Because of the complicated nature of pump flow and pressure control, industrial plants have often incorporated control of complex pumping and related systems using distributed control systems (DCSs) or expensive specialized controllers. In the past, many programmable logic controllers (PLCs) were not up to the task, so engineers and designers turned to DCSs or similar controllers, which, in some cases, can lead to higher costs and complex implementation. Today, new alternatives allow monitoring and control of these complex systems with programmable automation controllers (PACs), saving considerable expense and simplifying implementation. The PAC, or PLC-based PAC, fills the gap between the DCS and basic PLC. It has the hardware and software required to monitor, control and communicate with these pumping systems (see Figure 1, page 32).
Advanced Process Control
Complex pumping systems often require advanced process control (APC), which goes beyond proportional-integral-derivative (PID) control and can include methods such as model predictive control, inferential control and sequential control. PID is sometimes insufficient because the process that needs to be controlled has a long dead time, is non-linear or presents other difficulties. Various APC control methods and algorithms are supported in DCS platforms but not in most PLCs. PLC-based PACs, on the other hand, can execute many APC algorithms and typically have some built-in APC capability. Some APC methods require complex custom coding, a programming technique supported by DCS platforms but not by most PLCs. The PLC-based PAC solves this problem because it allows users to create custom code, encapsulate it and integrate it into the overall controller program. When APC is required, a PLC-based PAC provides many of the capabilities of a DCS but at a lower cost and with simpler implementation. Pushing a basic PLC to perform APC is impossible in some cases, and even high-end PLCs can require an extraordinary amount of effort to implement APC.Interfacing to Instruments
Pumping systems for applications such as custody transfer often contain a large number of instruments and analyzers. Typical instrument types include flow, pressure, temperature and density. Many of these instruments are multivariable, measuring several parameters at once. Modern pumping systems often employ smart instruments with a built-in, two-way digital data link, rather than simple instruments with a 4- to 20-milliamps (mA) output proportional to the measured variable. For example, custody transfer applications often use mass flow meters because they can precisely measure the amount of liquids transferred from one owner to the next regardless of product density. Coriolis meters measure multiple variables including flow, density and temperature and are most commonly used to measure mass flow. These variables are sent to the control system along with diagnostic, calibration and other information. A typical Coriolis meter used in custody transfer will transmit hundreds of parameters to the control system over a digital data link, presenting data storage and handling challenges. Plants often employ analyzers to measure parameters related to the chemical composition of oil and other liquid hydrocarbons. Like smart instruments, analyzers are usually connected to the control