In many pump applications, pressure gauges are not used to monitor the equipment and process flow. The operator has no idea if the pump is functioning as designed or as needed for the application. Before long, the pump may become a high-maintenance item. Why do so many pumps operate without proper monitoring?
Why Pumps Need Pressure Gauges
A set of digital pressure gauges will indicate if a pump is healthy or sick. How? The gauges will show the pressure differential between the suction nozzle and the discharge. That differential should match the psi for which the pump was designed, its best efficiency point (BEP).
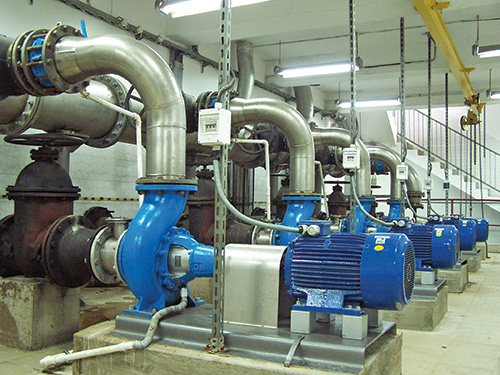
For example, if the pump was designed for 80 feet of head, it should be outputting 34.6 psi (80 feet / 2.31 = 34.6 psi) above the suction pressure. If the digital gauge at the suction nozzle reads zero, then the discharge pressure gauge should read 34.6. If the suction gauge reads 25 psi, the discharge gauge should read 59.6 psi. If the discharge pressure is not right, either the system or the pump needs to be adjusted to run optimally. This will prevent many problems—including cavitation—helping the pumps’ bearings and mechanical seals last for many years. Before end users can make the right changes to their pumps, first they need to understand how well the pump is operating. Good pressure gauges can provide this knowledge.
Where Do The Pressure Gauges Need To Go?
In reality, at least three pressure gauges are required to tell the pump technician the whole story:
- One at the discharge—for the actual output of the pump
- One at the suction nozzle—determines whether the pump performs as designed
- One to determine the gross positive suction head (GPSH)—helps the process engineer ensure that the pump has an ample supply of liquid
GPSH is the total energy at the source of the liquid—whether that is a tank or a pump farther up the line. Subtract influencing factors—such as friction—and factor in the height differences to determine if the net positive suction head (NPSH). The pump requires a certain suction head—net positive suction head required (NPSHr). If the suction head available (NPSHa) is less than what is required, then of the pump system has a problem. Therefore, all three pressure gauges are important to verify that the pump can operate as designed. If it cannot, then the system must be adjusted. Ignoring these issue will result in a high-maintenance pump.
What Are the Consequences of Ignored Pressure Readings?
Several problems can arise with pumps that run outside their BEP, including:
- Decreased efficiency
- Shorter lifespan of the bearings and seals
- Cavitation
Without digital pressure gauges on the pump, money is wasted trying to determine why the pump does not perform as it should. The pump is usually blamed. When it shuts down, it is considered unexplained downtime. Maintenance operators will tear apart the pump and replace its broken parts, scratching their heads the whole time. In short, without pressure gauges on pumps, understanding that the pump’s poor performance is a symptom of the system design—and not the cause of the problem—is difficult. Continual repairs and misdirected efforts can cost thousands. A good digital pressure gauge costs only a few hundred.
What Type Pressure Gauge Should Be Used?
Pressure gauges come in several different pressure types, and end users need to choose the right one. A basic understanding of what the pressure types are and how they affect the measurement of pressure gauges is helpful. The types include:
- Gauge pressure—is vented to the atmosphere. Therefore, a “gauge” pressure gauge measures all pressures relative to atmospheric pressure, which changes with the weather. It also only measures positive pressure.
- Compound pressure—is also vented to atmosphere. It uses atmospheric pressure as its reference point as well. However, a compound pressure gauge measures both vacuum and positive pressure.
- Vacuum pressure—is also vented. It still uses atmospheric pressure as its reference point. However, vacuum pressure gauges measure only vacuum pressure. At sea level, a vacuum is somewhere between zero and -14.7 psi.
- Sealed pressure—is not vented to the atmosphere. Its reference chamber is sealed at the factory, primarily for dusty, dirty or wet environments to protect the internal electronics. Sealed pressure gauges typically measure positive pressure.
- Absolute pressure—is also not vented. Its reference chamber is sealed at the factory as well, but under a full vacuum. Therefore, it considers even vacuum pressures as positive measurements.
Because pumps deal with vacuum pressure, an accurate pressure gauge must also account for vacuum pressure. For this reason, a compound pressure gauge or an absolute pressure gauge should be used.
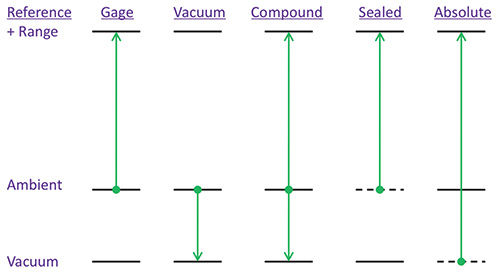
Using an absolute pressure gauge on pumps is a good idea, particularly when an end user needs a sealed chamber for protection from dust and moisture ingress. However, because it is not vented to atmosphere, the readings will change along with atmospheric pressure changes. This happens as the weather changes from day to day—resulting in a change of a few psi. Operators will need to be trained to read the pressure gauge. For example, what was zero on the compound gauge is actually the natural pressure of the atmosphere at the application’s elevation. On an absolute pressure gauge, it would read somewhere close to 15 psi, instead of zero. Operators must also understand why the readings will change when compared to a vented reading that automatically adjusts with the atmosphere.
Digital Is Best
A digital pressure gauge is preferred because it is more accurate and stable. The gauge reading is unaffected by vibration, and a digital gauge will not need calibration as often. In addition, its features, such as multiple units of measure, help end users convert their lingo for the different engineers to whom they will be talking. To make digital pressure gauges more affordable, end users can plumb in a valve at the suction nozzle and discharge of their pumps. This will allow them to use one set of gauges on multiple pumps, so that they can enjoy the enhanced reliability and features of digital gauges without large expenditures. Analog pressure gauges, on the other hand, are less accurate and less reliable. The needle and internal gears are dramatically affected by vibration. If left on a vibrating line for too long, the gauge will quickly wear—requiring either recalibration or replacement. Reading a needle on an analog pressure gauge contributes to inaccuracies. If a good analog gauge has an error band of 5 percent or less, this is magnified by visual error. The user who reads the gauge is guessing at decimal points, and the angle at which it is read will increase the error band. This is compounded when the needle vibrates. Suddenly, the analog gauge that was purchased for a low price with good-enough accuracy is no longer capable of performing within spec.
Make a Sound Investment
When a pump is left unmonitored, it may soon become a high-maintenance piece of equipment. A lot of money may be spent trying to fix the pump when it is not the problem. A good set of digital pressure gauges will prevent unnecessary and expensive maintenance. With proper training, much of which is available online, operators and mechanics can properly troubleshoot and fix pump issues before they result in pump repair and a loss of production.