treatment facilities, that threatens the structural integrity and operating efficiency of equipment. When refined metal is in contact with both air and moisture, the combination oxidizes the refined metal, converting it to a more chemically stable form. Unfortunately, for refined metal, a more chemically stable form means deterioration.
No matter how hard users may try, it is impossible to completely prevent corrosion. It is possible to slow the rate at which metal corrodes by considering relevant external influences such as the water’s pH level, conductivity, oxygen concentration and temperature, which all play a role in corrosion. However, at some point, equipment will corrode beyond repair.
Just because equipment is corroded does not mean it needs to be replaced. Most of the time, corroded equipment can be repaired and retrofitted, returning it to its best operating state and, in some cases, making it better than before. When corrosion strikes, a repair and retrofit service is often more cost effective and efficient than a brand new purchase.
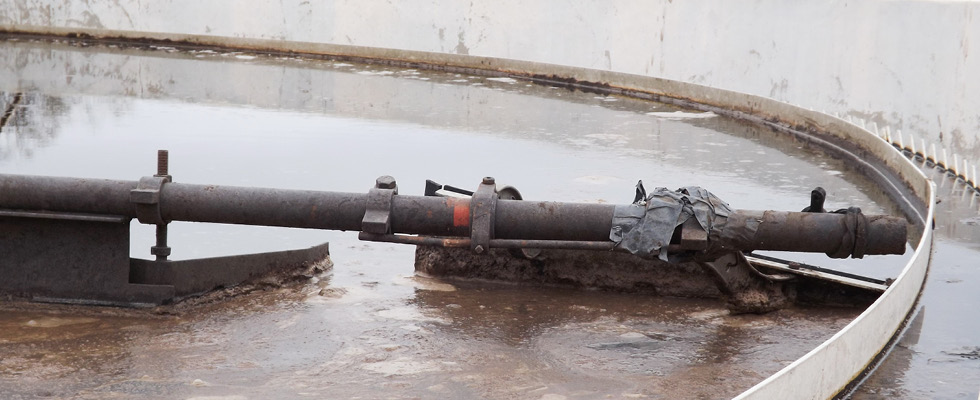
Understanding Corrosion
A common impact on corrosion is the pH level of the water. pH is a measurement of the activity of free hydrogen and hydroxyl ions in a solution and is measured on a scale of 0 to 14. In acidic conditions (a pH level below 7), certain metals like iron, steel and copper are more prone to corrosion. In highly alkaline environments (pH above 7), corrosion can affect materials such as aluminum and some stainless steels.
Weather conditions also influence local pH levels, like in Florida. Florida’s climate is extremely humid and has high water table acidity and high levels of alkali and gases, making projects in the state highly susceptible to rapid corrosion. Knowing the climate and local pH levels can help determine construction protocols. According to experts, wastewater treatment facilities that experience high rates of corrosion should look to install equipment that is manufactured with stainless steel, as opposed to steel, due to its chromium content.
Water conductivity is another important factor that affects corrosion rates. Electrical conductivity, a measure of how well water can conduct electricity, is influenced by the presence of dissolved ions, salts and minerals. In an industry like wastewater treatment, where water has a high concentration of the aforementioned elements, rapid rates of corrosion threaten operation.
When metals are exposed to water with high conductivity, ions can move more freely. Corrosion of metals involves electrochemical processes, where metals lose electrons, leading to oxidation. This process can occur more rapidly in a conductive environment because ions can easily transfer between the metal surface and the surrounding solution.
