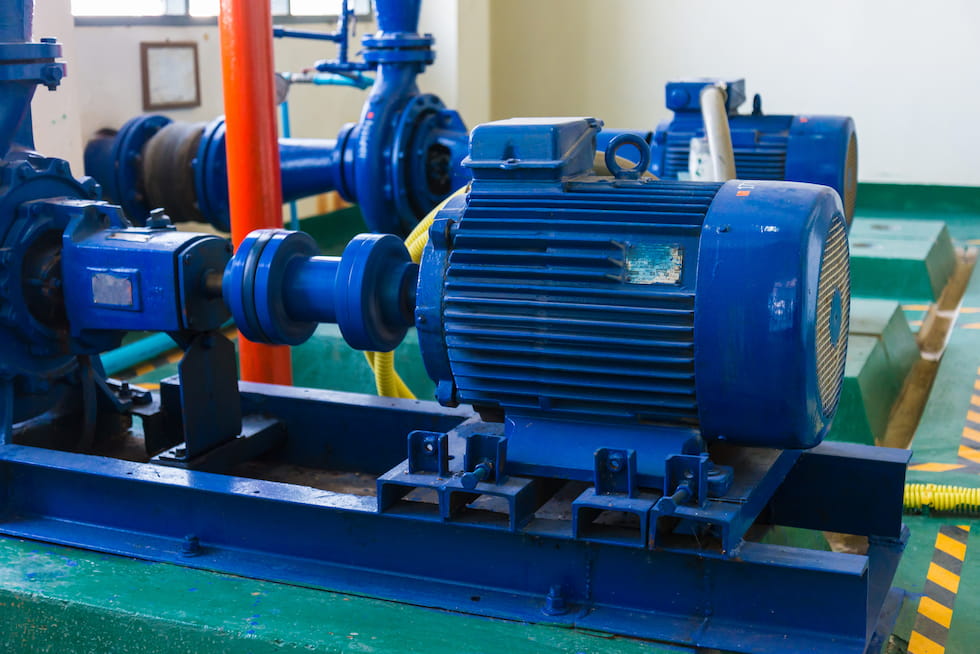
The presence of hydrogen sulfide (H2S), even in trace amounts, and water in a product can lead to sulfide stress cracking (SSC) and hydrogen-induced cracking (HIC) in standard materials used in the production of centrifugal pumps.
This cracking can lead to catastrophic failure of the component. Proper material selection to control SSC and HIC is addressed in National Association of Corrosion Engineers (NACE) standard MR0103 and MR0175. This article establishes standard materials for use in building wetted components for pumps in H2S service. In general, materials used require reduced hardness and strength of the selected material.
While other materials may be acceptable, the ones listed will work for all API 610 material classes. Note that the difference in wet and dry H2S is the presence of water.
It is the user’s responsibility to specify the amount of wet H2S that can be present in the product and if the amount present invokes the NACE standard. If reduced hardness and strength material is specified, the material required will be in accordance with NACE MR0103 or NACE MR0175.
Although it is the responsibility of the purchaser to specify if reduced hardness materials are required, even small amounts of H2S are sufficient to require materials resistant to sulfide stress-corrosion cracking.
If there is any question as to whether reduced hardness materials are required, they should be used as a fail-safe to prevent possible failure of the equipment.
NACE MR0103 or MR0175 apply to different operations. NACE MR0103 applies to oil refineries, liquefied natural gas (LNG) plants and chemical plants. NACE MR0103 applies to materials potentially subject to sulfide stress-corrosion cracking.
NACE MR0175 applies to material potentially subject to sulfide and chloride stress-corrosion cracking in oil and gas production facilities and natural gas sweetening plants.
Reduced-hardness ferrous materials not covered by NACE MR0103 or NACE MR0175 must have yield strength not greater than 90,000 pounds per square inch (psi) and hardness not greater than Hardness Rockwell C (HRC) 22 (234 Brinell Hardness Number [BHN]). Components that are fabricated by welding are to be post weld heat treated, if required, so that both the welds and heat-affected zones meet the yield strength and hardness requirements.
