First of Three Parts
09/02/2015
This series on troubleshooting piping systems draws on past columns in Pumps & Systems discussing the operation of individual components found in piping system. We'll use that knowledge to establish the connection between items with the goal of developing a model of the piping system. We will then see how to use the model to determine if the equipment is operating within the confines of the model, and then compare the model to the physical piping system. This approach can identify and isolate problems within the piping system to arrive at a course of corrective action. Piping systems vary in size and complexity, but the methods presented here can break down even the largest systems to troubleshoot and improve system operation.
The Example System
Figure 1 shows the example system. We will use this example to build the model and then demonstrate a variety of troubleshooting techniques.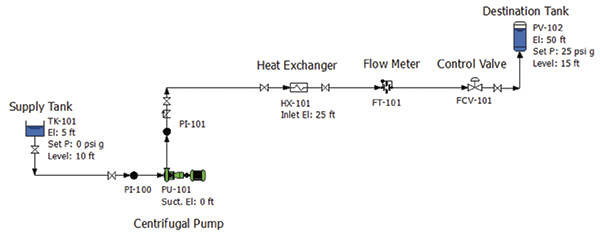
Understanding the Connections
Every piping system consists of three elements: the pump, process and control elements. The pump adds energy to the fluid; process elements make the product or provide the service while control elements improve product or service quality. Working together these elements meet the system's design objectives. The key to understating the interaction between the equipment in the system, as well as its operation, is energy usage. Since we know that energy must be conserved in any system, we can develop an equation for energy usage: hPU = hpg + hC Where: hPU=Pump gain (feet) hpg=Process losses (feet) hC=Control losses (feet) We will use head in feet of fluid as our energy units. Every system must have a known reference for comparing energy measurements so all values are made in reference to a common datum; i.e., 0 feet of elevation in this case.The Pump Elements
A centrifugal pump adds energy to the fluid by converting mechanical from the pump shaft to fluid energy. This is accomplished by converting velocity head to pressure head. The performance of centrifugal pumps is documented by the manufacturer in the form of a pump curve, which shows the pump head developed, and the efficiency in converting mechanical energy to fluid energy as a function of flow rate.1The Process Elements
The process elements consist of the supply tank, interconnecting piping, heat exchanger and destination tank. The supply and destination tanks represent our system's boundary. Since we are starting our system at the supply tank, we must determine the fluid energy content at this point. This is determined by calculating the energy due to the elevation of the liquid surface in the tank (referred to as elevation head), and the energy due to the pressure on the surface of the liquid (referred to as pressure head). The combination of the elevation and pressure head is referred to as the static head. The amount of system energy starts as the static head of the liquid in the supply tank. This calculation is outlined in the Bernoulli equation described in fluid dynamic textbooks. The pipelines transport fluid throughout the system. Due to the friction between the stationary pipe and the moving fluid, and the change in fluid momentum due to valves and fittings, energy is lost in the system. This is referenced in feet of fluid. The energy expended to move the fluid through the pipeline is called dynamic head, because it is a function of the flow rate through the pipe. Calculating head loss in pipelines for Newtonian fluids is performed using the Darcy formula. The heat exchanger's primary system function is heating the process fluid. A heat exchanger has two sides, one for the process fluid and one for the service fluid. Thermal energy is transferred from the hot service fluid to the cold process fluid to meet the process heating requirements. In the example system, the fluid is heated from 60 F to 100 F. A heat exchanger is designed to transfer thermal energy from the service side to the process side, but as far our piping systems is concerned, none of the thermal energy is converted to fluid energy. The process fluid moves through the heat exchanger inlet via a series of small tubes, then out of the heat exchanger. Just like in a pipeline, energy is lost when the fluid moves through the heat exchanger's nozzles, tube sheets and individual tubes. The hydraulic operation of heat exchangers and other process equipment is well understood, and performance data indicating the head loss as a function of the flow rate is supplied by the equipment manufacturer. The outlet system boundary, tank PV-102, is the final process element in our system. The fluid at the destination tank has an energy content that can also be determined using the Bernoulli equation. The static energy at the supply tank differs from the destination tank. This difference is called the system static head. It is calculated by subtracting the fluids static head at the inlet boundary from the static head at the outlet boundary. As long as the level and pressures in the tanks remain constant during system operation, the static head remains constant, regardless of the flow rate through the system. The head loss due to the fluid flowing through the process elements is a function of the flow rate. This is often called dynamic head. The energy used by the process elements is the sum of the system's static head plus the dynamic head for the given flow rate.Control Elements
The control elements consist of the instrumentation and controls used to improve the quality of the product by maintaining a given process parameter (PV) at a set value (SP). The purpose of the control element is to remove any excess energy supplied by the pump elements that is not required by the process elements. The control loop consists of a flow meter (FT-101), a controller that maintains a set process parameter (in our example the flow rate) and the final control element (FCV-101). The flow meter FT-101 uses an orifice device consisting of a metal plate with a concentric hole sized to provide a specific head loss for a given design flow rate. A differential pressure or head loss across the flow meter is required for measurement. The head lost in the flow meter can be calculated by the various meter sizing standards.2 The head loss across a control valve can be calculated based on industry standards as well the American National Standards Institute (ANSI) International Society of Automation (ISA).3 The control loop maintains the set flow rate by regulating the position of the control valve (FCV-101) based on the outlet signal of the control loop.The Math Is Always Correct
The energy added by the pump elements is well understood and documented by various pump performance tests as well as pump and motor standards. The equipment manufacturers test the pumps and motors using the applicable standards and also provide operating data to accurately calculate how efficiently the energy is converted from electrical to mechanical energy. The amount of energy used by the process elements can be determined by calculating the static head and dynamic head using fundamental engineering principles. The head loss associated with process equipment is determined from the manufacturer's supplied test data, especially the head loss vs. flow rate curves. The amount of energy used or lost by the control elements is well documented. Also, flow meters and control valves represent mature technologies that are well documented in industry standards. As a result, motor input power and the associated energy requirements of the pump, process and control elements is well understood. Once this information is inserted into Equation 1 (Page 17), we have a very accurate model of the total piping system. The key to troubleshooting piping systems is comparing the operation of the piping system model with the physical system. We can use this model to calculate how the system should be operating and compare it to how the system is actually operating. To accomplish this we must:- Determine the amount of energy each element in the piping system model should use based upon the system's "as designed" parameters
- Determine the amount of energy each element in the physical system is consuming based on the plant's operation data
Conclusion
We now have an understanding of how the energy flows within a physical piping system. Knowing how energy is being utilized by the various elements of the "as designed" system and then knowing how the energy is actually used in the physical system is the key to troubleshooting how the system is operating. In the next part of this series (read it here), we will discuss how energy is being utilized in a system with installed plant instrumentation. It is often said that most plants do not have sufficient instrumentation to perform these calculations. Much of the necessary information is readily available. You just need to know where to look. As always, feel free to contact me with questions about any of my columns. References- ASME Performance Test Code PTC 8.2 Centrifugal Pump and ANSI/HI 3.6 Rotary Pump Test
- ASME MFC-3 Measurement of Fluid Flow in Pipes Using Orifice, Nozzle, and Venturi
- ISA Standard S75.01 Flow Equations for Sizing Control