After the hangar’s chopper pump in the wastewater sump failed, the maintenance team looked for a reliable, long-term solution.
BJM Corp.
09/29/2016
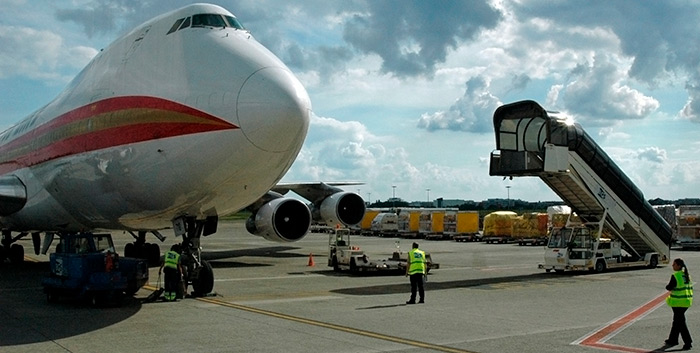
- A pump that could shred solids in the wastewater sewage. The lift station collected raw sewage from the airport hangar. This raw sewage coming out of the planes and from the hangar’s wastewater contained an excessive amount of flushable wipes and rags. The submersible pump would have to shred those solids and operate without clogging.
- Pump reliability. The lift station was designed with a simplex system, meaning only one submersible pump operated in the hangar’s wastewater sump. The team needed a reliable submersible shredder pump to reduce maintenance and avoid downtime.
- Fast delivery. The submersible shredder pump would need to be delivered as soon as possible so the facility maintenance group could install a permanent solution into the hangar’s lift station.