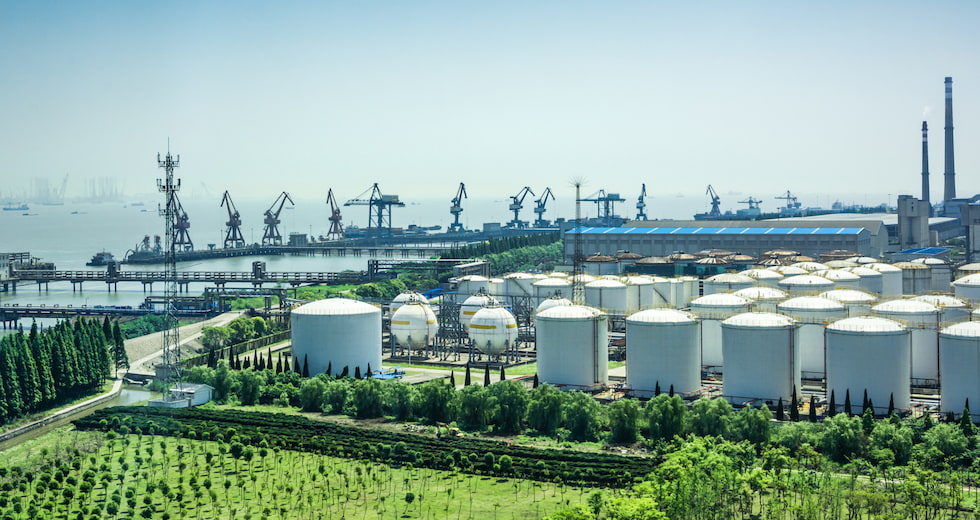
Specialty chemicals are essential in the oilfield. For example, chemicals are used to prevent corrosion, an expensive problem that costs the United States economy around $1.1 trillion every year. Chemicals are applied in the form of biocides to mitigate bacterial growth that would otherwise foul surfaces and pipelines. Oilfield companies also trust chemical scavengers to neutralize poisonous substances and byproducts, like hydrogen sulfide (H2S), which killed 60 U.S. workers between 2001 and 2010. Furthermore, chemicals promote high-quality oil production by enabling operators to remove contaminants like basic sediment and water (BS&W) from core processes.
Beyond these use cases, there are other ways users rely on specialty chemicals to ensure asset integrity, maintain production throughput, promote a safety culture, and more in the oilfield. However, these outcomes cannot be achieved without effective chemical management programs.
The ultimate goal of chemical management is to deliver precise concentrations of chemicals when needed according to specific process parameters. Chemical pumps are needed to inject the right chemicals, at the right times, to the right places.
The Problem
Today, most chemical injection management processes happen manually. In many cases, chemical account technicians still drive out to the field to change pump set-points by hand based on process readings they collect themselves or receive from operators through weekly or monthly reporting.
The problem with this approach is that it does not align with the dynamic nature of oilfield processes. By the time chemical service technicians arrive on-site, their changes are already outdated. As a result, chemical rate updates rarely address current-state field conditions appropriately.
Chemical pumps are prone to failure through several different modes, which can add further complications. Mechanical issues, power outages and network connectivity challenges are just a few problems that can prevent injection pumps from treating assets properly and on time.
Though a little downtime might seem inconsequential, the results can be catastrophic. When corrosion, bacteria and other byproducts build up, infrastructure fails, wells go offline, pipelines lose sales permissive or, worst of all, people get injured. These situations can rack up significant costs. In 2010, the Occupational Safety and Health Administration (OSHA) proposed over $1.4 million in penalties against Houston-area oil and gas companies after a fatal explosion. This is just one example of how such an event can impact financial outcomes.
Chemical management data adds further context to this sobering reality. Out of thousands of oilfield chemical injection sites the company surveyed in 2020:
- Three-fourths of individual injection pumps missed targets by more than 20%
- One in 15 chemical injection tanks were empty at any given time
- Over half of chemical pump downtime events lasted over 24 hours
- Four in five oilfield assets were left untreated or severely undertreated for more than 24 hours
This data shows that operators are struggling to stay on top of chemical management programs. Chemical treatment is not working as designed, and it is creating challenges in the oilfield.
Despite the best efforts of chemical services companies, chemical performance does not meet modern expectations. Every oilfield producer, transporter and refiner knows that chemicals are needed to sustain their operations, yet few can prove their effectiveness with a hard and fast return on investment (ROI).
Even fewer can trust their chemical programs to respond dynamically to real-world conditions. Many oilfield companies treat chemical management as a necessary evil rather than as an opportunity to create incremental value.
With the rise of Industry 4.0 and the industrial internet of things (IIoT), there is a better way to manage and monitor dispersed chemical injection pumps.
The Solution
Oilfield companies today can leverage advances in pump monitoring, control and automation enabled by IIoT to maximize chemical program effectiveness.
Through chemical injection pump automation, operators can set programs to run independently based on real-time process parameters.
For instance, users can configure upstream injection pumps to release more chemical scavenger whenever downstream readings show concentrations of H2S above permissible limits. Users can use remote monitoring sensors and then they will be informed when chemical tanks are near empty so crucial treatments are not missed. If chemical tanks do go empty, thus creating air-locked pumps, chemical pump automation systems can even purge injection lines remotely to restore injection.
Rather than send chemical account technicians on-site to make adjustments or take measurements, pump automation technology can be trusted to do this almost instantaneously. Chemical technicians are free to focus on higher-value activities. More importantly, by reducing reliance on manual labor, the likelihood of human error or safety incidents occurring is decreased.
Through automation, injection variances can be minimized.
Existing implementations reveal that automation can lower injection variance to less than 5% above and below expected targets. And when chemical treatments align with operational requirements, oilfield companies spend only what they need on chemicals.
Zooming out, it can be seen how automation solves major operational problems in the oilfield. With chemical program automation, companies can extend the lifetime of critical production infrastructure, cut down on systemic pump downtime, prevent leaks, neutralize poisonous gases, maintain throughput and produce high-quality hydrocarbons. Leaders do not have to worry as much about unexpected remediation costs hitting their profit and loss (P&L) statement year after year.
Moreover, sophisticated pump control solutions come with prepackaged monitoring capabilities that generate rich data for further processing. Automated data streams can prove the ROI of chemical management programs and validate that chemical treatment is working as designed. Usage and overspending by chemistry, asset, region and provider can be tracked and which chemical management programs provide the best value can be identified.
So, not only can oilfield companies improve corporate responsibility and organizational performance, but they can also make informed decisions that were previously less clear.
Chemical pump monitoring, control and automation is the key to unlocking new sources of value and eliminating waste from everyday operations.
A New Way of Doing Things
Effective chemical management is not out of reach. Oilfield companies do not have to keep doing things the way they have been doing them for decades. Manual labor is falling short, given the dynamic nature of chemical processes. Chemical pump automation makes life easier for operators and service providers without adding overwhelming technical complexity.
Some digital-forward thinkers are already moving down this path. It is expected that by 2025, more than half of oilfield chemical injection pumps will be automated, thanks to the adoption of remote monitoring technology in the industrial sector.
Now may be the time to consider making an automation investment.