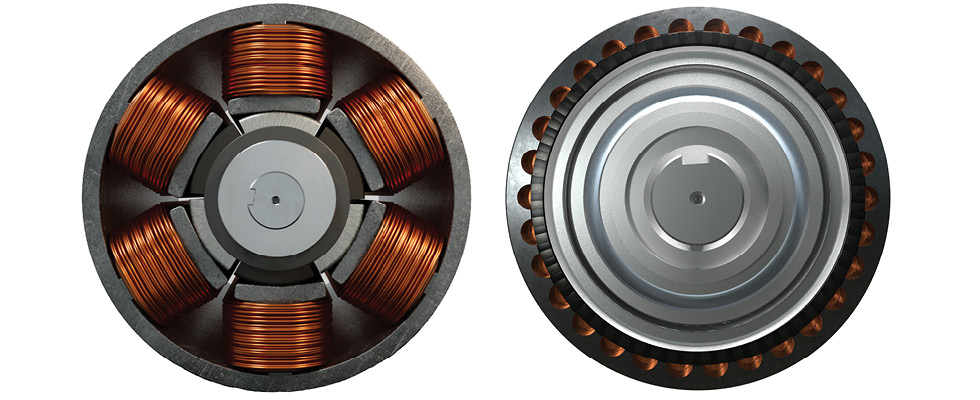
Standard Motor Technologies
The fundamental technology behind electric motors has remained the same for decades. Even with advances such as brushless technology, efficiency improvements to brushless direct current (BLDC) technologies and ever-improving controllers like variable frequency drives (VFDs), they often do not deliver the torque and energy efficiency needed for many applications today.
Transverse Flux Motor Design
A motor technology has recently been introduced and integrated into double diaphragm pumps to provide a high torque, low rotations per minute (rpm) solution to the fluid transfer world. At the heart of this technology is the use of a specially designed transverse flux motor. The design incorporates up to 10 times more motor poles and drastically reduces electrical losses with low-resistance coils. These low-resistance coils consist of an inner ring of simple copper coils that replaces the “rat’s nest” of wiring typically found in a conventional motor. This simple and compact coil set facilitates effective and efficient conversion of electrical current into mechanical torque.
This enables the electric double diaphragm pump to be gearbox-free. Traditional pump technology using an alternating current (AC) or DC motor requires gearboxes and couplings, which can introduce mechanical losses and additional maintenance and require control systems. The integration of the transverse flux motor into the double diaphragm pump technology avoids these drawbacks.
Further improving the efficiency of this design is the encapsulation of the windings within the housing instead of wrapping the coils around a core. This change means far more electromagnetic flux lines are captured and utilized in the creation of the electromotive field within the motor. Coupling this electrical induction with the increased number of poles creates magnetic fields, leading to a consistent and stable overall field. This translates to a continuous torque force that is eight times higher than equivalently sized AC induction motors running at nominal speed.
This torque improvement is even greater as the motors are operated at lower speeds. It provides an excellent solution for applications that require low-cycle rates versus traditional motor technology that works in the 1,800-3,600 rpm range (with significant gear ratio or belt reductions).
Improving the Basics
1. Lighter and more compact in application: By eliminating the need for a gearbox, the size, weight and footprint of the electrically operated component (i.e., pumps, mixers, agitators, etc.) can be reduced considerably, and the overall length of the powertrain can be shortened.
2. Increased operating range: An integrated control and direct drive motor leads to higher torque at far lower rpm, which results in a broader continuous operating range—thus eliminating issues that arise at high and low rpm.
3. Reduced heat generation: At low speeds, the transverse flux motor technology does not have the same heat issues seen with AC motors when being run at lower frequencies using a VFD to control the speed, which leads to longer overall motor life.
4. Improved reliability: With fewer moving parts (no brushes, gears or couplings), reliability is improved, leading to less downtime. Elimination of the fan required to cool AC induction motors further reduces a potential failure mode.
What Does This Mean for Positive Displacement Pump Applications?
Integrating the motor design into positive displacement pumps, such as pneumatic double diaphragm, rotary lobe or peristaltic, provides solutions not currently possible with traditional electric motor technologies. The compact motor fits more closely to the pump housing, creating a lighter and smaller design.
1. Plant automation: With the proper control, transverse flux motors can be operated remotely just as traditional AC motors. Via programmable logic controllers (PLC), supervisory control and data acquisition (SCADA) or over Ethernet. Traditional VFDs are not required to operate transverse flux motors, as frequency does not need to be manipulated to vary motor speed.
2. Energy efficiency: As energy consumption and sustainability initiatives have become high priorities for companies, facilities are forced to look at ways to conserve electricity. Electricity has long been the preferred method of powering pumps (though this is not always ideal, as in the case of pneumatic diaphragm pumps). This is due to electricity being the cleanest and, generally, most efficient way to power pumps. However, even the most efficient electric motors cannot overcome the mechanical losses when coupled with helical or planetary gear trains. Depending on gear train design, mechanical efficiency losses can exceed 25% and climb as high as 40%. Transverse flux motors eliminate these efficiency losses, and they do not require a gear train to achieve low rpm torque.
3. Pump technology: Transverse flux motor technology has also allowed for flexibility in powering pumps that have, traditionally, not utilized electric drives. A notable example is pneumatic diaphragm pumps. Diaphragm pumps have been used for decades due to their suitability for nearly any application. However, with the increased cost of generating compressed air, they are becoming cost prohibitive to operate. Transverse flux motors, with their high torque capability and low cost (relative to induction AC motors and gearboxes) are a solution when operating diaphragm pumps electrically.
4. Safety: Plants are constantly looking for ways to improve environmental safety and health (EHS). As in the example above, plant noise can be reduced by simply converting pneumatic pumps to those utilizing transverse flux electric motors, eliminating the large amount of noise pollution caused by exhausting compressed air. Secondarily, eliminating compressed air can reduce the likelihood of product contamination due to condensation buildup in the exhaust of compressed air driven pumps. This is especially critical in hygienic, pharmaceutical and biopharmaceutical applications.
Transverse Flux & the Future of Industry
Efficiency is front of mind for most plants and the people operating them. Transverse flux motors, by eliminating the gearbox and leveraging a high pole count, deliver significant advancements in electric pump technology. This leads to energy savings and the ability to achieve sustainability goals. The addition of transverse flux technology to pneumatic pumping systems also increases worker safety and product integrity.