Milk, Chinese hamster ovaries and sewage. What do these materials have in common? They can all be transferred via a pump— and often are. These are just a few of the many duties that are applied by engineers and pump distributors. At a rudimentary level, those engineers and distributors gather basic parameters required for the application and select a pump. That data might include temperature, viscosity, pH, solids size and specific gravity, to name a few. What happens when the pump selected for the application fits the criteria at a rudimentary level, but is not the best selection for the application, and creates issues as a result? The commercial considerations when selecting a pump for an application can be significant. This article will explore a high-level view of a pump selection. It will include diverse applications that are seemingly straightforward but have hidden obstacles and require additional scrutiny to mitigate costly repercussions. The ideas presented here are intended to invoke a thought chain that transcends any particular industry and promotes an effective series of questions to ask when writing a specification, designing a system or replacing a pump in an existing application.
Milk Application
Milk is a nice product to convey. It is not too viscous, has a friendly pH and lubricates mechanical seals nicely. What could go wrong here? One typical milk application is milk receiving, usually at a large dairy provider. Trucks back into receiving bays, hook up to plant piping and pump milk into silos. The trucks need to get in and out quickly.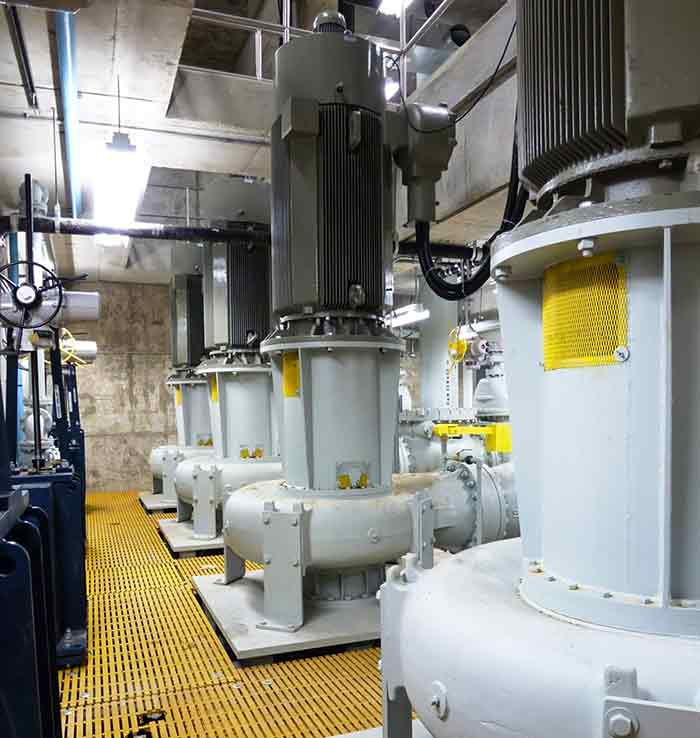
CHO Application
Chinese hamster ovaries (CHO), an epithelial cell line derived from the ovary of the Chinese hamster, are often used in biological and medical research. The first product produced from CHO cells was a product used in the treatment of acute myocardial infarction (heart attack). CHO is extremely shear sensitive and of no value if it is pumped in a manner that compromises its cell structure. The product is useless if subjected to excessive shear. While many pumps can convey this, a successful application requires low speed, shear sensitive design and an inert material composition. An application like this typically requires close collaboration with the end user in terms of compliance, design and shear rates, along with agreement on a successful yield after conveyance. Fortunately there is a body of intellectual capital in the industry that deals with this.Sewage Application
Sewage pumps have always been topical, in that they are large and required to pass many interesting items that range from deflated beach balls to teddy bears. Add a variety of wipes and other items, and things get interesting quickly. Handling solids is not a topic for this article. Neither is the debate between a dry pit pump versus a wet well submersible. They both have merits, and in the spirit of this article, require communication with the end user to determine the best fit. When selecting which one is the best fit, consider some features of the dry pit pump. Dry pit solids handling pumps are installed in dry wells. Their design includes a bearing frame. Lifetime maintenance costs are reduced since bearing life is longer. Servicing the pump is easy because there is a dry space within which to access the installation. When there is a motor problem, maintenance team members can address just the motor. When there is a pump problem, they can address just the pump. Submersible pumps typically have a lower upfront cost, are immersed in the pumped media and are close coupled to the motor. When there is a pump problem, there is a motor problem, and vice versa. Maintenance can be messy since the pump needs to be pulled from the wet well for service. The cost of ownership is typically higher than a dry pit design. Both designs manage large solids effectively. If the end user’s expectations of upfront cost and expected maintenance are resolved, then all base parameters are checked off, and it is a good fit. Seemingly, either pump is a good selection, however, the unknown may be downstream fluid velocities, which could cause settling of solids and blockages. Those issues alone can compromise a seemingly good selection and go beyond the realm of what the pump can handle.Summary
The applications in this article are diverse to make a point. Manufacturers making any product may be experts in their respective field. However, they should be able to rely on the pump distributors and engineers to be the experts when it comes to the pumps used in their process. A high-level view is often required, and the right questions need to be asked. A few major points to consider, beyond basic data:- How important is it to maintain the integrity of the product in the cycle? Is it a premium product where consistency is all important?
- Has the product been tested for shear sensitivity?
- What does the system look like?
- What are the upstream or downstream pipe velocities?
- Are there any space constraints?
- Is the application intermittent or continuous?
- Is flow pacing required or control functions for performance indicators to operators?