Energy is a strategic input for the mining industry in Latin America and worldwide. Mining requires large amounts of energy, which drives up total operational costs. In Chile, mining companies consume 34 percent of the total energy produced in the country and spend approximately 20 percent of their total income on electricity costs. According to official mining sources, the copper mining industry is expected to consume 41.1 terawatt-hours (TWh) in 2025, an increase of 95.5 percent from 2013. New projects alone will consume 36.2 percent by 2025. The world’s biggest copper companies use concentration plants—which are energy intensive and use the world’s biggest pumps—as their main production process. In 2013, concentration plants represented 48.6 percent of the total energy consumption for the copper mining industry, which is expected to increase to 64.2 percent by 2025, reaching 26.4 TWh. Water is another major concern in the mining industry. Freshwater restrictions from scarcity or government policy will have an impact on water availability for future mining projects. Because of these restrictions, desalination plants and seawater pumping systems are also expected to reach 6.2 TWh, representing up to 15 percent of the industry’s total energy consumption.
Pump Stations
Several studies have shown that pumps account for approximately 25 to 32 percent of total motor energy consumption on an average industrial site. Governments from different mining countries are considering applying strict energy efficiency policies to mining companies. These policies will seek significant reductions in carbon emissions and immediate optimizations (up to 10 percent in Chile, the world’s largest copper producer). In recent years, motor manufacturers have accomplished great results regarding energy efficiency, up to 96 percent. However, this has not been the case for the pump industry. In this new energy-efficient and carbon-reduction scenario, pump designers and manufacturers will play a key role in delivering highly efficient pumps. Energy represents up to 90 percent of a pump’s life cycle cost, making pumps and pump stations a huge opportunity to improve energy efficiency and reduce carbon dioxide emissions in the mining industry.Vertical Turbine Pumps
Vertical turbine pumps (VTP) are some of the most versatile and reliable pump designs in the turbomachinery industry. Their minimal space requirement, highly efficient semi-axial design and pro-gravity vertical arrangement have made this type pump popular in several industries, particularly mining because of their compact size and ease of maintenance. In recent years, engineering and design capabilities have improved through mechanical and hydraulic simulation software, advanced manufacturing technologies such as three-dimensional (3-D) printing and computer numerical control (CNC) machining as well as the extensive use of special metallurgies. These changes have allowed pump manufacturers to take this pump type to a new level. Engineers can custom design vertical turbine pumps, such as high-head/capacity pumps or pumps for the transportation of highly corrosive and abrasive fluids for heavy-duty applications, while maintaining the design’s highly efficient characteristics and operational advantages.Energy-Efficient Pump Design
Hoping to increase its production, one copper producer decided to double its concentration plant’s reclaim water pumping capacity. However, the water quality was a challenge for most pump manufacturers. The water had a high solids content concentration, about 20 percent, and high concentrations of chlorides, about 60,000 milligrams per liter (mg/L). The company’s previous pumping station consisted of 10 standard short-set vertical turbine pumps with a capacity of 1,500 cubic meters per hour (m3/h) and a total dynamic head of 80 meters (m). Each cast-iron pump had efficiencies below 80 percent. This pump configuration was a poor fit for this highly corrosive and abrasive application, requiring operators to repair and replace these pumps every three to five months. Assisted by computational fluid dynamics (CFD) and finite element analysis (FEA), a pump manufacturer custom designed a vertical turbine pump that met all the requirements for this abrasive service (see Image 1).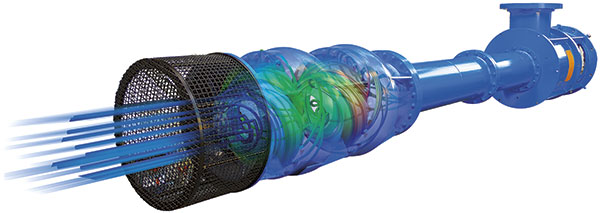
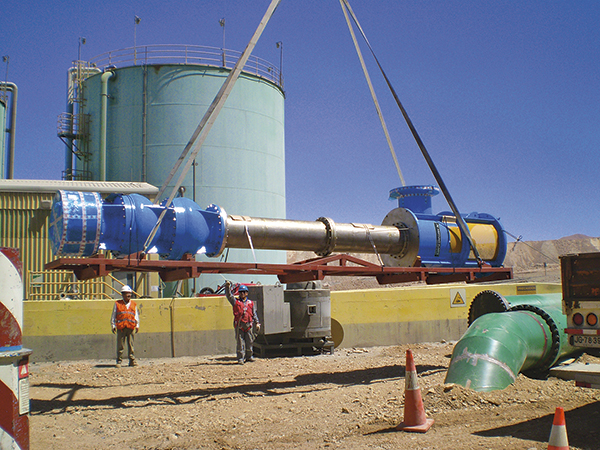
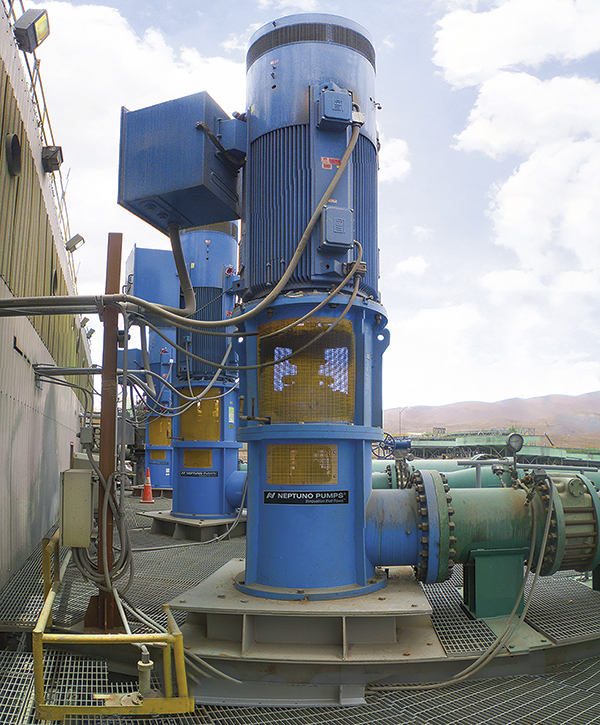