Pumps operating in harsh conditions will come under attack from many influences that can threaten a system's performance and service life. The good news is that advances in design engineering and high-performance materials offer viable defenses that can optimize uptime and productivity. Among the more extreme examples of harsh applications in the world of industrial pumps, cryogenic pumps that handle various liquefied gases can be subjected to temperatures as low as minus 250 C, particles in the gases, high rotational speeds, elevated vibration and stray electrical currents—all of which are problematic without safeguards. As another industry example, slurry pumps are often exposed to severe abrasives, which can result in wear and damage to a pump's impeller and cause imbalance that will affect other components. Across industries, pumps are put to the test every day unless operating conditions are offset with technologies to withstand assault. Manufacturers and suppliers have made significant strides to provide robust bearing and seal technologies designed to keep pumps up and running as intended without interruption.
Bearing Down on the Challenges
In general, pump bearings support hydraulic loads imposed on the impeller, the mass of the impeller and shaft, and loads caused by couplings and drive systems. They additionally keep axial and radial deflections of shafts within acceptable limits for the impeller and shaft seal. But when severe operating conditions arise, standard bearings can become targets and casualties. Using cryogenic pumps as an example, bearing service life often is less than six months because of attacks on the bearing arrangement. When bearings fail, overhaul and repair operations for a pump can be expensive and even dangerous. Specially engineered cryogenic pump bearings represent one solution. Compared with standard bearings, cryogenic pump bearings benefit materially from specially heat-treated stainless steel, which delivers improved protection against corrosion, wear and fatigue. The bearings integrate low-friction ceramic rolling elements, while the silicon nitride ceramic material prevents electrical erosion by insulating against stray currents and resists surface fatigue, even under the poor lubrication conditions inherent to cryogenic pumps. Cryogenic pump bearings are designed with single-piece, glass, fiber-reinforced polyetheretherketone (PEEK) cages. Unlike conventional rigid and riveted steel and brass or polymer counterparts, a PEEK cage allows liquefied gases in cryogenic applications to flow easily through the bearing. At the same time, the cage will flex away from the dynamic movements of the bearing\'92s rolling elements to help improve operational efficiency. A large petrochemical plant was experiencing repeated bearing failures with its cryogenic pumps. The pumps with high revolutions per minute (rpms) were submerged in and used to pump minus 100 C liquid ethylene through start-stop cycles around the clock. Issues involving the extremely low temperature of the liquid, ingress of contaminants, cycling, lubrication and other factors were combining to cause severe damage to bearing components, leading inevitably to their failure. With a need to increase pump reliability and eliminate expensive maintenance in the high-risk areas of the plant where the pumps were located, operators equipped the pumps with high-performance cryogenic pump bearings that would mitigate the ongoing risk factors. After more than two years in service, the bearings continue to perform well with no signs of damage. Today, the projected realistic service life of the newly installed bearings is at least three years, compared with less than six months for standard bearing counterparts. Thrust-taking bearings in American National Standards Institute (ANSI) style pumps also routinely face threats to performance. High loads and poor lubrication can result in higher bearing temperature, lubricant degradation and, consequently, premature bearing failure. In response to these common threats, a special family of double-row angular contact ball bearings has been engineered to deal with the extreme conditions and serve as complements to conventional double-row angular contact ball bearings typically specified to perform as thrust-taking bearings in ANSI-style pumps (and some older American Petroleum Institute [API] style pumps). Design innovations integrated into this special family of bearings include machined brass cages, which can withstand extremely high temperatures, poor lubrication conditions and rough operation more effectively than conventional plastic or pressed-steel cages. Steeper 40-degree contact angles impart increased thrust capacity. Reduced axial internal clearances promote load sharing between the two rows of balls and a reduced possibility of unloading the inactive ball set. Annular Bearing Engineering Committee (ABEC)-3 (P6) tolerances promote smoother and cooler bearing operation. All these improvements increase ruggedness.Sealing the Deal
Bearings are not the only precision components in the crosshairs when harsh conditions take aim. Effective sealing of pumps and systems is essential. Otherwise, contaminants can invade lubricant and inflict damage on bearings and the system and have catastrophic results.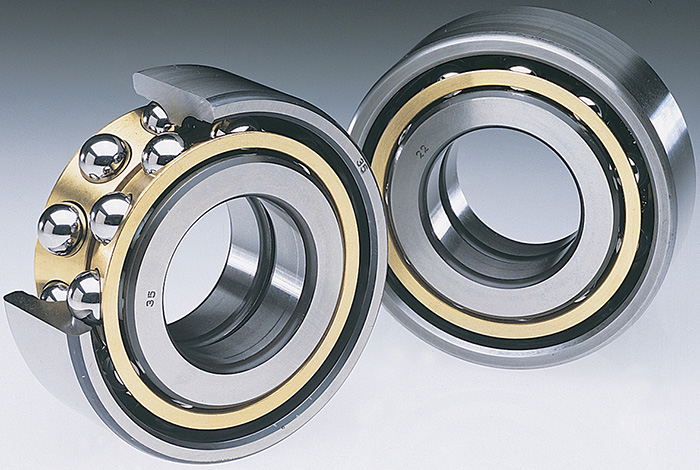