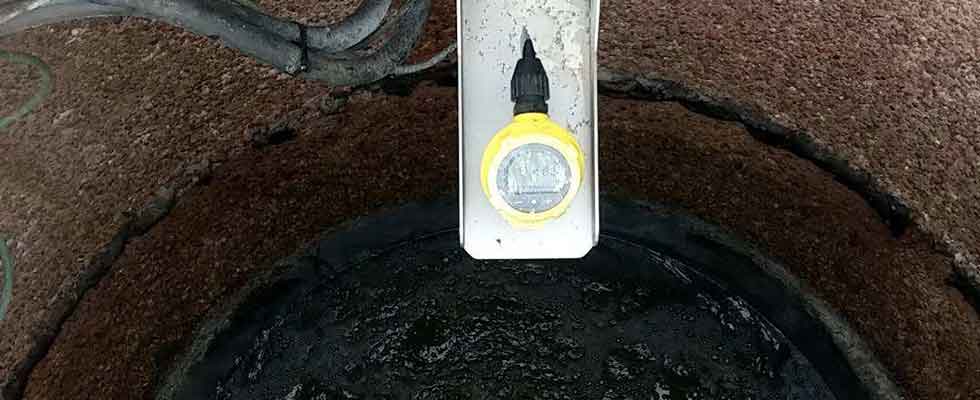
Wastewater collections systems, treatment plants and potable water facilities are experiencing an awakening as new level measurement technology is increasing the safety and simplicity of widely used processes found across the United States. Radar sensor technology is thought to be an accurate and reliable option.
These systems, plants and facilities have traditionally relied on ultrasonic transmitters, bubblers and floats. Each of these technologies were once considered cutting-edge, but the industry continues to build on instrumentation precision. As radar technology becomes more prolific, it also becomes more affordable.
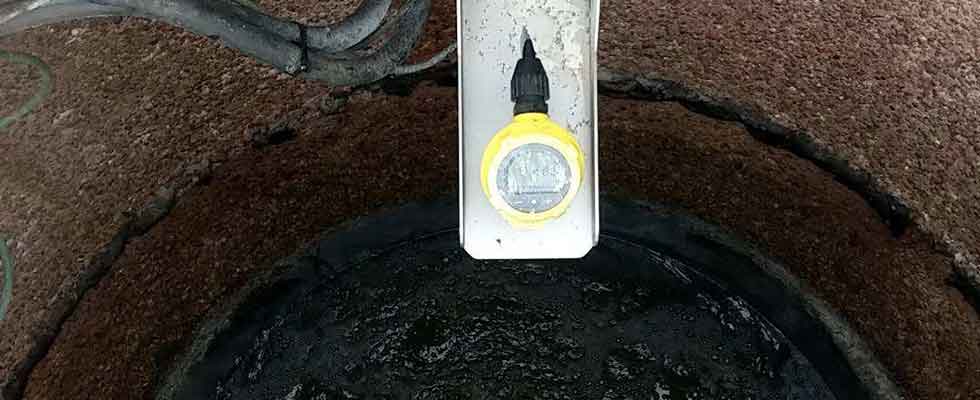
Lift Stations in Louisiana
More than 43,000 people in southern Louisiana rely on 160 lift stations to move wastewater to four treatment plants. These lift stations are scattered across their vast collections system and every lift station uses sensors for level measurement and pump control.
One shallow well was using an ultrasonic transmitter in combination with a submersible pressure sensor. With the setup, pumps were short cycling, running for roughly two seconds per cycle, which caused inefficiencies and put unnecessary wear and tear on the pumps. To remedy the situation, operators tried a new radar sensor, paired with a controller.
This 80-gigahertz (GHz) radar sensor is designed for noncontact continuous level measurement. The radar’s higher frequency means the sensor has a narrower beam angle, allowing it to only measure the surface of the water and avoid other obstructions in the well.
The higher frequency also allows the radar to measure through the light foam often found in lift stations. Specialized electronics inside the housing ensures the radar provides accurate and reliable measurements even when condensation forms on the radar antenna.
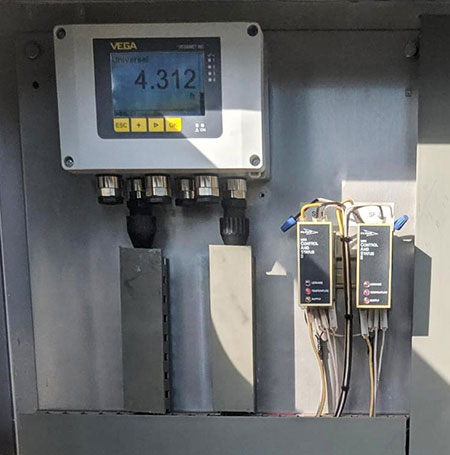
Influent Flow in Illinois
A suburban municipality in Illinois treats wastewater for a population of about 63,000 people. Like all wastewater treatment plants, the facility is required to track and report the influent and effluent flow of water. To do this, the sanitation department uses an ultrasonic transmitter to calculate a level-based flow measurement in a 36-inch Parshall flume.
This measurement is out in the open and susceptible to fluctuating temperatures, condensation and spider webs, all of which can cause measurement errors with some other transmitters. Installing an 80-GHz radar sensor for continuous level measurement bypassed these issues because radar microwaves are immune to changes in temperature, and the narrow radar beam with software can ignore condensation and obstructions that would otherwise impede the signal. Now, operators have a better idea of how much water is entering the plant.

Fluoride Tank in Eagan, Minnesota
Municipalities across the U.S. and around the world add fluoride to drinking water to reduce tooth decay in residents. Just outside of Minneapolis, a small city keeps a day’s supply of fluoride in a single 150-gallon polypropylene tank. Installed on top of the tank, an ultrasonic transmitter measures the level to monitor inventory and ensure a steady supply of fluoride.
However, operators were unable to maximize use of the fluoride day tank. The installed transmitter had a near zone, or “dead band,” spanning 12 inches directly below it, so the tank could not be filled to the top. Plus, condensation on the sensor routinely caused measurement errors.
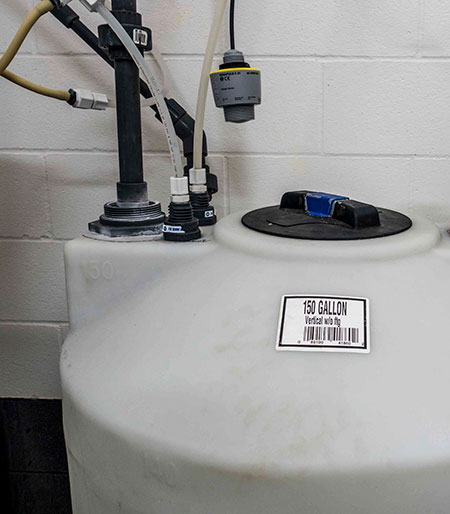
Installing an 80-GHz radar sensor eliminated these problems. All radar sensors use microwaves, which can penetrate the polypropylene material the vessel is made of. This feature lets the installers simply hang the radar above the tank and make a measurement without opening the vessel or creating a new process connection.
No two collections systems, wastewater facilities, or drinking water plants are identical, but many use similar processes requiring similar measurements.
Operators need reliable measurements to run pumps smoothly, maintain inventory of chemicals and additives, and measure how much water is moving through the treatment facility. In some cases, radar level sensors are the reliable technology that operators need to carry out these operations.