When considering the relationship of variable frequency drives (VFDs) with well water applications and the efficiencies they bring, a measure of success depends on the working definition of the word “efficiency.” Often, the actual benefit gained by applying VFDs to these applications is energy savings, not an increase in efficiency. What’s the difference? Efficiency is defined as the result produced compared to the energy put in and is governed by component design. Energy savings is using less than 100 percent of the capacity of the system and thereby reducing energy costs when compared to running at 100 percent. Energy savings requires excess capacity in the system for part of the operational time of the application. The efficiency of a pump is generally calculated and compared to other designs at the rated speed of the pump. Pump efficiency is conditional on the design parameters such as impeller shape and diameter, volute or bowl shape, pump type, and total dynamic head all measured at a fixed pump speed. It is important to select the best efficiency, as this will affect the electrical energy required to run the pump. The overall cost of energy for a given gallons per minute (gpm) flow is commonly referred to as the wire-to-water ratio. While it may be more expensive to gain an increase in efficiency, even a small increase of percentage points can be paid for in energy savings in a few years of operation. All of the conditions of a new application must be factored into the selection of the equipment to have the capacity to supply the current application. Other factors should be taken into account when engineering the system that will deliver water. The ground water geology, screen size, gravel pack, static water level and initial well development must be considered when selecting components. All of these parts of the water delivery system affect efficiency, capacity and overall wire-to-water ratio. Once these components are in place, it is expensive and impractical to change them. Today’s water applications generally have to deal with one or more system variations such as declining water pumping level and changing demand, which is why it is beneficial to have some excess capacity. Centrifugal pumps offer an efficient way of dealing with reduced demand by reducing the speed of the pump, easily accomplished with a VFD. To understand how speed reduction works to accomplish energy savings, it is useful to look at the graphs for the Laws of Affinity, which govern centrifugal fans and pumps. It has been known for some time (100-plus years) that centrifugal fans and pumps follow the Laws of Affinity as they relate to the operation of the impeller across the speed range. It was found that the flow of a given impeller diameter will increase in proportion to the speed of the impeller, while the pressure developed will increase at the square of the speed. The power required to rotate the impeller will increase at the cube of the speed. So, the relationship of pressure and power is non-linear compared to changes in rotational speed.
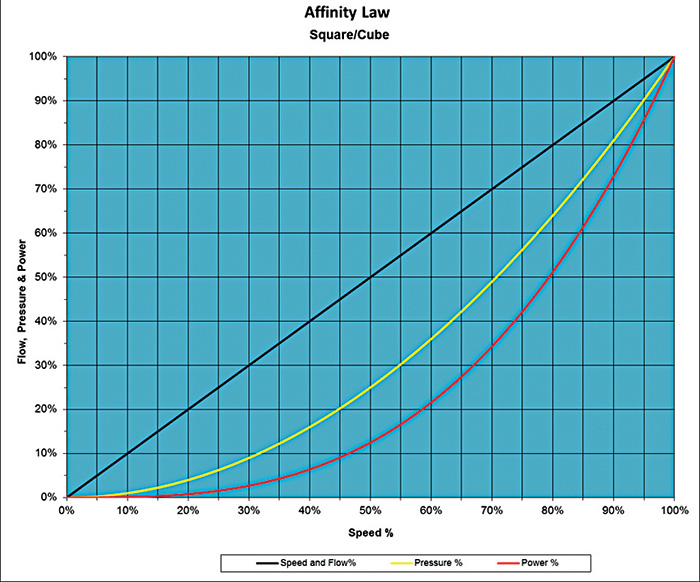
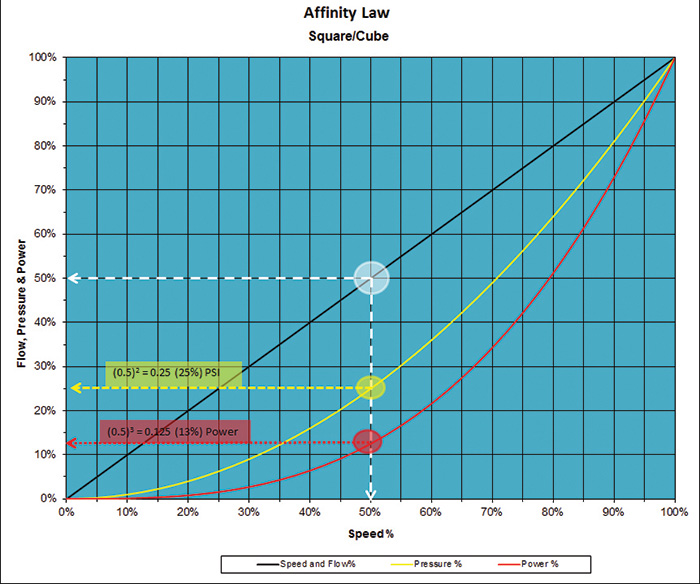
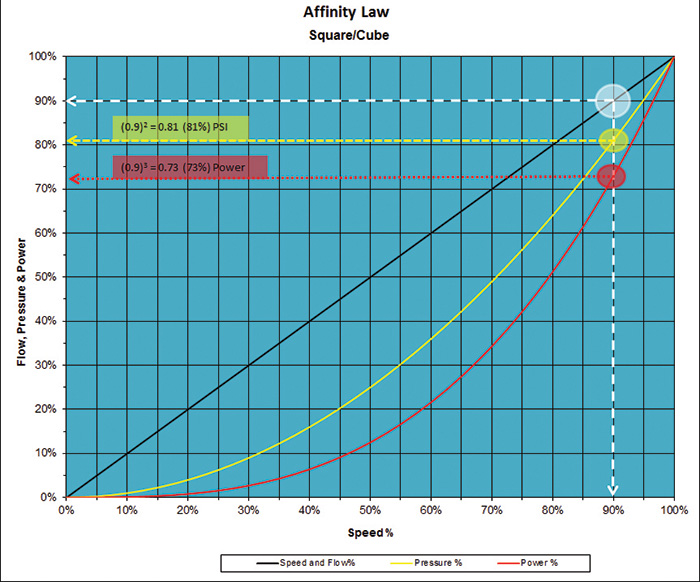
- soft starting reduces wear on all mechanical parts of the system
- soft starting also reduces water hammer
- high reliability with solid state construction
- point for a variety of sensors to measure process operations
- scalability and functions can be added or altered in the future
- programmable pump protection features
- motor protection features