Reduced hardness materials are to be provided for the following components, as a minimum:
- pressure casing
- shafting (including wetted shaft nuts and components)
- pressure-retaining mechanical seal components (excluding the seal ring and mating ring)
- wetted bolting
- bowls, columns and spiders
Notes:
Double-casing pump inner-casing parts that are in compression, such as diffusers and inner case assemblies, are not considered pressure-casing parts.
Casing bolting for pumps with axially split casings (such as API 610 BB1 and BB3) are not considered to be wetted.
Renewable impeller wear rings that are through-hardened must not have a hardness greater than HRC 22 (234 BHN). Renewable impeller wear rings that are either hard-coated or surface-hardened may be used if the hardness of the substrate and transition zones have a hardness no greater than HRC 22 (234 BHN).
Integral wear surfaces on the impellers may be surface-hardened or hardened by the application of a suitable coating in lieu of furnishing renewable impeller wear rings if their substrate material hardness is not greater than HRC 22 (234 BHN). In all material grades, variations containing alloying elements such as lead or sulfur to improve machinability are not allowed.
Cast Iron
Cast iron is acceptable for wear parts for API material class S-4. The common standard for this material is American Society for Testing and Materials (ASTM) A48 Class 30 and CIass 40.
Ni-resist
Ni-resist wear rings may be used for API class S-5 and S-6. When Ni-resist is specified, use ASTM A436 Type 1 for the stationary wear parts and ASTM A436 Type 2 for the rotating parts. Ni-resist parts should not be used where the differential pressure is greater than 350 psi.
Carbon Steel
Carbon steel is acceptable but must meet the hardness requirement of RC22 (248 BHN) and requires stress relief after welding regardless of how small the weld. The standard material class is ASTM A216 Gr. WCB. Generally, carbon steel bar stock is not acceptable because the low hardness requirement reduces the strength to such a low level that it will not work for most applications. In instances where strength is not important, it may be used as long as it meets the hardness and post weld heat treatment (PWHT) weld requirements.
Martensitic Stainless Steel
ASTM 479 type 410 is acceptable at RC22 (248 BHN) maximum hardness provided it has this three-step heat treatment:
- Austenitize and quench or air cool.
- Temper at 621 C (1,150 F) minimum, then air cool to ambient temperature.
- Temper at 621 C (1,150 F) minimum but lower than the first temperature; then cool to ambient temperature.
ASTM A CA6NM is acceptable at RC23 (255 BHN) provided that the material has been heat treated in accordance with the steps below:
- Austenitize at 1,010 C (1,850 F) minimum and air or oil quench to ambient temperature
- Temper at 649 C to 691 C (1,200 to 1,275 F) and air cool to ambient temperature
- Temper at 593 C to 621 C (1,100 to 1,150 F) and air cool to ambient temperature
Austenitic Stainless Steel
Austenitic stainless steel with the chemical composition shown in Image 1 is acceptable at a hardness of RC 22 (248 BHN) maximum in the solution annealed and quenched or solution annealed and thermally stabilized condition.
Cold work to enhance the mechanical properties is not permitted. Pulsate hydrotest for multistage pumps is acceptable as it is used to stabilize the material and does not enhance the mechanical properties.
ASTM A479 type XM19 (Nitronic 50) is acceptable in the solution annealed, hot rolled (hot/cold worked) or cold worked condition at RC 35 (327 BHN).
Duplex Stainless Steel
Wrought and cast duplex stainless steel is acceptable in the solution annealed and liquid quenched condition. Allowable hardness number is related to the pitting resistance equivalent number (PREN). The PREN number can be calculated by using the formula in Equation 1.
For duplex stainless steels, the ferrite content must be controlled between 35% and 65% by volume. Aging heat treatments to increase mechanical properties are prohibited due to the formation of embrittling phases.
