11/22/2013
Q. What information is available regarding NPIPA and NPIPR for rotary pumps? A. Net positive inlet pressure available (NPIPA) is the algebraic sum of the inlet and barometric pressure minus the vapor pressure of the liquid at the inlet temperature: [Equation 1]
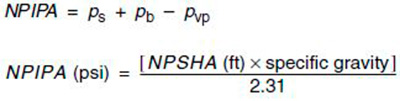

- A 5-percent reduction in output rate of flow at constant differential pressure and speed
- A 5-percent reduction in power consumption at constant differential pressure and speed
- The inability to maintain a stable differential pressure and speed
- The onset of loud or erratic noise when this criterion is previously agreed upon by all parties
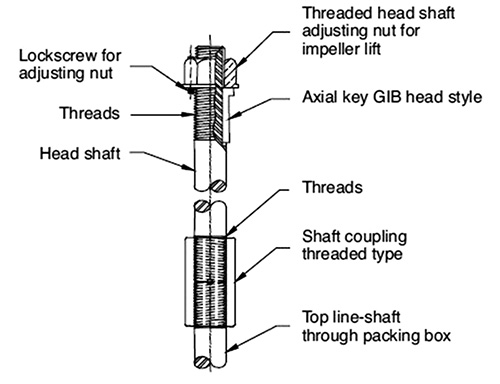