Methane (CH4) is the second largest source of greenhouse gas emitted in the U.S. In 2013, CH4 accounted for about 10 percent of all U.S. greenhouse gas emissions from human activities. Methane's half-life in the atmosphere is much shorter than that of carbon dioxide (CO2); however, it is significantly more efficient at trapping radiation. Pound for pound, the comparative impact of CH4 on climate change is 25 times greater than that of CO2 during a 100-year period. One area responsible for contributing to the increase in CH4 is leaking equipment in the oil and gas sector. A major contributor to this leakage is valves that leak CH4 and sub-derivatives called volatile organic compounds (VOC) from the gland. During the last 30 years, governmental agencies have worked with industry leaders to address these leaks by increasing the implementation of new technology. This focus has prompted packing manufacturers to ramp up research and development of new materials. State and federal agencies have also tightened standards for maximum leak rate measurements of VOC values from 10,000 parts per million (ppm) 20 years ago to 100 ppm in most places in the U.S. today. As a comparison, that is like changing the Corporate Average Fuel Economy (CAFE) limits for miles per gallon (mpg) of automobiles from 1990 levels of 27.5 to 2,750 mpg. One of the main challenges the industry needed to overcome was the lack of a unified testing standard. Twenty-five years ago, many refineries and packing manufacturers used their own testing standards with varying media (nitrogen, helium or methane at different concentrations), temperature ranges and thermal cycles. These variations made it difficult to compare the effectiveness of valve emission packing. A few standard organizations created tests for valve emissions addressing this issue. The American Petroleum Institute (API) was one organization that specifically focused on a detailed testing procedure for packing performance in methane. The standard, API 622, has become a benchmark for packing performance in the U.S. for a variety of reasons, including the Environmental Protection Agency's (EPA) insistence that packing performance testing be conducted using methane instead of other gases. This standard became the catalyst for research and development efforts to create valve packing that could meet a less than 100 ppm requirement. Using methane as a test gas, API 622 requires five thermal cycles from ambient temperature to 260 degrees C (500 F) with 1,510 mechanical cycles. Thermal cycles are completed once per day and are divided into 300 mechanical cycles (150 at ambient and 150 at 260 C). A final 10 mechanical cycles are completed at ambient temperature, where the final leakage measurement is taken. This test requires a large number of mechanical and thermal cycles and is designed to challenge packing manufacturers to improve development. At the 2015 ISA Leak Detection and Repair (LDAR) Symposium, a paper by Buzz Harris from Sage Environmental focused on emission factors of leakage in refineries. His main focus was comparing testing data from API 622 to current common limits. He concluded that, in refining gas and vapor service, the emission factor would be reduced from 2.6 x 10-2 to 1.0 x 10-5 kg/hour/source—a decrease of more than a 1,000 times. One important point is that API 622 is not a valve test but a packing test. It would be a mistake to assume that all valves will exhibit the same performance with the same packing. This is because all valves have their own unique design characteristics that affect overall sealing, primarily tolerances and unique valve design features. As a result, API created a testing protocol—API 624—that focused on emissions capability by valve design and valve manufacturer (see Image 1).
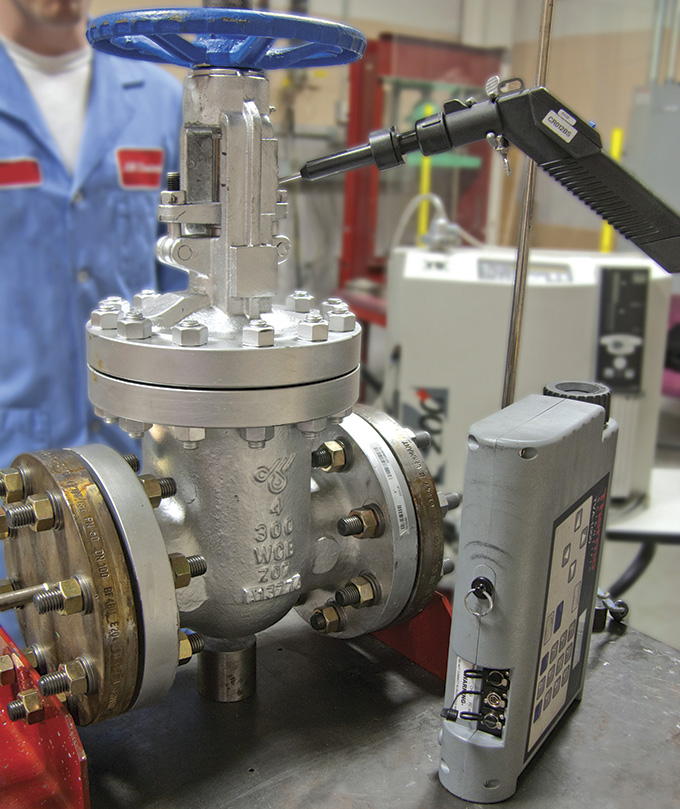
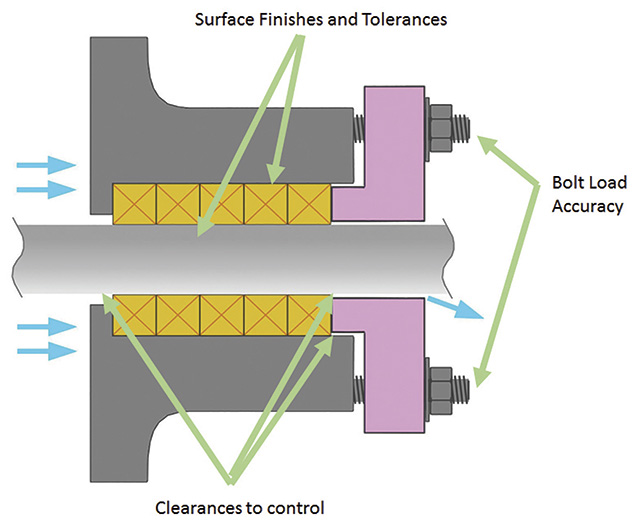