A mechanical seal is used to contain a fluid within a pump where a rotating shaft passes through the housing. Many are used in a wide variety of applications all over the world. Technical papers have been written about the various and sundry technologies and applications. But leaks continue to be the bane of anyone who needs to move fluid in their operations. Regardless of manufacturer, size and material of construction, the fundamental basics of the seal function remain constant. The heart of a seal is a combination of highly polished faces, one rotating and one stationary, that run in close semi-contact to each other. Damage to these faces causes seal leakage. Other leaks are caused by running dry, inadequate lubrication, misapplied equipment, operational issues and personnel issues. There are typically one or two of those “bad actors” where conventional sealing technology simply does not work well, where the seal-life expectancy is low and the cost for maintenance is high.
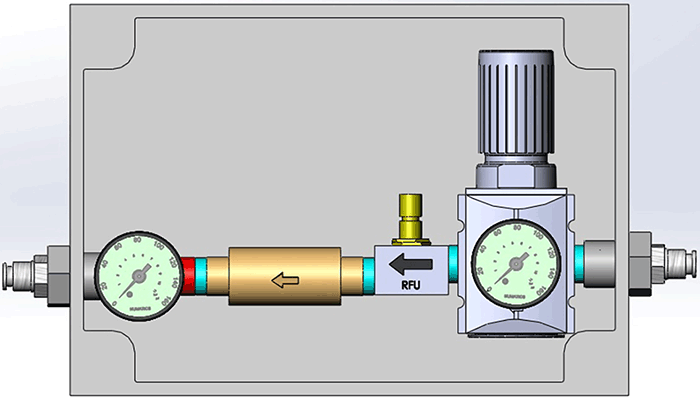
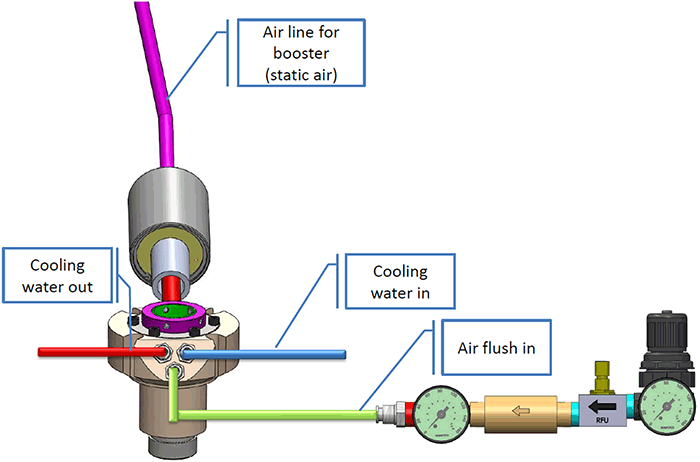
LPS Air Flush for Pump Applications
The air flush feature uses a small amount of compressed air—about 0.17 standard cubic feet per minute (scfm) at 8 pounds per square inch gauge (psig) for a 2-inch pump shaft—or nitrogen, which is injected into the seal to form an air bubble between the back of the seal (bottom of seal chamber) and the back side of the impeller. The air injection pressure is typically one bar—14.7 pounds per square inch (psi)—above seal chamber pressure. In some cases of high solids, a higher margin may be required due to the weight of the process fluid. The process fluid cannot get past the air bubble to leak to the atmosphere. The pressurized flexible sealant maintains the air bubble but also acts as a constant available backup if the pump is shut down or the air is turned off. In essence, the complete LPS arrangement acts to maintain the air flush at the required pressure with minimum air consumption. When the air bubble is generated within the seal, there is a complete phase separation between the seal and process fluid. There is no contact between the process and the sealing components. By this, the seal is constantly sealing so it can withstand dry-run, closed suction and other upsets that would damage conventional mechanical seals permanently. The sealant will maintain seal ability for a short period if air is lost, or in some instances deadheading overcomes the air flush pressure. In some isolated cases, a leak can occur, but unlike a conventional mechanical seal, especially a double, permanent damage does not occur as it would with a conventional mechanical seal. With the LPS system, the seal can be corrected while the pump is in operation and returned to full operation. With a conventional seal, the pump normally would be shut down, pulled and the seal replaced, thus incurring the costs of an unplanned shutdown.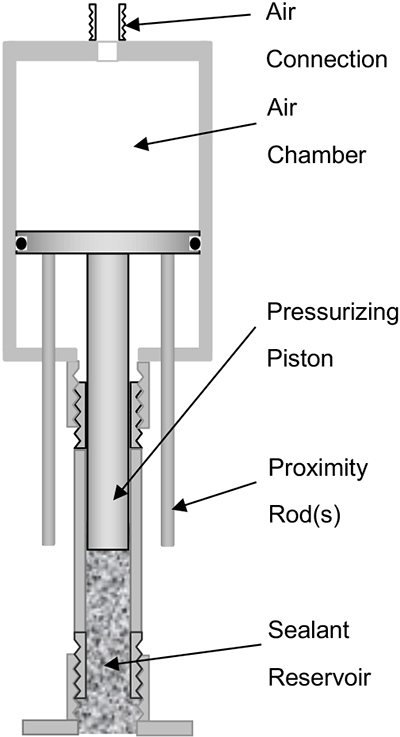
Air Prevention System
The entire air system for the LPS seal is maintained through an air control panel supplied with each seal. It would be similar in function as a barrier fluid support system for an API Plan 53 and double seal but using 100 percent air versus a barrier fluid and air pressure. It would be more similar to an API Plan 74 found on double gas seals. Each panel has a pressure regulator and needle valve that allows the user to adjust the required pressure and flow rate for the specific characteristics of the application. The booster does not consume air, only the air flush, which will be set based on box pressure and process fluid conditions.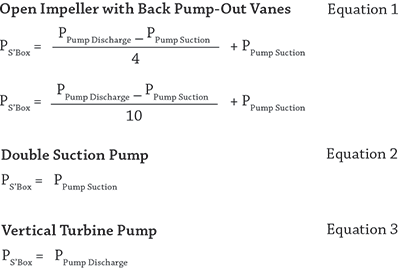