Adapt people and processes before implementing IIoT tools
Fluke Accelix
03/29/2019
The industrial internet of things (IIoT) connects data, teams and systems, providing significant opportunities for improving facility operations. One of those improvements includes the adoption of condition-based maintenance (CBM) using advanced monitoring technologies and tools.
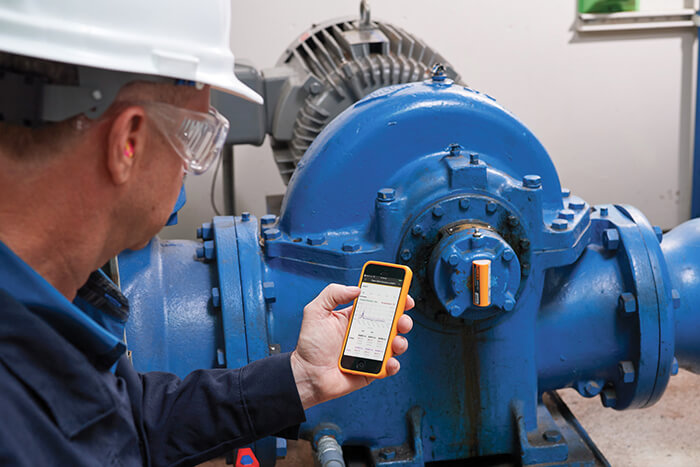

Where, What, Why & How
1. Are you honestly assessing your current PM status? Make no mistake, being on a journey and not knowing the basics of why you are on it can take you down a road to nowhere. Before end users do anything, they need to understand where the facility and its people stand on the path to CBM. First, define the facility’s maintenance and reliability status and confirm that the fundamentals are solid. Do technicians grasp, and can they apply basic RCM knowledge, or do they need further training? Are process and PM routines effective and efficient, or do they need to be revamped? Second, M&R teams should examine in detail what they are doing, why they are doing it, and how they are doing it. Figuring out where the teams are in the journey helps customize a CBM program specific to the facility.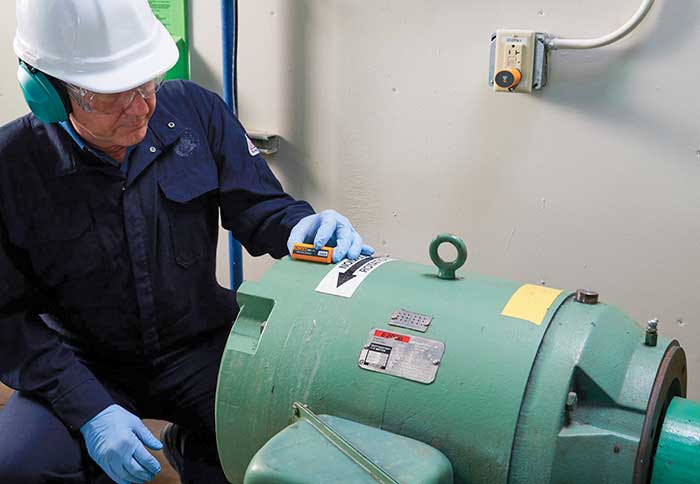
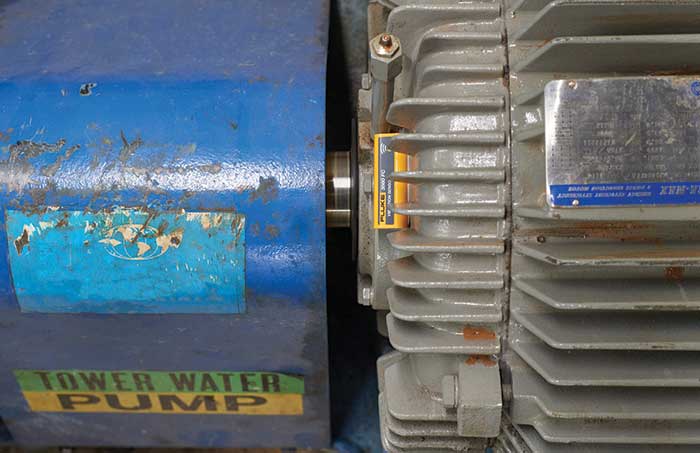