Inspect compression surfaces thoroughly to help ensure leak-free repairs.
06/27/2014
A leak rate of one drip per minute equals about a liter (quart) of water in three days. For an O-ring on a submersible pump, that is a major problem. O-rings are often used for static seals on submersible pumps. Understanding what makes a good static seal and what causes one to leak is important for pump maintenance and repair technicians. The effectiveness of an O-ring static seal depends on the dimensions of the mating parts, the surface finish of the mating parts and the characteristics of the elastomeric O-ring. The focus of this article is the dimensions and condition of the mating parts.
Dimensions
The dimensions (geometry) of the mating parts are important for achieving a good O-ring seal and will not change unless the surfaces have been corroded, damaged or machined. The radial mounting’s inside diameter (ID), for instance, will be slightly larger than the O-ring’s ID. Therefore, the O-ring will be subjected to a slight stretch when slipped into the mounting groove. To form a leak-free static seal, the O-ring should be compressed about 40 percent by the mating parts. The amount of compression is a function of the mounting groove’s depth (GD) and the O-ring’s cross-sectional diameter (OCD). The width of the mounting groove (GW) must allow the O-ring to expand in that dimension while it is being compressed in the depth dimension (see Figure 1).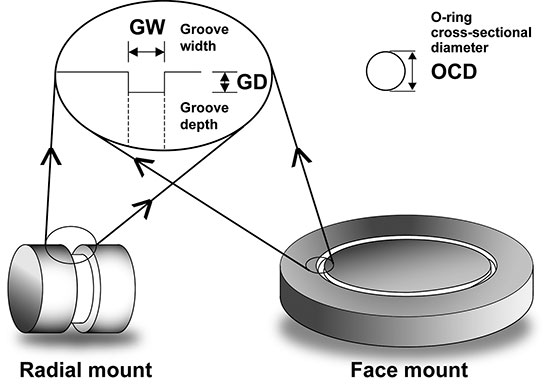
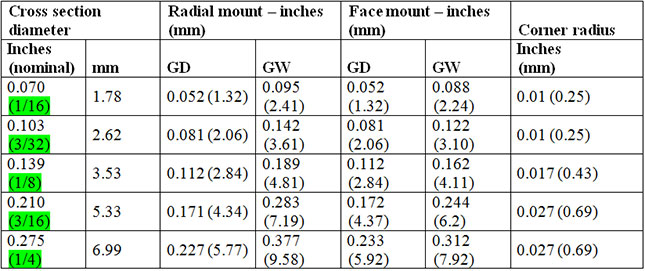