system via a two-way digital data link and often transmit more than a hundred parameters to the control system. Complex pumping systems commonly employ smart valves. Like smart instruments and analyzers, smart valves communicate large amounts of data with the control system over two-way digital data links. A DCS will have built-in communication capabilities for a number of the process control protocols used by smart instruments, smart valves and analyzers. While a PLC will have more limited communications capabilities, a PLC-based PAC will have an extensive array of built-in communication ports and protocols, with the ability to expand through plug-in communication modules.Data Handling
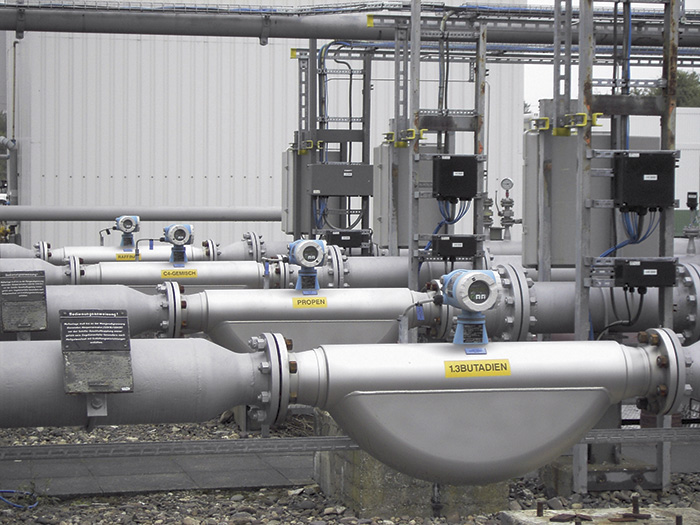
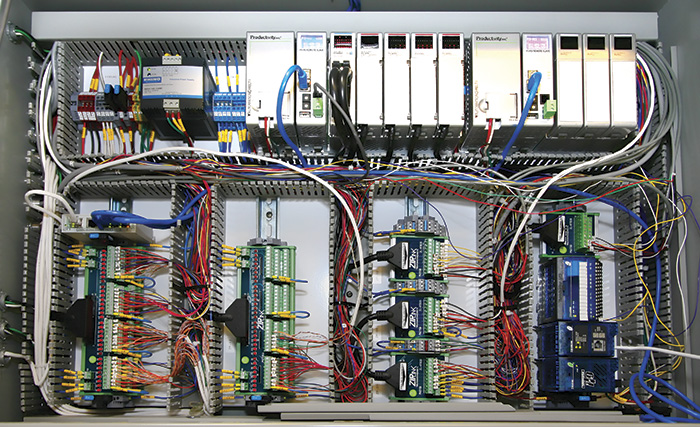
Lots of I/O
Refineries and power plants often have thousands of input/output (I/O) points, many of which are analog and related to the control and monitoring of pumps and related systems. A PLC-based PAC can handle many I/O points, even when the majority of them are analog (see Image 2). The available memory in a PLC-based PAC is more comparable to a DCS than a typical PLC. It will easily support thousands of I/O points and have the program space necessary to handle these more complex applications. Another benefit of a PLC-based PAC is the tag-based control environment, which gives the flexibility to assign data types—and by extension, memory allocation—as needed. Most PLCs have a fixed-memory map, leaving the PLC designer with no flexibility regarding the right balance of memory allocation for the application.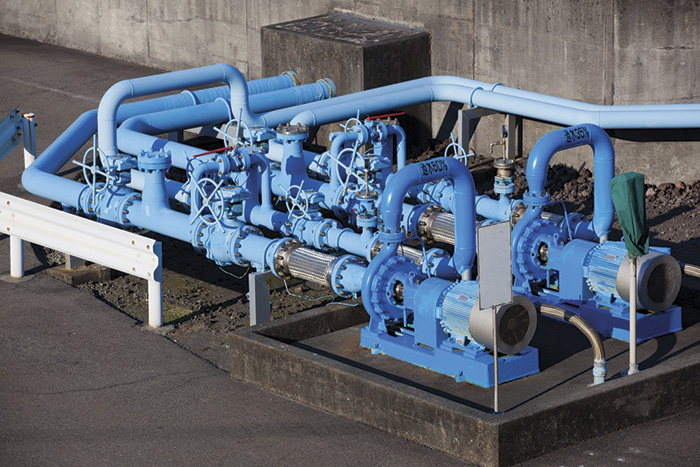
Higher Level Computing System Communication
Control systems for these types of applications often require communication to higher level computing systems. A custody transfer skid, for example, may be controlled by a PLC-based PAC, but it must communicate to a plant-wide DCS. The control system in a refinery or power plant is often tied to an enterprise resource planning system. Getting data to the people who need it has never been an easy task for a PLC, but a PLC-based PAC takes much of the work out of this process. Reporting data to higher level systems often requires interface with Structured Query Language, Access or other Open Database Connectivity database applications. The tag database of the PLC-based PAC is easily shared with bridge applications, allowing manipulation of the database via standard actions such as insert, delete, update or select.Conclusion
A DCS has been the platform of choice for control and monitoring of complex processes, many of which contain large numbers of pumps. While the DCS is quite capable, it can be expensive and difficult to implement. PLCs are less expensive and easier to apply but often are not capable of the task. The PLC-based PAC, however, was created to fill the gap between a DCS and a PLC and can be ideal for these types of applications.Figure 1. PLC-based PAC capabilities for complex control
- APC
- Structure text language for complex functions and calculations
- Sequential function charts for process control
- Integration with smart instruments, smart analyzers and valves
- Can store large amounts of data
- Advanced data handling
- Can handle thousands of analog I/O points
- Easy to integrate with higher level computing systems