The technology can result in increased productivity, higher safety levels and better overall efficiency.
AMETEK
09/28/2016
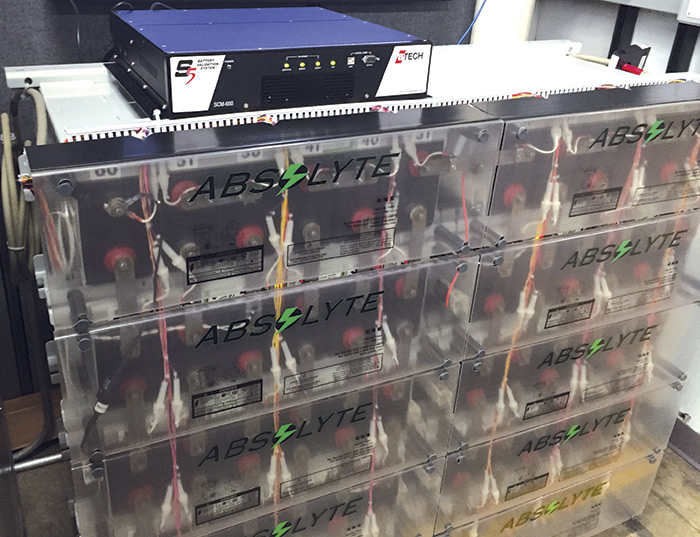
Monitoring vs. Maintenance
Battery monitors can deliver various real-time data down to the cell level, including impedance, temperature, voltage, float and discharge currents. Because impedance deviation is a great predictor of cell deterioration, most monitors today take a baseline cell measurement and compare that to trends over time. If the trend changes beyond an expected level, the monitor will alert the operations center to a cell—or cells—that may be problematic. Compare that type of monitoring to manually checking cell values on a test schedule. First, you have to rely on manual measurements and possible errors resulting from calibration differences. Measurements typically are taken to three places to the right of the decimal point, and battery impedance is a micro-ohm measurement to begin with—incredibly small numbers to track. It is easy to see where errors can be made and how small trends can remain hidden from sight. Monitoring a 60-cell battery bank in real time manually at the resolution and accuracy of a monitoring system would require 60 technicians holding 60 fine-tuned and calibrated meters for only a single value such as voltage—let alone current, impedance and temperature. This is unthinkably inefficient and impractical. A monitoring system, on the other hand, can do all of this and more. Additionally, if there are multiple battery systems at multiple locations, they can be monitored and managed from a central location.Preventive Maintenance
Preventive maintenance programs include some type of human labor. Technicians travel to a location to take readings on a set of batteries. Many times there is some travel involved and tools to be purchased and maintained, not to mention the hourly cost of employee salaries, benefits, safety training, etc. A battery monitor can become the full-time, always-on, always-there maintenance technician for your system. Additionally, periodic visits are just that—periodic. What happens in between visits? Batteries do not fail on a schedule. What happens if the visits are not frequent enough and problems arise in the interim? Monitors increase efficiencies with reduced troubleshooting, often eliminating multiple trips to solve a single problem.Averting Crises
The premise of a battery monitor system is to manage the asset and prevent a catastrophic event. Essentially, the system is like buying an insurance policy for your battery bank and all the direct-current (DC) equipment that depends on its clean, available power. There is an old saying: “Why is there never enough time to do the job right but always enough time to do it over?” Proper planning up front saves money, time and pain down the road. The UPS systems manufacturer experienced a similar situation last year in its manufacturing facility. When installing a battery monitor on a UPS that backed up the IT servers and phone system, alerts were immediately received to six bad cells on a 60-cell system. At first, it was believed to be a calibration problem with the new monitor, but these same cells were checked manually every six months. Further inspection revealed that there were six suspect cells. One of them was more than 100 percent out of voltage tolerance, meaning that the possibility of a thermal runaway condition was only days or hours away. In retrospect, the manufacturing facility was dangerously close to losing its servers and phones and experiencing damage to the other cells in the system. This would have caused a shutdown, resulting in high production losses. Instead of managing a crisis, the company was able to schedule the timely replacement of an aging battery system. By installing the monitor, the need to call a technician service to conduct measurements was eliminated and peace of mind was restored—another added benefit.Asset Management
Industrial batteries are an expensive but valuable and necessary asset in any manufacturing operation or industrial application. Maintaining them on a regular basis is like maintaining the family car: By ignoring the warnings of low oil, tire wear and other problems, the end costs will most certainly be higher; however, by following a scheduled maintenance regimen that is dictated by built-in computer prognostics or a manual checkup, the car will operate at optimal efficiency. The same is true for industrial batteries. They need attention and care. It is typical for a seven-year battery to last less than three if not maintained properly. Batteries need the same type of attention in terms of torque on the terminals, electrolyte levels and checking their electrical health. Battery monitors are designed to provide those services, but they do it faster, more accurately and more efficiently than previous manual methods. For management, the benefits of using battery monitors go beyond the countless dollars saved. They also bring a sense of relief from the frustration of not having an accurate pulse on the condition of the installed batteries. Monitors allow operators to check the health of the cells at any time and view trends as they happen, resulting in increased productivity, higher safety levels, better overall efficiency throughout the facility and a healthier business bottom line.
To read other Efficiency Matters articles, go here.