Process control through traditional adjustable speed drives (ASDs) with centrifugal pumps has an inherent problem of attempting to use a linear equation to solve a non-linear problem. Common ASD controller software provides an estimated speed to achieve a desired set point. But when the target speed is reached with this method, the set point is not available because the answer is on an unknown non-linear curve. The software must again guess the speed and decrease the error. This process continues until a reasonable deviation from the set point is met. If one aspect of the system curve changes, the whole process must be restarted. Searching for the speed costs energy, even on a single machine. On a system with multiple machines operating either in series or in parallel, a second and more serious problem occurs\'97balancing the load. Even if the machines are built to the same specifications, differences in motor performance, impeller clearances and other mechanical design issues will change a specific pump's speed. Conventional frequency control operates multiple devices at the same speed. In parallel operation, the pump with the greatest pressure capture most of the output and corresponding amperage while the other pumps use a fairly high amount of power and add little to the total output. There is no way to balance a load using frequency directly, because the smallest of physical differences will cause a shift in power to the device with the highest pressure.
Balancing the Set Points
Specialized balancing algorithms start with a fixed linear pump curve number. If the output electrical current is less than the number, the frequency is increased. If the output current is greater than the number, the frequency is decreased. On centrifugal pumps, the frequency in Hertz turns into rpm to meet the amp draw. Amp draw is linear to both pressure and flow, and non-linear to speed. This is in contrast to the balancing algorithm, which directly controls power to meet pressure or flow. Consider the pump affinity laws, where the diameter of the impeller is held constant: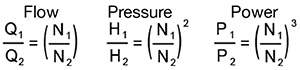
Simplifying Control
If controlled from a common external analog signal, a minimum value of 0 percent will cause all the pumps to run at the minimum set point. The same is true at a value of 100 percent, where pumps will run at their maximums. Each change in set point will affect linear flows and pressures and non-linear frequencies and amp draws.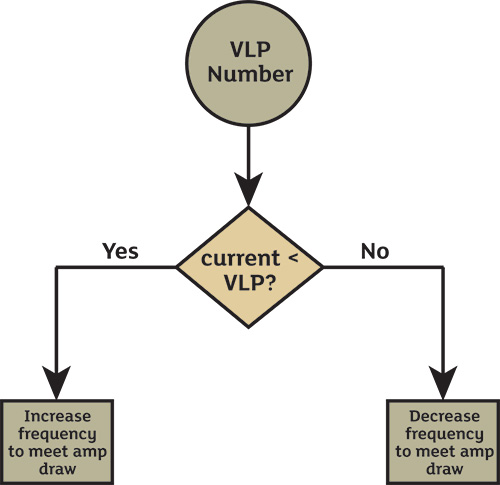