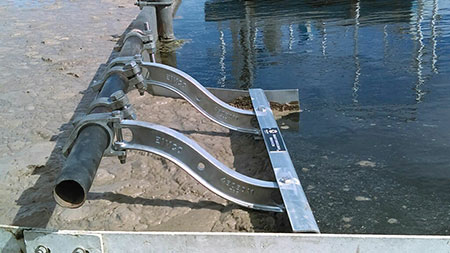
Galvanic Corrosion
Of the many ways corrosion manifests, wastewater treatment facilities are most susceptible to galvanic corrosion. Galvanic corrosion can be defined as corrosion that occurs because of one metal being in electrical contact with another in a conducting corrosive environment. Because wastewater treatment facilities are filled with metal equipment like pumps, valves, drives, skimmers, etc., structural steel treatment tanks serve as prime breeding grounds for corrosion. Although it can manifest anywhere, there are certain parts of the tank that have a higher probability for galvanic corrosion than the rest of the tank.
The highest corrosion risk in any wastewater treatment plant is the point near the top of the clarifier where air and water meet. The combination of constantly moving metal and oxidation rapidly increases the rate of corrosion, and without proper maintenance, clarifiers could fail at a moment’s notice.
To help reduce the rate of corrosion, plant managers should look for clarifiers that are manufactured with corrosion-resistant metals such as stainless steel and aluminum and/or are treated with corrosion-resistant coatings. Another corrosion hot spot is where the skimming device attaches to the metal attached to the feedwell. Again, the constantly moving metal increases the rate of galvanic corrosion and can lead to clarifier failure.
Although corrosion is impossible to prevent, plant operators need to be aware of its effects on operation. Being proactive is imperative, and apathy during routine checks of this equipment can lead to complete plant shutdowns and cost thousands of dollars in fines and repairs.
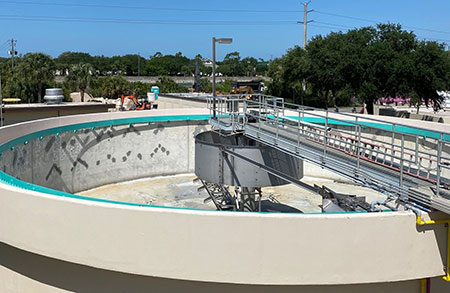
Repair & Retrofitting
Routine maintenance and proper project planning can extend the life span of operational equipment, but unfortunately, proper planning only lasts so long. If an operations manager finds themselves with a faulty piece of equipment or notices the plant is not operating at peak efficiency, they have some options. The first option available is the purchase of new equipment. This can be an easy process, but it is also the most expensive. Because technology has exponentially sped up the process of innovation, there is always a new product that is better and has more features. Although these innovations promise increased efficiency and smoother operation, they can often have the opposite effect on plant operations, as they are not catered to the plant’s unique functions. Additionally, any new technology comes with new problems to solve, and more training is required. The steep cost of new equipment is compounded with the cost of the time and training required to maximize its potential.
Instead of purchasing new equipment, plant operators can turn to repair and retrofit services for a cheaper, and oftentimes more effective, solution to their equipment woes. Retrofitting is more cost effective than buying new equipment and has the potential to make old equipment function even better than before. Through the benefits of corrosion-resistant coatings, increased welding integrity and technology upgrades, these kinds of services can help plants keep their original infrastructure intact, leading to fewer complications and compatibility issues.
Emergency
Sometimes preventative measures are not enough, and corrosion can spell disaster for wastewater treatment facilities. Treatment facilities are essential to community infrastructure, and without them, millions of gallons of water would pollute local water systems. The Environmental Protection Agency (EPA) imposes heavy fines for plants that are shut down for any number of reasons. In November 2023, the city of Lynnwood, Washington, was fined a total of $550,259 by the EPA for shutting down a sewage incinerator. Plant operators and municipalities want to avoid these types of shutdowns, but should an unfortunate circumstance strike, there are companies that can help get plants back up and running in no time.
Comprehending Corrosion
Corrosion poses some of the largest threats to efficient operation in wastewater treatment facilities, and although it is impossible to completely prevent, understanding how it manifests and how to slow its spread can exponentially extend the life span of equipment. When equipment corrodes beyond function, a new purchase is rarely the only option available. To save time, money and energy, plant operators can look to repair and retrofitting services to help revive their equipment.