Baseplate failures are often difficult to identify in the field but can be correlated to reoccurring performance issues in mounted equipment.
04/27/2016
The success of rotating equipment often can be traced directly to the surface and structure quality on which it is mounted. The useful life of seals and bearings in most process pumps is compromised when shafts are misaligned or excess vibration is present. Some estimate that more than 80 percent of sealed centrifugal pumps are pulled from service for an issue with a mechanical seal or bearing. A solid foundation can increase the mean time between planned maintenance for pumps and most other types of rotating equipment.
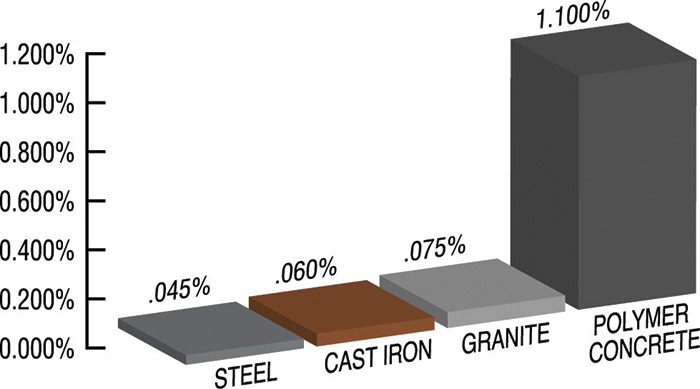
- Mounting surfaces should support the entire pump and driver continually through the operating range of the equipment.
- Baseplates should be stiff enough to resist distortion and deflection and maintain alignment of the pump and motor when installed properly per design.
- Driver and pump mounting-pad surface flatness should be parallel within 0.002 inch per foot (0.15 millimeters [mm] per meter).
- Final alignment should be maintained by allowing up to a 0.125-inch shim pack (3 mm).
- Mounting hole requirements, including size and location, should never present a bolt-bound condition that inhibits final alignment procedures.
.jpg)