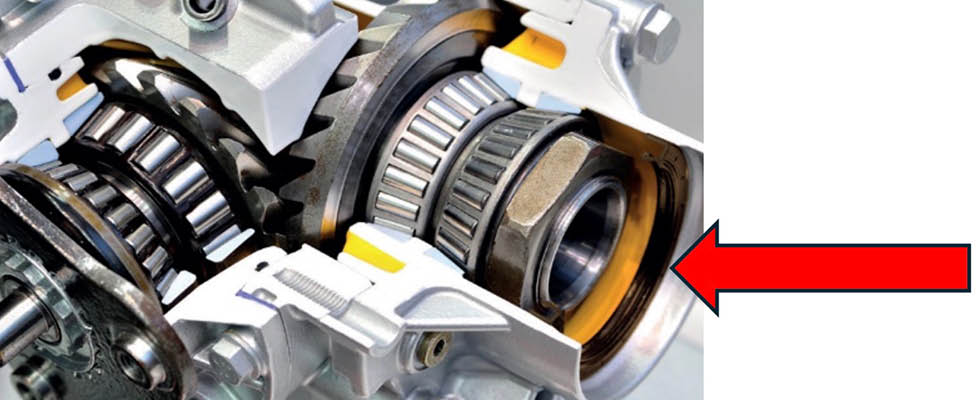
Sealing technology has evolved significantly since its development in the late 1800s. Selecting the correct seal design and material is crucial in ensuring operational efficiency while minimizing the risk of equipment failure and costly downtime. This cannot be emphasized enough and is especially true for equipment operators in critical, heavily regulated industries such as food and beverage processing, oil and gas and semiconductor manufacturing, where seals help keep machines running in increasingly aggressive operating environments.
There are several factors to consider when choosing a seal, depending on the industry, application and environment. This article will take a closer look at three major factors to consider when evaluating the right seal for critical applications: material, temperature and pressure.
Material
Seals are manufactured from varied materials including nitrile, silicone, chloroprene, thermoplastic and polyethylene. If the materials in the seal are incompatible with the seal’s application, it can rapidly deteriorate, so understanding a material’s strengths and weaknesses is key. For example, a current choice for demanding applications are perfluoroelastomers (FFKM, by American Society for Testing and Materials [ASTM] 1418 standard), a family of chemical- and heat-resistant elastomers that combine the chemical resistance of polytetrafluoroethylene (PTFE) with the flexibility and elasticity of standard fluorocarbon elastomers (FKM). FFKM were born out of necessity, and they are widely used across many industrial processes. FFKM are fully fluorinated and therefore contain higher amounts of fluorine than standard FKM, resulting in higher temperature ratings (up to approximately 325 C/617 F) and improved chemical resistance with nearly universal chemical compatibility.
Temperature
It is important to consider the temperature a seal will be exposed to when selecting one for an application. Temperature can significantly impact performance. Advancements in major industries, such as new processes, chemicals and more, have led to the use of new equipment, changing requirements and new operating temperature ranges. Seals must withstand wider temperature ranges than they have in the past, especially in extremely cold environments. If the operating temperature is too cold, the seal will lose its elasticity and become more brittle, making breakage likely. Conversely, if a seal gets too hot, it can become too flexible, leading to degradation. Identifying the temperature range of the prospective application will help in choosing the right seal.
Pressure
Seals are generally designed to hold pressures up to 1,500 pounds per square inch (psi). It is essential to know what pressure the seal for an application will be required to hold, as this pressure directly affects the hardware geometry requirements and the type of elastomer the seal will be manufactured in. Some compounds have been designed specifically to handle extremely high pressure, extremely low pressure and rapid change in pressure. When choosing a seal for an application, it is important to ensure it can handle the pressure it will be subjected to.
Real-World Applications
It should now be evident that choosing the right seal is critical to ensure the proper function and application success. Next, this article will take a look at the oil and gas and food and beverage industries as real-world examples of why the seal evaluation process is crucial for operational success.
Oil and gas
Sealing solutions play a critical role in various applications within the oil and gas industry, ensuring equipment and operations’ integrity, safety and efficiency. From exploration and production to refining and transportation, the harsh and demanding environments present challenges that require reliable sealing solutions.
In the exploration and production phase, sealing technology is employed in wellheads, valves, pumps and other equipment to prevent leakage of fluids such as oil, gas and drilling mud. These seals must withstand high pressures, extreme temperatures, corrosive fluids and abrasive contaminants commonly found in downhole environments.
During refining processes, seals are utilized in pipelines, reactors, distillation towers and storage tanks to contain hazardous chemicals, prevent leaks and maintain optimal operating conditions. The seals must resist exposure to aggressive chemicals, high temperatures and mechanical stresses associated with refining operations.
Seals are essential for maintaining the integrity of pipelines, valves and fittings, ensuring safe and efficient oil and gas transport over long distances. These seals must withstand environmental factors such as temperature fluctuations, vibration and external pressures while preventing fugitive emissions and minimizing the risk of accidents, thus ensuring safe and long-lasting operations. Overall, the successful application of sealing technology in the oil and gas industry requires innovative designs, high-performance materials, rigorous testing and adherence to strict safety and environmental standards. By addressing these challenges, sealing solutions contribute to the reliability, sustainability and profitability of oil and gas operations worldwide.
Typical applications include completion tools, drilling and wireline tools, valves, pumps, compressors, process instrumentation, packing systems, mechanical seals and downhole drilling tools.
Food and beverage processing
Every phase of converting raw goods into finished, consumable products in the food and beverage processing industry uses diverse machinery. This sector faces a series of considerable challenges in sealing.
- Extreme temperature ranges: O-Rings and seals used in the industry must withstand significant temperature variations. Sealing integrity and durability must be maintained from the icy cold storage conditions to the intense heat of cooking and sterilization processes.
- Chemical resistance: Cleaning agents and chemicals are frequently used to maintain hygiene in food processing environments. Consequently, seals must display high chemical resistance to prevent degradation that could lead to leaks and potential product contamination.
- Wear and abrasion resistance: The constant mechanical movements inherent to the operation of processing machinery demand seals with excellent wear and abrasion resistance. High-pressure techniques also contribute to the stress placed on these critical components.
- Food safety regulations: All seals used within food processing must be food-grade and non-toxic and must comply with rigorous food safety regulations. Compliance ensures the health and safety of consumers and protects manufacturers from potential legal issues related to food safety.
Sealing technologies and solutions are critical to operating performance and can have a significant impact on success. Partnering with an experienced seal manufacturer and/or distributor can help ensure the best sealing material.