The custom solution reduces supply and maintenance costs and provides a consistent feedwater supply.
04/04/2016
The oil and gas business has always been a water business, with water-oil ratios averaging 8-to-1. Oil and gas operations consume 82 billion barrels (bbls) of water and produce more than 2.5 billion bbls of polluted wastewater each year. That is 1,300 times the City of San Francisco’s annual water use. With water management becoming an ever-larger proportion of industrial operations, oil and gas operators are beginning to look for advanced wastewater treatment technologies that can mitigate this cost center. Across the U.S., three key pressures are driving these upgrades.
- Aging infrastructure and regulations. Without proper infrastructure, industries cannot efficiently perform at scale. According to the U.S. Environmental Protection Agency (EPA), there is a $500 billion gap in water investment in the U.S. alone. Environmental concerns also drive strict water disposal regulations to protect natural resources, which can add stress to complicated water treatment protocols. Many facilities that had previously used internal wastewater treatment systems now struggle to keep pace. As water use is more closely tracked and increasingly strict wastewater regulations are created, many oil and gas facilities are looking to update their treatment systems.
- Regional water pressure. Extreme drought is affecting residential and industrial water use in several regions, especially California where new standards are cropping up to better manage water across the value chain. For example, Senate Bill 1281, passed in 2015, requires all oil and gas operators to provide a monthly water use statement to the state board for approval. To add to the complexity of efficiently managing industrial processes, falling oil prices are leading to tighter budgets across the oil and gas industry. As legislation continues to change and oil prices continue to drop, operators are searching for an environmentally friendly water treatment alternative that won’t break the bank.
- Lack of in-house resources. Purchasing a water treatment facility or equipment requires a substantial investment of time and resources, and many refineries are no longer hiring dedicated in-house water managers. Companies must find the resources to complete water analyses, technology evaluation, scope development, vendor evaluation, capital budgeting, and proposal requests and evaluation. They must then perform final design work, equipment fabrication, environmental permitting, field installation and process optimization—work that detracts from their core operations. Outsourcing can take care of those tasks in a comparatively short time span.
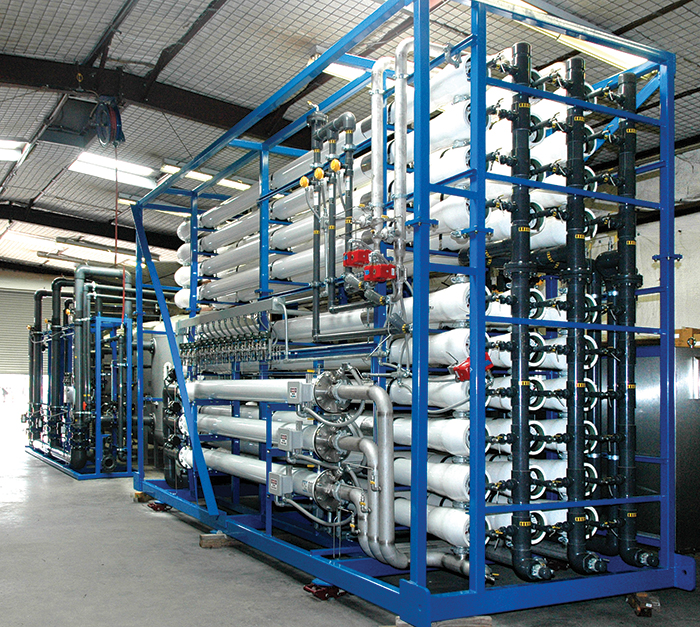