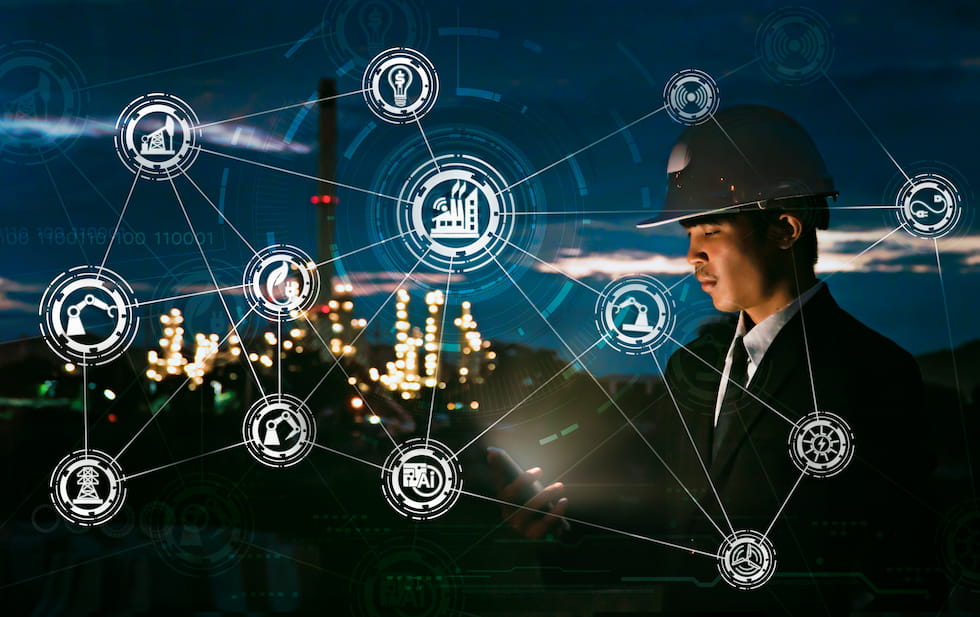
While industrial applications often get a lot of flak for being behind the curve when it comes to technological advancements, it’s interesting to see pump manufacturers leading the way in implementing IoT strategies.
Why is this the case? In many cases, pumps are the most crucial component of an application. The impact of a pump failing is often catastrophic versus, let’s say, a fan or a conveyor. Take a commercial HVAC fan. If the fan fails, there is redundancy to account for the failure. On the other hand, a pump delivering cooling water goes down, and the asset you’re trying to cool overheats, causing devastating failure.
Of course, this is just one example among many critical pump applications, and it’s this criticality that has created a higher incentive amongst pump manufacturers to apply advanced solutions like internet of things (IoT) monitoring. Historically, these types of advancements have been an afterthought where end-users, versus the pump OEM, have implemented add-on condition monitoring tools, like vibration monitoring. Yet, this is changing with more pump manufacturers realizing the value in this “afterthought” and integrating entire IoT-enabled solutions themselves, including drive and vibration monitoring.
Maybe you’re one of those pump OEMs. Maybe you’ve decided it’s time to rethink your IoT strategy to keep up with this shift. We’ve gone through a very similar process in bringing our IoT-enabled motors to market, and here’s what we’ve learned from both a business and technical perspective:
1. Understand the Business Case
The high-level primary objective for any pump end user is to avoid unintentional downtime and ultimately reduce their costs. How can pump manufacturers support that high-level goal? The use of data and analytics is a crucial component. I’m not simply talking about data in a spreadsheet, but the ability to analyze and present data in a way that provides recommendations on what needs to be done. When you elevate your data to analytics with predictive capabilities, you can easily see when vibration, for example, is trending up and receive predictions as to when vibration levels will be outside of the normal operation band.
This leads to the benefit of being able to schedule preventative maintenance and downtime. Normally, when an asset fails, it comes as a surprise and you’re not prepared. When IoT data allows you to see, in advance, that numbers are askew, you can schedule maintenance time and adequately prepare for that maintenance. This also means you can choose when to schedule downtime for the maintenance, selecting a time where you’ll have as little impact on productivity as possible. Ultimately, knowing that error or failure is coming before it comes and preparing for the associated maintenance beforehand not only equates to significantly reduced downtime but increased revenue as well.
This is what all pump OEMS are looking for, right? Increased revenues and profitability. Over the last 20 years, a large portion of the world has shifted to an as-a-service model where the end user is not responsible for ownership, upkeep, maintenance, etc. and is simply purchasing output. Take the copy machine example. In the past, your business likely had their own machine, but today you may simply be paying a service for each copy. And there are the many “anything as a service” (XaaS) models (SaaS, PaaS, IaaS, etc.) that have exploded in information technology (IT) over the last several years.
