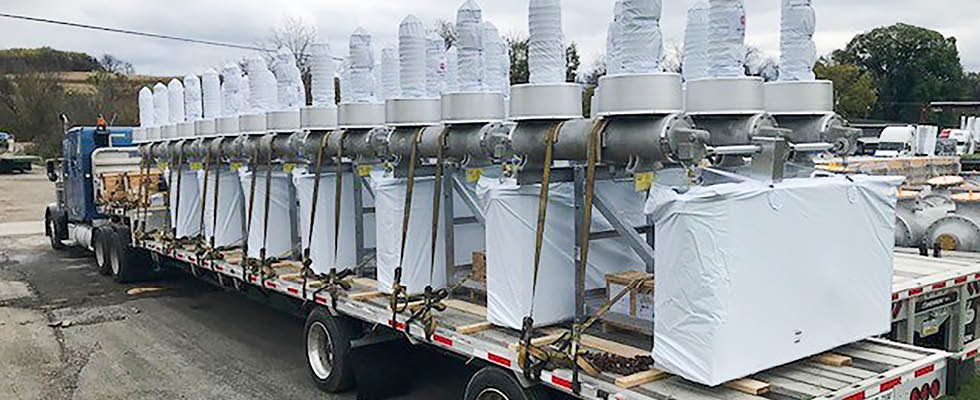
Corrosion is a widespread concern that extends far beyond maritime settings, significantly affecting the longevity and efficiency of power generation equipment. The financial implications of corrosion are substantial, warranting innovative approaches to mitigate its effects. In this context, anti-corrosion protective covers are gaining attention as an effective preventative measure for both manufacturers and operators.
This article aims to examine their function and utility in preserving the integrity of critical power generation infrastructure and will also discuss how to choose the best cover to meet equipment needs.
The Corrosion Problem in Power Generation
Corrosion is particularly detrimental in power generation facilities where high-value equipment is exposed to extreme conditions including high temperatures, pressures and potential chemical exposures. This environment can accelerate the corrosion of metal surfaces, which in turn can lead to increased maintenance costs, reduced operational efficiency and shorter equipment life span.
Power generation assets transported over the road face a similar set of conditions, only amplified. The early onset of corrosion during high-speed transportation can be ignited by an array of factors: the impact of rocks and road debris, moisture damage caused by rain and snow, ultra-violet (UV) exposure, salt solutions sprayed onto roads to prevent ice and more. Especially for equipment manufacturers, keeping newly manufactured assets corrosion free during transit is paramount to preventing warranty claims, and to upholding a reputation for quality.
Initial Considerations
When considering strategies on how to safeguard equipment from corrosion and selecting a protective cover, several factors come into play:
Nature of protection required
The specific threats equipment is exposed to largely dictate the type of protection needed. For equipment stored indoors and shielded primarily from dust and routine environmental factors, a basic dust cover might suffice. On the other hand, equipment intended for over-the-road transportation confronts a spectrum of challenges, from ensuring a proper aerodynamic fit to road debris and UV exposure.
Geography and seasonality
The journey of the asset, coupled with its operational environment and the time of year, plays an influential role in the choice of protection. The majority of North America is susceptible to corrosion, especially near coastal regions where salt is heavy in the air, and in southern regions where humidity is more prevalent. Acquainting oneself with the range of conditions the equipment will encounter can inform and refine a protective cover choice.
Frequency of protection
How often the cover will be deployed is another crucial variable. A cover intended solely for shipping will differ from one designed for prolonged outdoor storage across varied seasons. Similarly, a cover for daily on/off use will have its own requirements.
Pillars of an Anti-Corrosion Protective Cover
An effective protective cover serves multiple functions in reducing the likelihood of corrosion, whether it is for transportation, long-term storage or daily on/off use. The features an effective anti-corrosion protective cover should possess can be categorized into these areas:
UV shielding
Solar radiation can exacerbate the corrosion process, particularly on painted or coated surfaces. While paint and other coatings serve as initial barriers against environmental factors, they can degrade over time due to UV exposure, resulting in exposed bare metal that is susceptible to corrosion.
Moisture regulation
One of the most critical factors that catalyzes corrosion is the presence of moisture, especially when combined with other contaminants like salts and dirt. Protective covers can help in preventing moisture intrusion and reducing humidity levels around the equipment, thus slowing down the electrochemical reactions that contribute to corrosion.
Customized, secure fit
A cover with a tight, secure fit can prevent a multitude of factors that contribute to corrosion. When a cover is too loose and ill-fitting, the chances of dust, dirt, moisture and rodent intrusion rise substantially. In addition, loose-fitting covers present opportunities for wind tunnelling during transit and storage, which can lead to the cover blowing off, completely exposing the asset.
Nonabrasive interior
Covers with coarse and abrasive interior linings can cause the painted or coated surfaces of assets to be etched and scratched, degrading the surface and speeding up the chance of corrosion when exposed to environmental factors like UV and moisture. Ideally, the cover’s interior should be nonabrasive, designed to safeguard even Class A automotive finishes.
Incorporation of vapor corrosion inhibitors
Chemical inhibitors can add a layer of protection by bonding with metal surfaces to deter corrosion. These inhibitors, often incorporated into the fabric of protective covers, serve as a molecular barrier that repels moisture and other potential corrosive elements.
How Modern Protective Covers Differ
Unlike traditional canvas, vinyl covers and ordinary shrink wrap, modern protective covers are designed to address all five aspects of corrosion prevention. They offer the advantage of being water-resistant yet breathable, which allows for effective moisture regulation.
Their material composition includes UV-resistant properties, minimizes moisture retention (enabling better environmental control around the protected equipment) and offers nonabrasive interiors that prevent etching and scratching. Typically, these covers are custom-fit, engineered using modern patterning techniques such as 3D scanning, to guarantee a secure fit and a neat, tailored appearance.
Implications for Equipment Manufacturers
Understanding and employing protective covers can be instrumental for equipment manufacturers keen on improving the durability and appearance of their products upon delivery. A focus on long-term corrosion resistance can result in fewer warranty claims and increased trust in the product’s quality.
Operational Benefits & Cost-Efficiency
For power plant operators, reduced equipment downtime and lower maintenance costs are significant benefits of effective corrosion management. The consistent use of protective covers can contribute to a lower total cost of ownership and more stable operational performance.
Corrosion remains a persistent challenge for the power generation sector, but the use of advanced anti-corrosion protective covers offers a viable preventative strategy. As the industry continues to prioritize operational efficiency and sustainability, these covers provide a tool for preserving critical infrastructure.