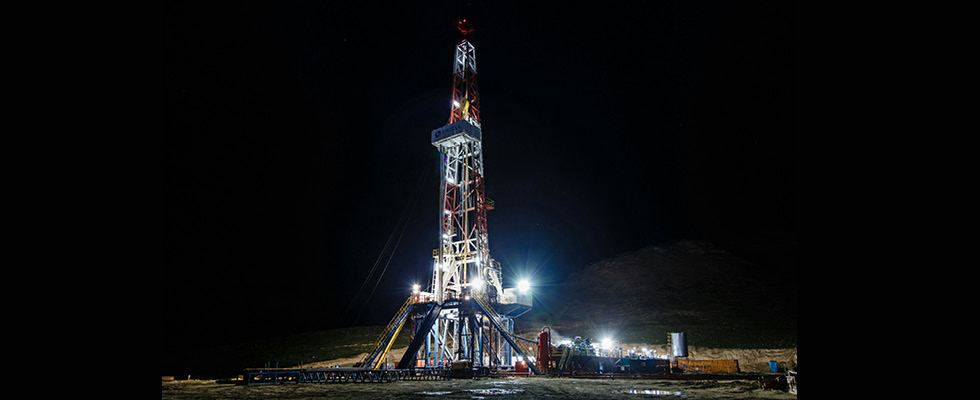
Oil seals are essential components in systems with rotating and moving parts, playing a vital role in various applications within the oil and gas industry—including valves, actuators, pumps, mixers and subsea operations. In oil and gas machinery, these seals are critical for ensuring smooth operation and serve three important functions.
First, they prevent the leakage of lubricants or fluids, even in high-pressure conditions. This is vital for ensuring the effective operation of the equipment, as proper lubrication is essential for the machinery to function smoothly.
Second, oil seals help retain lubricating oil within the machinery. This retention minimizes the need for constant maintenance or relubrication, which saves both time and resources.
Lastly, oil seals act as a barrier against contaminants, preventing dirt, dust and other impurities from entering the machinery. This protection is important for safeguarding sensitive components from damage or wear.
An oil seal generally consists of an outer circular metal part and an inner flexible member that does the actual sealing and is bonded to the metal part by chemical adhesive agents. The collaboration of these parts results in the seal’s functionality and effectiveness. A garter spring may also be included as an available feature, providing an extra layer of operational support.
Depending upon the application, oil seals can be made from a vast range of materials. Two of the most popular materials used to manufacture oil seals include nitrile butadiene rubber (NBR) and fluorine kautschuk material (FKM).
NBR offers excellent resistance to a wide range of petroleum-based oils, greases and fuels, making it the most commonly used material for oil seals due to its good balance of properties like high abrasion resistance, low compression set and a wide operating temperature range of -40 F to 226 F (-40 C to 108 C).
FKM compounds also offer a wide operating temperature range varying from 40 F to 400 F (4 C to 204 C). They are considered the premium materials for lip seals and are highly resistant to chemicals and abrasion.
If a seal breaks during oil and gas pumping operations, it can lead to many significant and disastrous outcomes including leaks, major environmental disasters, safety hazards for workers and substantial financial losses for the operator.
The consequences of seal failure extend beyond immediate operational disruptions, potentially resulting in long-term environmental damage and reputational harm to the company involved. Therefore, taking preventative measures to avoid oil seal failure is essential for maintaining operational integrity, corporate responsibility and community trust.
Avoiding Oil Seal Failure
In the oil and gas industry, oil seals commonly fail at the pump due to factors like extreme temperature fluctuations, excessive wear from abrasive particles, chemical degradation from harsh fluids, improper installation, misalignment, high pressure, contamination, aging of the seal material and mechanical damage from vibrations or impacts—all of which can lead to the seal losing its sealing ability and causing leaks.
When seals leak, various indicators can reveal the underlying causes. Signs include grooving from contamination, swelling and deterioration due to exposure to incompatible media, hardening from low temperatures and scarring from installation damage. Wear may manifest as shiny surfaces from inadequate lubrication, while extrusion occurs when seal edges protrude due to overpressurization. Fractures, such as cracks or missing pieces, typically result from weak materials subjected to extreme conditions.
To ensure effective pump operations and safeguard against seal failures, oil and gas operators should consider the following four essential tips:
Select appropriate seals
Choosing the right seals is crucial for operational safety and efficiency. Operators should select seals made from high-grade materials that can withstand the conditions encountered in their operations. It is also important to account for the design of the shaft and ensure the selected seals have the correct size and lip configuration. This tailored approach will enhance the seal performance and longevity.
Proper installation
The installation process is a critical phase that directly impacts seal performance. Before installation, ensure all surfaces are meticulously cleaned and free of any contaminants that could compromise the seal’s effectiveness. Using the proper installation tools is vital to avoid damaging the seal during placement. Furthermore, applying appropriate lubrication to the seal lip and shaft not only facilitates easier installation but also reduces friction during operation, contributing to better seal life.
Preventative maintenance
Regular maintenance is key to identifying potential seal issues before they escalate into major problems. Organizations should establish a routine inspection schedule to assess seals for signs of wear, damage or leaks. It is recommended to replace seals proactively based on the manufacturer’s guidelines or considering the specific usage conditions encountered in the field. Additionally, maintaining a clean system is essential. Debris accumulation can shorten seal life span and effectiveness, so routine cleaning should be part of the maintenance protocol.
Monitoring and early detection
Implementing robust monitoring systems plays a major role in early detection of potential seal issues. Tracking critical operating parameters such as pressure, temperature and fluid levels can provide valuable insights that indicate whether or not seals are functioning as they should. Early detection systems help identify leaks at an early stage, minimizing the risk of catastrophic failures. Regular data analysis and trend monitoring can also aid in forecasting potential problems, allowing for timely interventions.
By prioritizing these essential practices, oil and gas operators can reduce the risk of seal failure at the pump and its associated consequences. Creating a culture of safety and diligence within an organization not only protects the workforce and the environment but also ensures sustainable operational efficiency and profitability in the long run.