In today’s industrial world, selecting a chemical pump from the various pump technologies and brand names can seem like an endless array of choices. With so many different benefits, sizes, materials and other features available, choosing the best pump can be overwhelming. Deciding between electrically driven pumps, such as centrifugal or peristaltic, versus pneumatically driven pumps, such as air driven double diaphragm pumps, can be a difficult choice for chemical pumping and transfer applications throughout a plant. A technology that has recently been introduced provides a new tool to a user’s toolbox when trying to select the right pump technology for chemical pumping applications. The electric double diaphragm pump has combined the well-known diaphragm pump technology with the control and energy-saving benefits of electric drives. This new technology also offers some unique advantages.
Worker & Plant Safety
One of the most important considerations when weighing options for different pumps is making sure the plant environment is safe for all workers by preventing leaks or pump failures, which could risk human contact with harmful chemicals. Many typical electric rotary pumps employ a shaft seal that will wear over time and can allow corrosive and dangerous chemicals to leak onto the floor and expose workers to the dangers of contact with the chemical or inhalation risks due to fumes. This can be especially true if the chemical being pumped contains any particulates that could expedite seal wear within the pump.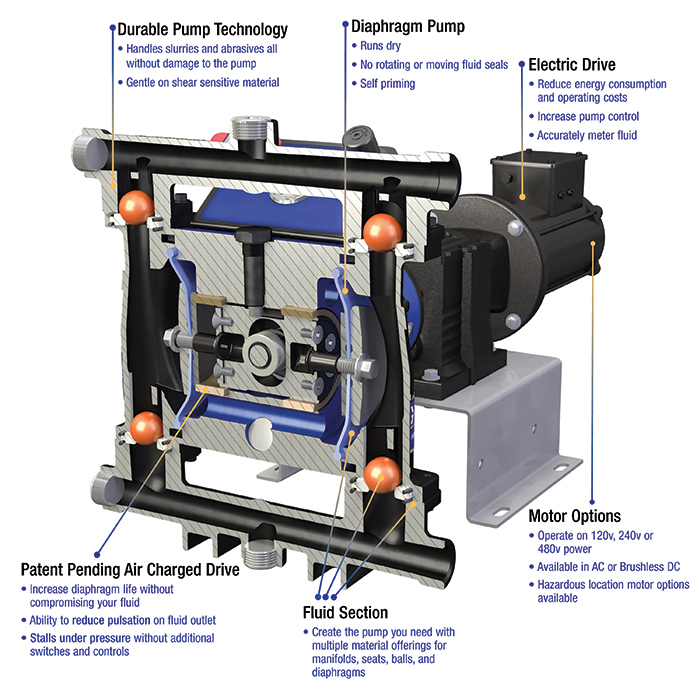
Material & Chemical Considerations
Another important consideration for users is what type of chemical or media they are looking to transfer in their process. If it is a clean chemical without any particulates, then standard centrifugal style pumps are a great solution at a reasonable price point, depending on the materials of construction. If the chemical contains any particulates, is a chemical slurry or is potentially a waste chemical with unknown matter in the fluid, centrifugal pumps may struggle and have frequent breakdowns because they cannot handle the solids in the fluid very well. The particulates will damage seals, impellers and bearings, forcing pump repairs or replacements frequently. Apart from the “cleanliness” of the chemical, as most users know, it is imperative to ensure that the pump materials of construction are compatible with the chemical that they are trying to pump. These days, most pump styles offer different options to accommodate different chemicals, but it is always important to check to ensure no issues will arise. Aside from the main components, it is important to check rotary pumps for bearings, seals or other components within the pump for compatibility with the chemical. Often times main housings, impellers, rotors or other items are compatible, but ancillary components within the pump may not be the right match for the chemical.Process Operation
Verifying that the pump and chemical will work well together is usually step one in the pump selection process. Step two is verifying that the pump fits well into a process. Many items need to be considered for this part of the selection to make sure the right pump is installed. The first considerations at this stage are generally flow rate and pressure required. For high flow applications, centrifugal pumps are hard to beat. They can also be staged to achieve higher head pressure where required. For lower flow rate applications or higher pressure applications, users will probably enter the realm of positive displacement pumps: rotary lobe, gear, peristaltic and progressive cavity, for example. Although the positive displacement style pumps generally do not provide as high of flow rate as their centrifugal counterparts, they offer the ability to accurately measure flow (meter) since they are positive displacement. If this is important to an application, it can be a deciding factor. The drawbacks to most of the above technologies are key points that double diaphragm pumps have been solving for years. If the pump must pull suction, most of the above pumps are not a good fit. If stalling under pressure is an important feature due to a dispense valve inline, process valve that may close or the highly likely event of a clogged line with slurries, diaphragm pumps offer the ability to stall the pump under pressure without damage.Electric Diaphragm Pump as a Solution Option
For years the only way to power a double diaphragm pump has been with pneumatic pressure to the pump, which can be limiting in some circumstances. For example, air capacity in a facility could be taxed by all other processes, air could be unavailable at a location or facilities could be looking to capitalize on the lower operations cost of electric. Fortunately, it is now possible to use the double diaphragm pump technology for chemical pumping without the requirement of large air compressors to power the pump. New electric diaphragm pumps remove the worry of worker and plant safety that other pumps have. The double diaphragm style pump is the same sealless design that is used on the air driven model discussed earlier, but electric pumps are not driven by compressed air. This means in the event of a diaphragm failure, the chemical will not enter an air motor and will not be pumped out the exhaust as previously discussed.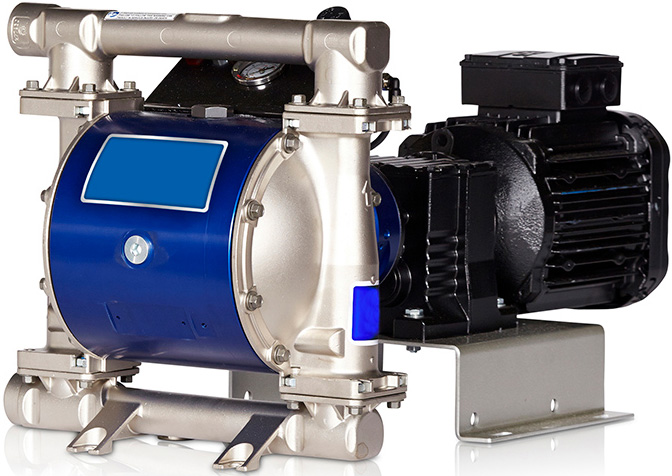