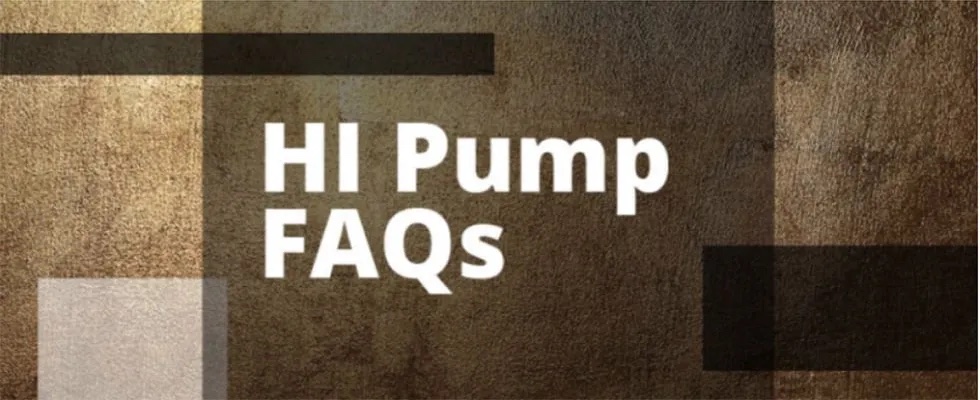
Boiler feed pumps are used to inject water into a pressurized boiler, and the application considerations can vary widely depending on the design and purpose of the boiler. For example, a residential boiler will use a much different pump than a boiler used for large scale power generation. Here we’ll focus on the latter, but even within power generation, there are differing plant designs and generating capacities that result in a wide range of flow rates, pressures and temperatures, all of which will affect the pump selection.
Coal-fired power plants can generate more than a megawatt and typically have a pair of boiler feed pumps, but in some cases a single boiler feed pump is used. In these applications, the boiler feed pumps used are highly engineered and are some of the largest pumps in the world from a power perspective due to the high flow rate and differential pressure requirements.
Combined cycle power plants use gas turbines to generate electricity, plus a steam cycle (boiler and steam turbine) that leverages the high temperature exhaust gas. The generating load of the combined cycle power plant can be as large as a coal-fired plant, but since it utilizes multiple methods for generating, the boiler feed pumps can often be lower flow rate and differential pressure than the coal-fired plant.
The most common pump types used for boiler feed service are between bearing multistage pumps that are axially split (BB3), radially split single casing (BB4) and radially split double casing types. For a summary of pump type descriptions and definitions, visit datatool.pumps.org. BB3, BB4 and BB5 pumps used for boiler feed service will be custom engineered for the application, so when selecting a boiler feed pump, it will be done in consultation with the pump manufacturer and will consider a variety of factors, such as the steam generating capacity, temperature and pressure requirements, material compatibility and maintenance requirements. Additionally, how the pump will be operated is an important consideration to discuss with the manufacturer. From an operational standpoint, four important considerations are whether the pump is required to run in hot standby, typical load swings, the frequency of its startups and shutdowns and cold starting requirements.
Hot standby refers to when a pump is kept ready for operation when not in use, avoiding a cold start. In hot standby operation, the boiler feed water remains close to operating temperature and is continually recirculated, allowing the plant to react quickly to load demand.
Load swings refer to the variations in the demand on the pump involved with day-to-day operation. A combined-cycle natural gas plant will typically operate at several load points throughout a 24-hour cycle. In this case, the pump selected will be designed to accommodate load swings reliably, and the control system should facilitate meeting the different load points while maintaining optimum efficiency and reliability.
Frequent shutdowns and startups can be stressful on a pump’s internal components and may result in faster wear compared to continuous or hot standby operation. Additionally, frequent cycling of large motors can cause them to fail. The materials of construction, internal design clearances and motor starting methods can be optimized to mitigate the stress and wear caused by starting and stopping the pump.
A cold start refers to starting the pump when the system is at or near ambient temperature. Like the considerations taken for frequent shutdown and startup operation, pumps that will be subject to cold start conditions can be pre-warmed, warmed slowly and are designed with materials that have limited growth and contraction due to temperature.
These considerations are only a small part of the process of selecting a boiler feed pump for power generation applications. For more information on the subject of power plant pump selection, please consult the HI Power Plant Pump Guideline for Application and Operation, available at pumps.org/guidebooks.