Product waste in hygienic manufacturing industries such as food and beverage, pharmaceuticals and cosmetics has long been accepted as an unavoidable cost of doing business. The problem is that flushing or draining raw ingredients or intermediate/finished products that remain in suction and discharge piping at the end of production or during product changeovers is the same as watching money go down the drain. The key to eliminating this waste is identifying and deploying the most efficient and reliable pumping technology that can strip suction and discharge lines of still useable raw materials and saleable end products. Technologies such as lobe, external circumferential piston (ECP), twin screw, centrifugal, hose and progressive cavity-style pumps have routinely been used in hygienic manufacturing. Another choice is the eccentric disc pump. The pump’s operating principle—a disc revolving on an eccentric plane within a circular channel—gives it the ability to function in a nonpulsing, low-slip manner with high volumetric consistency. Eccentric disc pumps are also able to pump air, which creates a vacuum effect on the suction side and a compressor effect on the discharge side, resulting in the ability to push a complete product “plug” out of the piping without the need for expensive pigging systems or other line-clearing solutions. Here are several examples where eccentric disc pumps have been introduced to hygienic-manufacturing operations with good results:
1. Winemaking
Bailly Lapierre in Saint-Bris-le-Vineux, France, produces Crémant de Bourgogne, a white or rose sparkling wine made mostly from pinot noir and chardonnay grapes. When the facility was upgraded, eccentric disc pumps were chosen for several stages that require high, nonpulsing flow rates with strong volumetric consistency and minimal slip.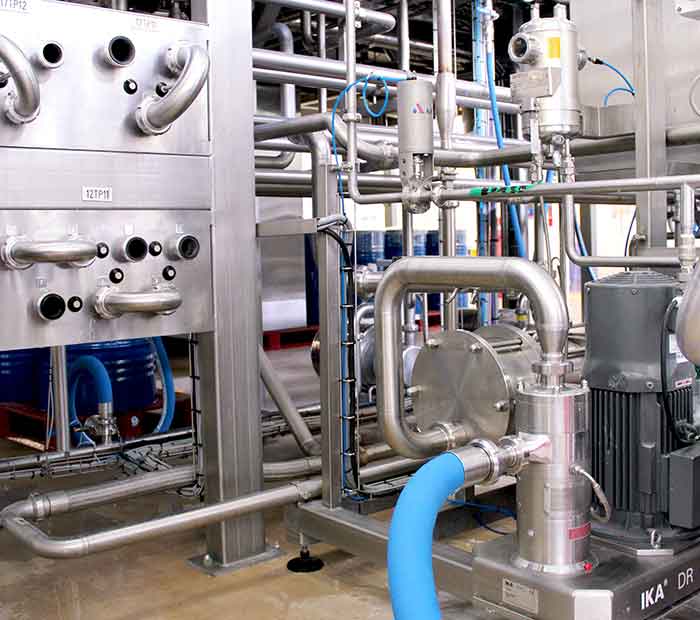