While the industrial space has been slower to adopt these types of modern business models, we’re starting to see some permeation, and what better place to start than with an application as critical as pumps. No one has more expertise on the pump than the pump OEM that designed and manufactured the product. The option to outsource and leverage their OEM’s help and built-in IoT technology, versus a general maintenance resource, is an appealing option for end-users and a lucrative option for pump OEMs.
2. Consider a Cost-Benefit Analysis of Different Connectivity Options
When it comes to understanding and making connectivity decisions to support your IoT strategy, there are several factors to consider.
We know that, traditionally, everything in a facility was hardwired and on its own guarded network. This works well when anyone who needs data is on the premises or in the same building as an asset, but there are many instances where this set up just isn’t feasible, thus the proliferation of wireless. If you’re a food manufacturer with a waste treatment pumping station far away from main production, running an ethernet cable from your production site to the pumping station is likely not possible.
But you can’t just “go wireless” and move on. There are a variety of options to assess with pros and cons to each: point-to-point, WiFi and now cellular (3G, 4G and 5G). If you haven’t considered cellular as an option, the cost-benefits analysis makes it a worthy contender.
The cost of cellular-based networking components continues to decrease, which drives down the cost of integrating IoT capabilities into industrial applications. Take cars as an example. Many cars are now integrated with cellular modems. With 4G and the approaching 5G release, access via cellular is now so fast, easy and affordable that it’s also driving down the cost of utilizing the same technology in assets like cars. There’s no reason this can’t also be the case for IoT-enabled pumps as well.
On top of the cost benefits analysis, there’s ease of use to consider. Connecting to an existing WiFi network requires end-users to make numerous configuration changes to their devices and their network to allow for data to be sent outside the facility. Choosing cellular for your IoT initiatives avoids all of this entirely.
3. Ask Important Questions Before Choosing a Cloud Platform
When embarking on an IoT journey, you’re likely weighing different cloud options to help you deliver new IoT capabilities or services. Here are the main questions to consider in your search:
How is technology advancing?
The industrial industry continues to see more consolidation, and this consolidation eliminates the need for costly “extras.” For instance, when a pump, motor and drive are integrated, it makes it a lot easier for pump manufacturers to offer IoT capabilities. The consolidation allows for data to be pulled from all sources and integrated into one holistic view. Therefore, you’ll want your cloud solution to be capable of handling data in this kind of multi-source environment.
What’s the business strategy and do you have the resources?
You’ll need to clearly define your IoT goals before selecting a cloud platform, and decide what, if anything, you’re capable of handling in-house. What are your capabilities as a company? If you’re hyper focused on adopting a cloud and IoT strategy as a competitive advantage, you may want to consider more open platforms. These platforms allow for a more custom-built solution catered to exactly what you want your IoT infrastructure to look like, though it would require a built-from-the-ground-up approach from your IT team.
On the flip side, there are some great tools on the market that are purpose-built for the industrial IoT space that take on a lot of the foundational work for you. These tools are designed with industrial applications in mind and include a built-in ecosystem capable of easy additions like cybersecurity monitoring and vibration monitoring analytics. It’s a simple module that makes entering the IoT world easier than most.
There are also plenty of cloud options with built-in IoT capabilities, but these could lack industrial focus. Think about your objectives, your timeframe and what you’re willing to invest before choosing your platform strategy.
Does the platform allow for multiple access levels?
We live in a world where OEMs sell to other OEMs who sometimes sell to other channels before a final product makes its way to the end-user. How much is your cloud platform or IoT strategy really worth if only a small percentage of the people in this chain have access to important data? You want to make sure your cloud platform can enable not only your end-user, but the intermediary channels to market as well. This means you’ll want to choose a cloud tool that allows for multiple access levels and the management of assets across a wide range of people in a way that still maintains each individual and company’s privacy.
How open-ended do you want the platform to be?
The more beneficial your IoT strategy is to your customers, the higher the demand will be for your product. For an end user, your pump is likely a small cog within a bigger wheel. Sure, pump data alone is beneficial, but what your customers really want is the data your asset is providing within the context of the bigger picture, such as the overall health of a cooling tower. They want to have the ability to merge the pump IoT data you’re offering with their systems to uncover their own analysis, predictions and insights. This means that it’s important to find a cloud platform open-ended enough to allow relevant parties to benefit from and build upon what you’re offering.
It’s exciting to see digital transformation making its way to the industrial space and the innovative solutions being applied to the pump industry. It won’t be long before smart-pumps are the norm, leading the way for other industrial assets to follow suite. The advantages of IoT data are immense, and just like the internet and smart phones, it won’t be long before businesses consider it a necessity. Get ahead by exploring IoT for your pumps now, and establish yourself as a leader in what will soon be a crowded space.