HI Pump FAQs
Hydraulic Institute
09/16/2016
Q. What mechanical seal designs are recommended for wastewater application pumps? A.In wastewater, two seal arrangements are commonly used: single seal and dual-pressurized (double) seal. Single seal designs, shown in Figure C.2, are normally either a stationary pusher seal with the springs isolated from the process fluid or a rotating elastomeric bellows seal with a large single coil spring wetted by the product.
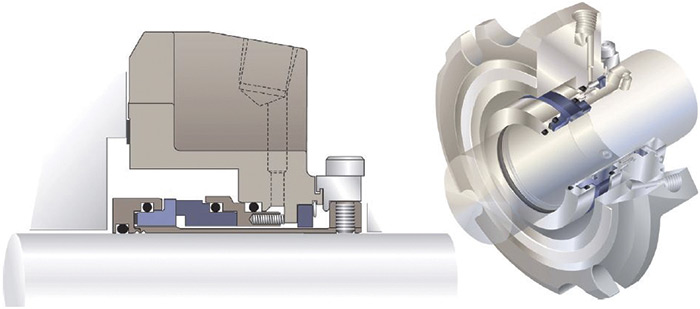
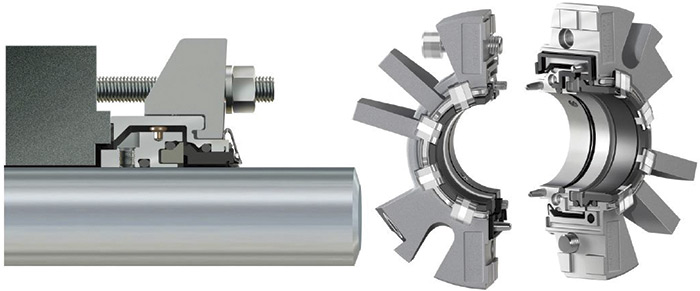
- They are hydraulically balanced and provide maximum interchangeability in pumps and other equipment without equipment modification.
- They eliminate sleeve wear and minimize power consumption compared with packing.
- They have a wide operating window, from vacuum to positive pressure.
- They can be installed without sleeve or shaft replacement, even if the pump was previously packed.
- The springs are typically a nonclogging design or are located outside the process fluid, which prevents them from clogging.
- They eliminate excessive leakages that lead to bearing failures and corrosion issues.
- Large pumps benefit from split seals by saving equipment teardown for initial installation or seal replacement.
- They reduce maintenance and operating costs for large pumps through reduced flush requirements and repair costs.
- While the initial cost of split seals can be slightly higher than nonsplit component or cartridge seals, the overall life-cycle costs (LCC) can be less. The savings associated with split seals are achieved by not having to remove the pump or realign the equipment for seal repair.
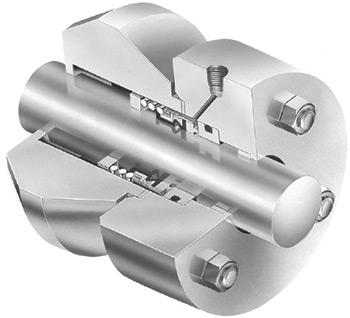
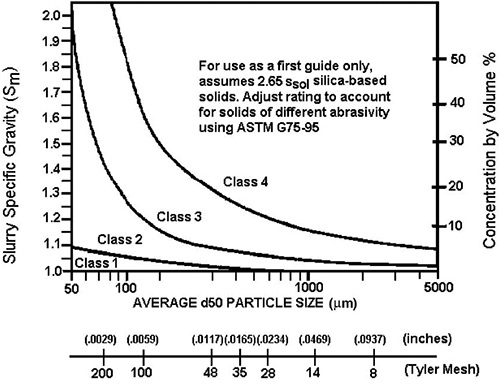
See other HI Pump FAQs articles here.