Some will know from their experience with automobiles that thicker oils, such as Society of Automotive Engineers (SAE) 30, are more appropriate for warm summer months. But thinner oils, perhaps SAE 10, can help prepare a vehicle for winter driving. Figure 1 illustrates where these motor oils fit in comparison to the industrial oil designations used today. Thick oils are more viscous and may not readily flow into the bearings. Users can heat the oil or avoid oil rings and other risk-inducing lube application methods by using smarter means. They can use a jet of oil (oil spray) or convey the oil mixed with compressed air in the form of an oil fog—also called oil mist. Whatever the user chooses, he or she must guard against using the thinnest oil found on the market to avoid the problem of inadequate oil film strength and thickness.
Lube Oils for Process Pumps
The MRC Engineer's Handbook states, "In general, the oil viscosity should be about 100 Saybolt Universal Seconds (SUS) at the operating temperature."1 If for some reason a bearing was operating at 210 degrees F, Figure 1 would call for a lubricant with an International Organization for Standardization (ISO) viscosity grade (VG) somewhere between 220 and 320. But that is unrealistically thick for most process pump bearings. Oil rings, if used, would probably slow down and malfunction in such viscous oils. Oil overheating may be an additional concern.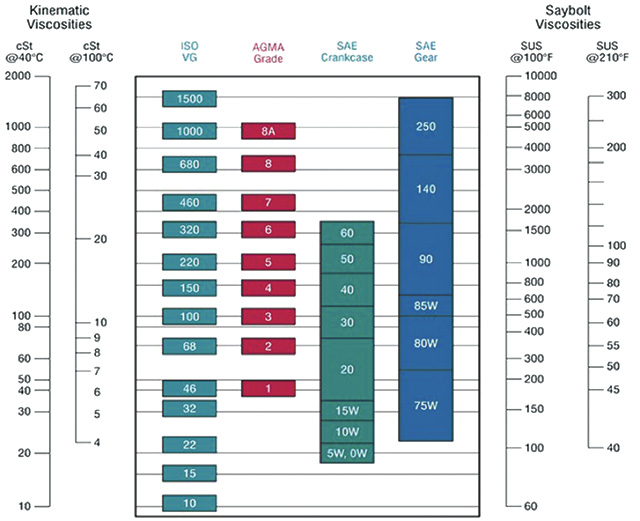
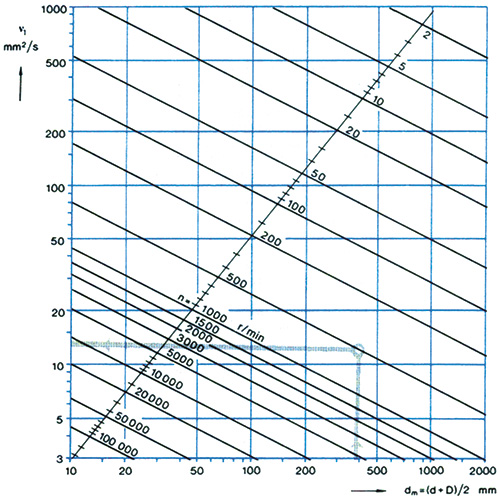
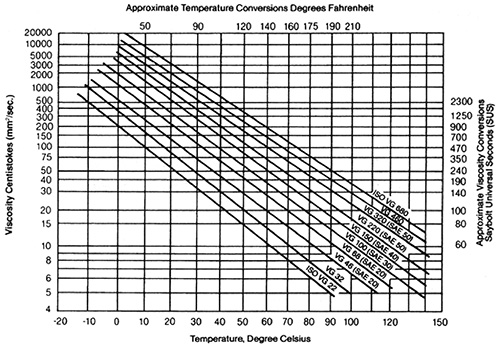
Real-World Example
In a recent case history, ISO VG 100 was applied to a large pump where ISO VG 68 mineral oil or its equivalent ISO VG 32 would have sufficed. An ISO VG 32 synthetic is the bearing life equivalent of an ISO VG 68 mineral oil. The synthetic ISO VG 32 runs considerably cooler than the mineral oil equivalent. With ISO VG 100 mineral oil, the oil-misted radial bearing ran a few degrees in temperature lower than it had with conventional sump and oil ring lube. The user was pleased but expressed disappointment at a triple-row thrust bearing running as hot as before—190 F. A premium formulation synthetic ISO VG 32 would have been sufficient and would have given the user everything a solid reliability professional could have asked for. Reliability professionals would like to see pump bearing housings with no oil rings, no need for constant level lubricators and few, if any, repeat failures. They start with the right lubricant. Why, with all that, is the radial bearing cool? After all, it is also surrounded by the thick ISO VG 100. It is cool because it has no load. The load is in the triple-row thrust bearing, and that creates temperature in addition to the frictional temperature mentioned earlier in this article. Part 2 of this series will examine which temperatures are reasonable, which are high and which are out of allowable range for rolling element bearing housings and pump bearing housings. References- MRC "Engineer's Handbook," General Catalog 60, Copyright TRW, 1982
- Bloch, H.P.; "Improving Machinery Reliability," Gulf Publishing Company, Houston, TX, 1983, 1993
- SKF America, General Catalog, Kulpsville, PA (2000)
- Bloch, H.P. "Pump Wisdom: Problem Solving for Operators and Specialists," John Wiley and Sons, Hoboken, NJ, 2011