The last straw for Larry Krause was when one of his workers fell out of a boat into a 30-million-gallon wastewater lagoon. At the time, Krause was superintendent of a Minnesota food processing plant, responsible for managing the operation's wastewater and solving its odor problem. Like the owners of many facilities, Krause's management team had turned to surface aerators, also known as "splashers." Krause's employee was trying to repair one when he fell out of his boat. "They have their place in certain applications but not in these lagoons," Krause said. "The mixing blades were only stirring the top 6 feet of the lagoon, and the lagoon was twice that deep. We were trying to mix in oxygen, and we were adding deodorants, plus we had a safety issue—guys had to go out in duck boats to repair those splashers, breathing in aerosols and worrying about falling in. It spurred us to find something better." Krause and his colleagues replaced their surface aerators with a recirculation system that used one manufacturer's specialized Venturi injectors and mixing nozzles placed at an optimal depth to solve their odor problem. The injector system uses a fraction of the energy of the old system through the use of shore-mounted pumps and the laws of physics—no blowers or compressors—to maximize efficiency. After retiring from the food business, Krause joined Neil Dornbusch & Associates in New Prague, Minnesota, to promote the injector systems to other lagoon managers.
Injectors Explained
The manufacturer's specialized Venturi injector utilizes the physics of fluids with no moving parts. When pressurized water enters the injector inlet, it is constricted toward the injection chamber and changes into a high-velocity jet stream. The increase in velocity through the injection chamber results in a decrease in absolute pressure, creating a vacuum and enabling air to be drawn through the suction port and entrained into the water stream.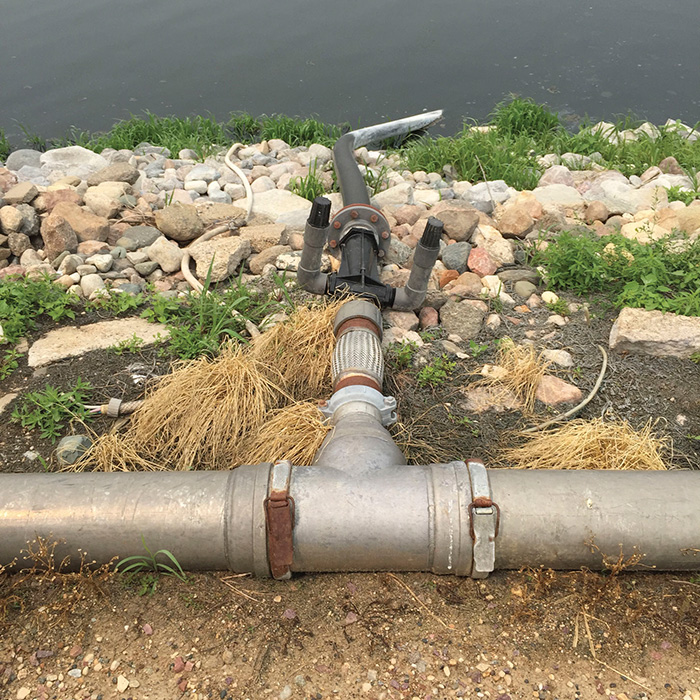
Nozzle Positioning
Optimal positioning of the mixing nozzles at the bottom of the lagoon does more than put additional wastewater in the path of oxygen. It takes advantage of the fact that oxygen transfer occurs more effectively under higher pressure—exactly the conditions found beneath 30 million gallons of liquid. That positioning neatly addresses one of the major challenges that surface aerators face. "They're wasting a lot of their energy up at the surface, where the solubility potential is a lot lower," one of the manufacturer's representatives said. "And because gas naturally tends to float upward in water, it's difficult for surface aerators to push oxygen lower into the lagoon." Energy savings is one major benefit of a Venturi injector system, Krause said. Converting to an injector system reduced one user's energy bills by more than 30 percent. They replaced 16 surface aerators and simplified maintenance dramatically. "The only moving part is the pump," he added.Close Collaboration
Designing an injector system for a wastewater lagoon is a team effort that taps the skills and experience of the end user, a local engineering firm, pump suppliers and the manufacturer's in-house engineering team.
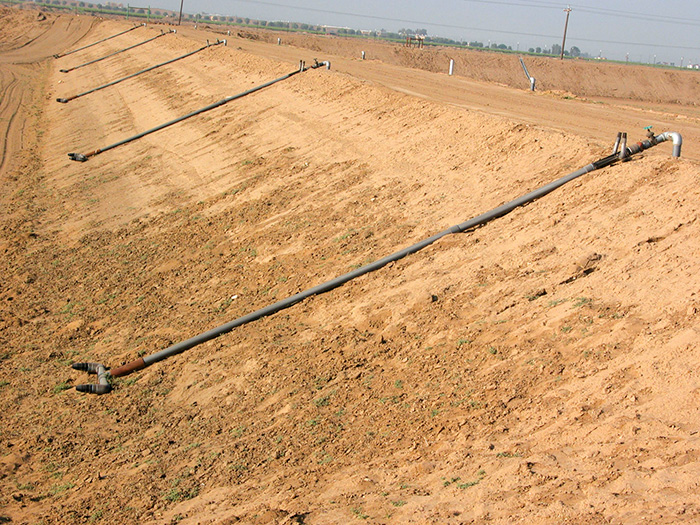
