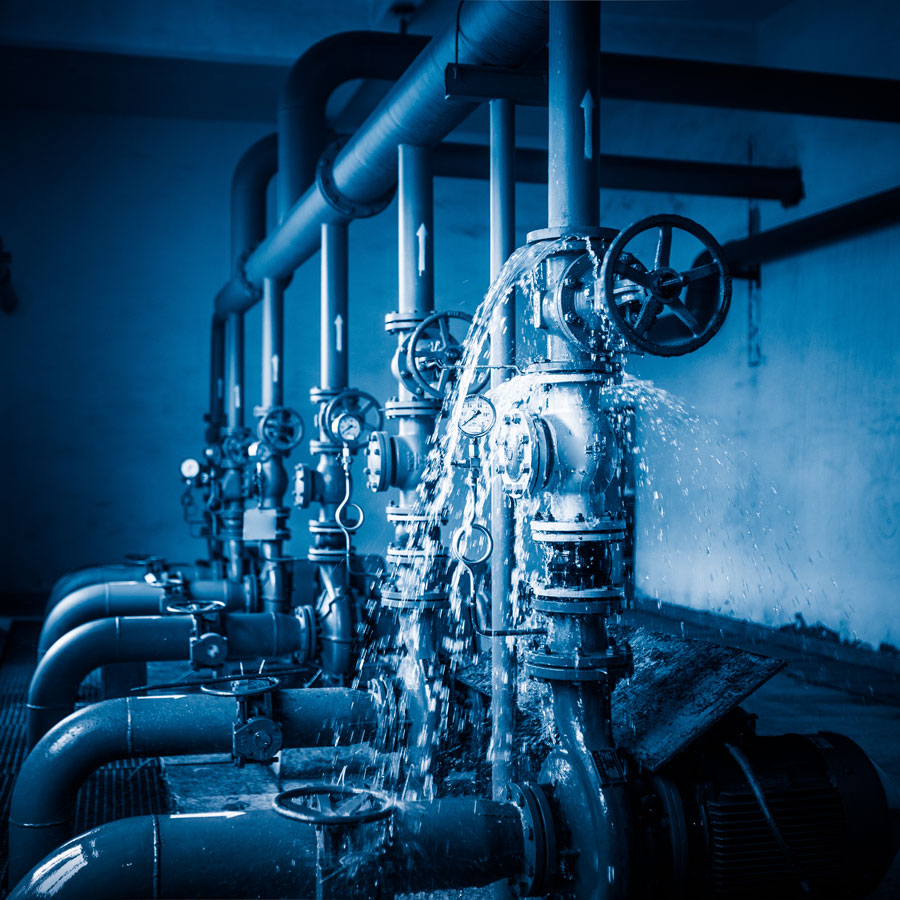
Pumps are a key part of enabling most facilities to properly function and produce their intended product at the expected system reliability. Grand View Research shows the 2020 global industrial market share as divided into five large segments: water and wastewater, construction, chemicals, oil and gas, and power. Globally, there is ongoing growth in the need for chemical products from manufacturing, automotive and construction. Along with continued population growth, there is more demand for power/energy, driving greater usage of various pumps in industry and municipalities to keep up.
At the plant level, users need to maintain pumps with efficient and effective preventative maintenance (PM) to attain or maintain a competitive advantage. Many possible issues need to be checked. Just a few are: excessive vibration/noise, insecure mounting points, bearing temperature, leaky gaskets and pump flanges, over or under lubrication and loose electrical connections.
Most pump failure starts long before it is detected due to corrosion, cavitation, wear, etc. Human error is still a key issue—likely the largest issue. That is due to a lack of training in precision maintenance, insufficient resources, improper maintenance frequencies and insufficient use of predictive technologies and condition-based monitoring.
In North America, top-quartile companies are at 9% reactive maintenance versus 64% for bottom-quartile companies. Maintenance cost as a percent of replacement asset value (RAV) is 2.1% for top quartile and 13.3% for bottom quartile. The Society for Maintenance and Reliability Professionals (SMRP) Body of Knowledge defines RAV as the dollar value that would be required to replace the production capability of the present assets in the plant. It includes production/process equipment as well as utilities, facilities and related assets. It also includes the replacement value of buildings and grounds if these assets are included in maintenance expenditures. It does not include the insured value or depreciated value of the assets, nor does it include the value of real estate, only improvements.
