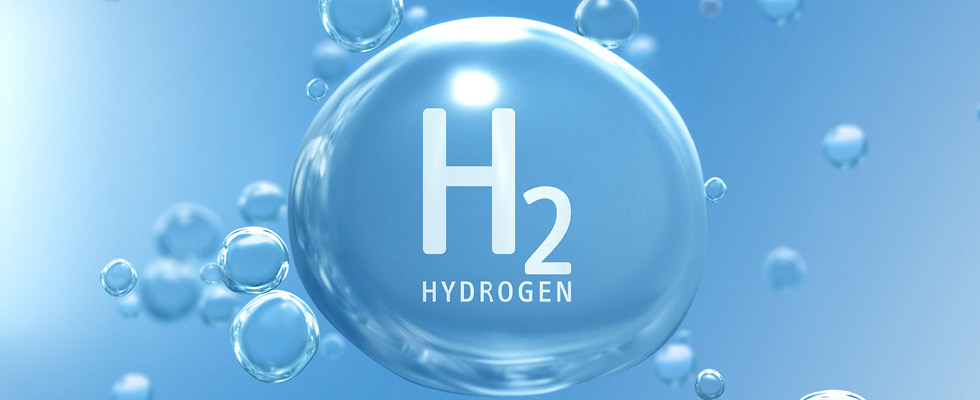
As the world accelerates toward an energy transition, it has become clear hydrogen will play a key role in decarbonizing hard to abate industrial and transportation applications.
Hydrogen is the most abundant element in the universe and, when produced from water by electrolysis using green electricity, is a totally clean energy source. While batteries have the potential to be the new gasoline, hydrogen could well become the next diesel. Unlike carbon-based fuels, hydrogen produces no harmful byproducts upon combustion. Only power, heat and clean water are produced when hydrogen is combined with oxygen in a fuel cell.
As liquid hydrogen is much denser than gaseous hydrogen, it allows for more hydrogen molecules, i.e. energy, to be stored by volume. Pumping liquid hydrogen is also more efficient than compressing gaseous hydrogen for several reasons, the most significant being the reduced energy losses due to density changes during the heat of compression.
However, the gains from using liquid hydrogen do come with their own set of challenges, particularly the energy costs and inefficiencies associated with liquefying the hydrogen in the first place and then turning it back to electricity while maintaining the low temperatures needed to keep the hydrogen in a liquid state.
1. Safety
Liquid hydrogen leaks easily, is inflammable but vaporizes easily and when combined with the oxygen in the air, it ignites easily and burns with a near invisible flame. As gaseous hydrogen is lighter than air, it will rise quickly and disperse and does not pollute the ground or groundwater. Due to the deep cryogenic temperatures (-253 C/-423 F) involved in handling liquid hydrogen, care must be taken to ensure there is no direct skin exposure to any uninsulated equipment. Liquid hydrogen must be stored in well-insulated, double-walled containers to maintain low temperatures and prevent boil-off, reducing the risk of leaks or explosions associated with high-pressure gas storage.
2. Materials
Hydrogen can cause embrittlement in common industrial pump materials like carbon steel, leading to cracking and reduced mechanical integrity over time. As such, it is recommended to use 300 series stainless steels or more noble alloys for liquid hydrogen applications for all the wetted parts. In certain applications, aluminum can be used but requires
special care due to its potential susceptibility to hydrogen embrittlement at high temperatures and pressures. It is important to consult with materials engineers and experts familiar with hydrogen-related challenges when considering both metallic and non-metallic parts for these applications.
3. Rotor Dynamics
Liquid hydrogen is light, with a relative density of only 7% that of water. It has low viscosity and, as a result, low pressure drop across any close clearances within the pump offering limited “Lomakin” support.
Designing centrifugal pump rotors for service in liquid hydrogen presents unique challenges, primarily due to the specific properties of liquid hydrogen. One of the primary concerns is the relatively low stiffness developed in the close clearance seals, commonly referred to as the Lomakin Effect. The Lomakin Effect arises when there is a hydrodynamic force in
the thin film of fluid between the rotor and the stator. In the context of liquid hydrogen, the low viscosity and density of the fluid create high fluid velocity and relatively low-pressure drops, minimizing the Lomakin Effect and making the
rotor more susceptible to vibrations and potential damage.
4. Pump Selections
Low- and medium-pressure applications will most often utilize specially designed single or multistage cryogenic submerged motor pumps like those serving the liquified natural gas industry.
The anticipated release of new modular axial field integral motor pumping systems with individual stage speed control and no axial thrust compensation requirement will offer significant potential benefits as the technology matures. As with any centrifugal pumping application, ensuring operation at or near best efficiency point (BEP) is key to ensure reliability and optimum total cost of ownership.
As liquid hydrogen has such a low mass, it requires pumps to generate high heads to create any significant pressure. In practical terms, this will necessitate positive displacement pumps or high speed multistage centrifugal pumps above approximately 10 bar.
For higher pressures, positive displacement piston pumps specially adapted to seal the ultra-cold cryogenic liquid hydrogen are used. These pumps can be driven by motor/crank or hydraulic actuation.
5. Heat Generation
A primary concern in liquid hydrogen applications is the addition of heat to the fluid and consequential vaporization, leading to boil-off gas losses and higher potential for rotor instability and leakage.
Centrifugal pumps, when used for liquid hydrogen, present thermal challenges. Compared to positive displacement pumps, centrifugal pumps are generally less hydraulically efficient. This reduced efficiency translates to energy being imparted to the hydrogen in the form of heat. Additionally, the compression of the fluid inherently generates heat, elevating the temperature of the liquid hydrogen being pumped.
These thermal effects are cumulative, and given the proximity of operation to the vapor dome, there is a tangible risk of the liquid hydrogen vaporizing. Such vaporization not only introduces rotodynamic instability in the pump, but also impacts the economic viability of the process. The resultant boil-off gas collected and vented represents a loss in efficiency and profitability. As the fluid is compressible, the application engineer will also have to consider the potential increase in temperature through the pump due to the heat of compression.
6. Net Positive Suction Pressure
With its low density, liquid hydrogen has a reluctance to flow into the eye of the first stage or through the suction valve of a reciprocating pump. As such, the application will always require a sufficient net positive suction pressure to ensure reliable operation and no vapor locking. As the fluid is compressible, the application engineer will also have to consider the potential increase in temperature through the pump due to the heat of compression.
7. Sealing
Polytetrafluoroethylene (PTFE) elastomers are used to prevent leaks at joints and static connections. For sliding surfaces, resilient metal seals or specialty seals pre-loaded by metal springs will provide both reliable static and dynamic sealing under cryogenic conditions. At higher pressures, suitably rated cone and thread fittings should be utilized.
8. Testing
Due to the relative lack of equipment experience in new liquid hydrogen pumping applications, it is critical that equipment be thoroughly cryogenically tested for safety, performance and reliability in the liquid hydrogen environment.
Liquid hydrogen can be safely and efficiently pumped to support the growing list of use cases in the ongoing energy transition. Special care and attention need to be taken on pump design, selections, materials, operating conditions and sealing to ensure safe and reliable operation.