The purpose of using a torque wrench is to apply the target load for a specific amount of stress on a gasket. For any given combination of gasket, bolt and flange, a stress range will ensure that the gasket will seal while, at the same time, protecting from over tightening that may cause damage to one of these components. Failure to remain within this stress range may result in environmental concerns, safety issues and downtime that can be expensive and dangerous. Understanding the types of torque wrenches, their advantages and how to maintain them will help operators apply the correct stress to gaskets. Specific guidance on a torque wrench’s use can be found in ASME PCC-1-2013. This “Sealing Sense” discusses some commonly used torque wrenches, their capabilities and their maintenance.
Types of Torque Wrenches
A torque wrench is a precision instrument designed to develop a specific amount of axial force within a fastener. Like a spring, the fastener needs to be elongated or stretched a known amount corresponding to a specific force. The axial force stretches the bolts, and the resultant force from this stretch clamps the flanges against the gasket. The amount of stretch is determined by the amount of torque applied to the bolts. The torque must not be too much or too little so proper load is achieved while protecting the other components of the bolted flange joint. It sounds simple. However, several important considerations must be kept in mind to ensure safety and the accuracy of the torque wrench.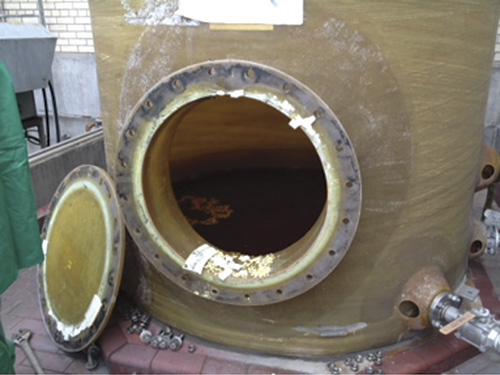
Beam
A beam torque wrench is the most basic, reliable and least expensive type. One advantage is that it can measure how much torque is needed to loosen a bolt. A disadvantage to this model is it can be difficult to use in tight spaces where it might not be possible to see the pointer needle.Clicker
The clicker style torque wrench is the most commonly used, with a typical accuracy level of +/-4 percent to +/-6 percent. To adjust the torque setting, the handle is unlocked and turned to set the scale on the handle with the scale on the shaft. The click sound indicates that the torque setting has been reached and enables the use of the wrench if the scale is not visible. The main disadvantage of a clicker torque wrench is that it can be sensitive to the shock of being dropped, and the spring must be reset to the lowest torque setting after each use. Another disadvantage is that it can take extra time and effort to turn the graduated handle because it requires working against the pressure of the main spring. It can be tiring to set it to a high torque because of working against a heavy spring within the handle.Electronic
An electronic torque wrench is similar to the clicker. However, it provides an electronic readout or torque selection. A major disadvantage to the electronic torque wrench is the higher cost. Instead of a click, a light or beep is used to indicate that the torque has been reached.Other Considerations
It is important to follow acceptable maintenance and use practices when using any torque wrench. These include: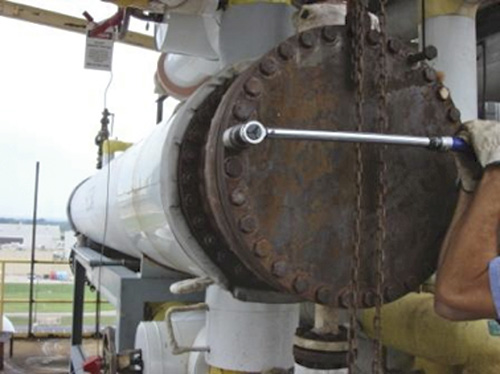
- Safety glasses should be worn at all times when using any hand tool.
- Do not exceed the recommended working range of the torque wrench. In general, most wrenches have a usable range from 20 percent to 100 percent of full scale.
- Do not use handle extensions, such as a pipe fitted over the wrenches handle.
- Torque losses occur when using socket extensions or crows foot attachments. The typical rule is to increase the torque by 10 percent to account for these losses.
- Dropping a torque wrench on a hard surface can cause the instrument to lose calibration. After 5,000 cycles or up to one year of use, the torque wrench should be inspected and recalibrated by the manufacturer or a reputable calibration service.
- If using a clicker torque wrench, always store it at the lowest level on the scale.
- Use a torque wrench to apply the specific torque value during the final assembly process.
- Do not use a torque wrench to loosen fasteners.