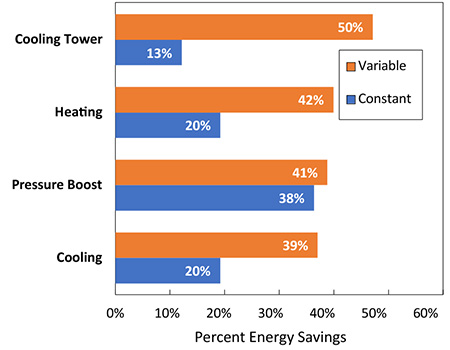
As 2021 arrives and users begin to establish new goals around energy savings, new research on the energy savings potential of smart pumps, or pumps with integrated power drive systems (PDS), shows commercial building operators can reduce energy usage, operating costs and carbon footprints in the months and years ahead.
The report, sponsored by the National Electric Manufacturers Association (NEMA) and the Northwest Energy Efficiency Alliance (NEEA), is one of the first in-depth analyses that supports the benefits of PDS in both variable and constant load applications.
PDS combines a pump, an electric motor, adjustable speed controls and sensors, which allow equipment to slow down or speed up to meet demand and makes the pumps more efficient.
Adding variable speed capability in commercial buildings is not a new idea. But until now, there has not been much data on how much energy savings PDS can unlock in constant load systems. This has likely kept many organizations from investing in a PDS and prevented them from reaping the full benefit of better system control.
Right-Size for Savings
In constant load pumping systems, or systems that require consistent demand throughout operation, motors are often oversized. Oversizing can occur for many reasons, including limitations on the stock sizes of motors manufacturers have available, engineers building in extra system robustness, or because field conditions differ from the original design. This oversizing leads to a higher flow rate in operation than required in design.
Historically, installers adjusted pump flow rate though mechanical means such as using a balancing valve to throttle flow or by trimming a pump’s impellers. However, using these methods has consequences. Balancing valves increase energy use, while trimming impellers is expensive, time-consuming and intrusive. Trimming impellers also limits future expansions.
Analyzing data from pumps installed in a variety of applications in the Pacific Northwest (heating and cooling, industrial and manufacturing applications), NEEA and NEMA found that using a PDS instead of conventional measures could result in:
- an average of 23% energy savings in constant load systems
- an average of 43% energy savings in variable load systems
The NEMA and NEEA research also found that the payback period, or the amount of time it takes to recover the cost of investing in a PDS, could be as low as 10 months for a constant load system and four months for a variable load system.
The analysis also explored the difference in savings for constant and variable loads for four commercial pumping applications: cooling towers, heating water, pressure boost and chilled water. The research found that while the savings potential is larger for variable load pumps, every application sees energy savings from PDS installation on constant load pumps.
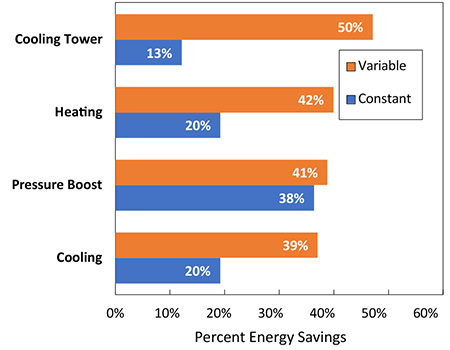
Image 1 shows the savings broken out by application and load type for four of the most common pumping configurations analyzed by the study. These results indicate that even in constant load applications, using a PDS to right-size a pump can result in energy savings of 23%.
Non-Energy Benefits
The analysis also found non-energy benefits of installing a PDS:
- Lower maintenance costs from reduced equipment wear, vibration, heat and load when starting and operating motors and motor-driven equipment
- Process improvements and improved control, which can have meaningful impacts on overall system efficiency (e.g., ensuring appropriate return water temperatures to a condensing boiler) and better response to changes in system load due to unexpected increases or decreases in demand
System connectivity and visibility, allowing operators to remotely maintain efficient equipment and system performance.
According to ENERGY STAR, energy efficiency investments can also pay for themselves by increasing the value of buildings and industrial sites. Studies from the U.S. Department of Energy (DOE) have shown that efficient buildings and industrial plants have lower operating costs and have shown that efficient commercial real estate properties command higher rents with tenants.
Beyond Pumps
While the new NEEA and NEMA study focuses on pumps, the concepts and projections in the report likely apply to fans and centrifugal compressors as well. While the energy savings for a PDS in fan and compressor applications may be different, the non-energy benefits mentioned above are meaningful and should also be considered.
Energy Impact of Commercial, Industrial Sectors
The data presents a clear opportunity for owners and operators of commercial and industrial facilities to cut their energy spending and help reduce the nation’s overall energy use.
The U.S. DOE reports that commercial and industrial buildings, from factories to schools to supermarkets, account for nearly half of all energy consumption in the U.S., at a cost of more than $200 billion per year. That is more than any other sector of the economy. Out of that energy, 30% or more is wasted through inefficiencies.
Considering motor-driven products including pumps use over 25% of all commercial energy, this new research shows the potential for energy savings by using a PDS. Greater use of PDS, along with other efficiency improvements, means organizations can save more energy and more money and have a greater impact on protecting the environment.
Visit NEEA’s resources and reports page (neea.org) to read the full analysis on PDS. There is also other research available on emerging technologies that may help inform energy efficiency projects.