Based on benchmarking results, this means that, on average, it is about six times more expensive to run the business of maintenance (bottom versus top quartile). This does not include the bigger associated losses in production and lost opportunity improvements in safety, energy savings and product quality (as assets get more stable and predictable).
Many companies are still struggling in their journey to a proactive maintenance mindset because it is a complex change process. Some are working on getting better at maintenance. Instead, they should be focusing more on why they need to do maintenance at all and take a reliability-based approach. Users cannot maintain their way beyond the inherent reliability of the asset. Others are working on reliability-centered maintenance (RCM), which considers a user’s limited resources/business situation in making decisions.
To be successful, a big part of the change effort needs to focus on the people side of the effort. Over 70% of companies still pinpoint culture as the biggest roadblock to RCM implementation. In the 1980s, it was not unusual to have a mean time between failures (MTBF) of less than one year. Today, if the correct pump is purchased for the intended application—to operate at best efficiency point (BEP) or American National Standards Institute (ANSI) or American Petroleum Institute (API) standards—it is used as intended and the needed checks are performed, it is not unusual to get an MTBF of over 10 years.
5 Common Pump Reliability Mistakes
Packing vs. mechanical seal
A common myth is that packing is cheaper and more forgiving than mechanical seals. Often, the only cost considered for this comparison is replacement cost. When the costs of packing are factored in, including the frequent (almost daily) adjustments needed, excessive flush water consumption, damage to shafts, base corrosion, etc., mechanical seals can be less expensive. Some states will give rebates based on reduced water consumption.
Maintain seal flush system correctly
The most common cause of seal and packing failure is improper maintenance of the seal flush system. The flow needs to be checked and adjusted frequently as the pump’s performance envelope changes. The correct flush plan for the application should be used and the flush medium should be clean. If seal flush is lost, the packing will be immediately affected. Mechanical seals, dependent on application, can survive for several hours.
Double pumping
Most pump systems with two pumps are designed to be operated with a single-duty pump and a standby pump. The piping systems are designed for the flow from a single pump running close to BEP. Running two pumps in parallel into a system designed for the flow from one pump results in both pumps running far back on their curves, resulting in poor reliability from a variety of flow-related problems.
Specifying pumps
When purchasing/specifying pumps, users often buy the same size pump as the one that is being replaced or decide based on efficiency, believing these relate to quality. Replacing a pump is an opportunity to review the actual requirements (flow head, piping system, etc.) and ensure that the new pump matches the system conditions. A common tendency is to end up with too much pump for the application, resulting in a pump running back on its curve.
Troubleshooting pumps
In a centrifugal pump, the piping system controls the pump performance. Therefore, when troubleshooting pumps, look to the system and piping for the source of trouble before investigating.
5 Best Practices for Pumps
Suction piping
There should be at least 10 diameters of pipe between the suction of the pump and the first elbow. This is especially critical in double-ended pump designs as the turbulent inlet flow can cause shaft thrusting and subsequent bearing problems. If an elbow must be installed, be sure it is in a plane at right angles to the pump shaft to prevent an uneven flow to both sides of a double suction impeller. Make sure eccentric reducers are not installed upside down at the pump suction. The top of the reducer should go straight into the suction flange.
Piping installation
Pipe from the pump suction flange to the pipe rack, not the other way around. This reduces the chance of pipe strain.
Pump selection
For a system that will have variable flow, make sure the system curve and the pump curve intersect each other at a large angle. Having the pump and system curve intersect at an acute angle will result in an unstable system with flow control issues.
Pump assembly
Ensure the pump rebuild is fully documented, including all bearing fits, shaft runouts and clearances. Make sure that the appropriate oil level (centerline of lowest ball) is marked on the outside of the housing for easy validation of oil levels.
Pump housing seals
Always use a good quality labyrinth or an end face bearing housing seal and a good quality desiccant breather to prevent and control moisture ingress.