There are not many among us who have not experienced an unintentional bleach-related laundry room mishap. You know, the time liquid bleach was mistakenly added to the wash cycle and your blue jeans came out of the washer dotted with white splotches. But considering how dangerous sodium hypochlorite—the chemical compound that is dissolved in water to create liquid bleach—can be, a couple of pieces of ruined clothing is a small price when compared to the hazards that can occur when sodium hypochlorite is mishandled. Stanford University’s SLAC National Accelerator Laboratory spells out the dangers associated with the handling of sodium hypochlorite and things to be aware of in its Sodium Hypochlorite Safe Handling Guide: “Incompatible with strong acids, amines, ammonia, ammonium salts, reducing agents, metals, aziridine, methanol, formic acid, phenylacetonitrile. When combined with an acid or ammonia may produce chlorine and chloramine gas. [. . .] Contact with metals may evolve flammable hydrogen gas. Containers may explode when heated. Releases chlorine gas when heated above 35 C (95 F). Anhydrous sodium hypochlorite is very explosive. Hypochlorites react with urea to form nitrogen trichloride, which explodes.” Sodium hypochlorite has a pronounced irritant effect and may cause severe burns to the skin and eyes. Any chlorine gas that is created is corrosive to respiratory passages, and sodium hypochlorite is poisonous if ingested. The handling of sodium hypochlorite and the manufacture and use of its components come with inherent risks, all of which must be taken seriously in order to prevent spills, releases or contact that can harm the user or environment.
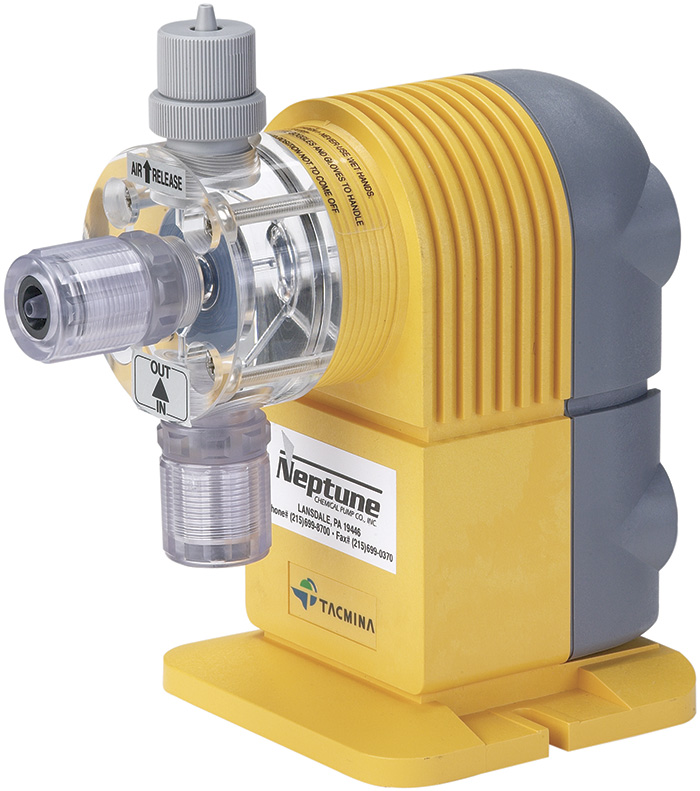