Super Duplex
Super Duplex, ASTM A890 grade 5A is advised for both D-1 and D-2 grades because it is the only material acceptable to both NACE MR0103 and MR0175.
Standard Duplex, ASTM A890 grade CD4MCuN is acceptable for D-1 applications when NACE MR0103 is specified. It is not acceptable for NACE MR0175.
Precipitation-Hardenable (PH) Stainless Steel
ASTM A747 CB7Cu-1 Condition H1150M (17-4) is acceptable at a hardness of RC 33 (327 BHN). Users
should make sure that the material is heat treated according to the following procedure:
- Solution anneal 1,140 +/- 14 C (1,900 +/- 25 F) and air cooled or suitable liquid quench to below 32 C (90 F).
- Harden at 621 C +/- 14 C (1,150 F +/- 25 F) for four hours minimum at temperature and cool in air to below 32 C (90 F).
- Additional cycles at 621 C +/- 14 C (1,150 F +/- 25 F) may be used if required to produce an acceptable hardness level.
More Notes on Materials
A. Material must be furnished with a HRC 22 (234 BHN) maximum hardness. Any welding done to the casting or for fabrication must be post weld heat treated (PWHT) regardless of how minor the weld is. If a vendor’s stock casting or fabrication is used, it must be PWHT prior to use because of the possibility that minor welding was done at the foundry and not subsequently heat treated.
B. CA6NM castings are acceptable at HRC 23 (240 BHN) provided they are three-step heat treated to the following:
1. Austinitize at 1,850 F minimum and air or oil quench to ambient temperature
2. Temper at 1,200 to 1,275 F and air cool to ambient temperature
3. Temper at 1,100 to 1,150 F and air cool to ambient temperature
C. Ni-resist wear rings are acceptable as long as the user approves. Use ASTM A436 Type 1 for the stationary wear parts and ASTM A436 Type 2 for the rotating parts.
D. The microstructure for duplex stainless is a critical variable and must be documented. The ferrite content is to be between 35% and 65% by volume. If the pitting resistance number (PERN) is above 40% for the material, the hardness is limited to HRC 32 (318 BHN) maximum.
E. ASTM A564 Type 630 condition H1150 (17-4 PH) is an acceptable substitute for Nitronic 50 at RC33 (327 BHN) when heat treated to the following criteria:
1. Solution anneal at 1,038 C +/- 14 C (1,900 F +/- 25 F) and air cool or suitable liquid quench to below 32 C (90 F)
2. Harden at 621 C +/- 14 C (1,150 F +/- 25 F) for four hours minimum at temperature and cool in air to below 32 C (90 F)
3. Harden at 621 C +/- 14 C (1,150 F +/- 25 F for four hours minimum at temperature and cool in air
4. Additional cycles at 621 C +/- 14 C (1,150 F +/- 25 F) may be used if required to produce an acceptable hardness level
F. ASTM A890 grade 5A is specified for both D-1 and D-2 grades This material is acceptable to both NACE MR0103 and MR0175. Standard duplex, ASTM A890 grade CD4MCuN is acceptable for D-1 applications when NACE MR0103 is specified. It is not acceptable for NACE MR0175.
G. ASTM A790 gr. S31803 may be used for duplex (D1) if the reduced strength resulting from the reduced hardness required by NACE (279 BHN) is acceptable for the design.
H. ASTM A240 gr. S31803 may be used for duplex (D1) if the reduced strength resulting from the reduced hardness required by NACE (279 BHN) is acceptable for the design.
References
1. API 610, 12th edition
2. NACE MR0103, Standard Material Requirements, Materials Resistant to Sulfide Stress Cracking in Corrosive Petroleum Refining Environments
3. NACE MR0175, Standard Material Requirements, Sulfide Stress Cracking Resistant Metallic Materials for Oilfield Equipment