In today’s market, end users are always demanding more from their pumps. New technologies must meet specific system requirements, keep maintenance costs low, ensure long product life and save energy. Manufacturing companies face increasing costs for material and energy in a market that has become competitive on a global scale. As industrial, agricultural and pharmaceutical applications become more complex, manufacturers strive to keep up by designing more advanced equipment and filling the market gap as quickly as possible. Few manufacturers know the installation or application environment before designing their pumps. Desert or ocean, high-density seawater or freshwater—the challenge for designers is to build a product that can adapt to multiple applications while still meeting requirements. This calls for proper product validation and verification.
3-D Simulation
The application scope of virtual 3-D simulation includes nearly every stage of the product development and manufacturing process.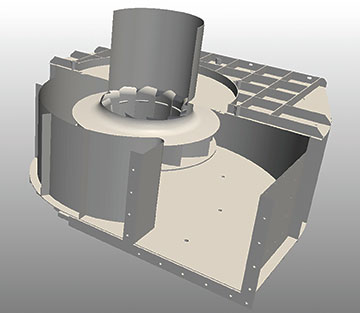
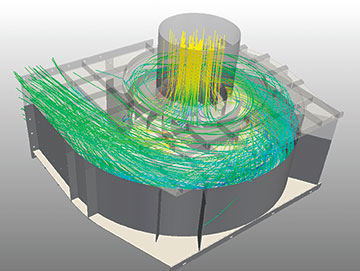
Financial & Operational Challenges
Despite the benefits of this technology, only a fraction of companies invest time and money in 3-D simulation software. High financial and technical barriers often stand in the way of purchasing, installing and configuring the software for a particular application. Companies are often forced to buy a long-term software license, even if the testing only involves minor design changes in the scope of a few months. Many simulation methods require so much computing power that large computers or computer clusters must be purchased. This increased capacity often requires a larger information technology (IT) staff or even training for simulation specialists.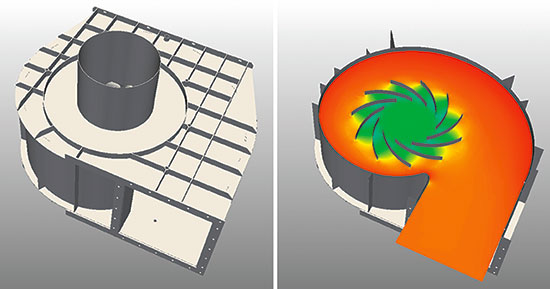
The SaaS Advantage
Cloud-computing allows manufacturers to access modern IT infrastructure without the burden of fixed expenses. Instead, the cloud-computing service provider takes care of infrastructure setup and maintenance. The delivery of software by a service provider is called software as a service (SaaS). The purpose of the SaaS model is to cut costs and overcome IT hurdles. In the manufacturing industry, the SaaS concept is combined with engineering simulation to run structural and fluid flow simulations. These simulations adjust test conditions according to density, fluid viscosity, inlet velocity and rotation speed.
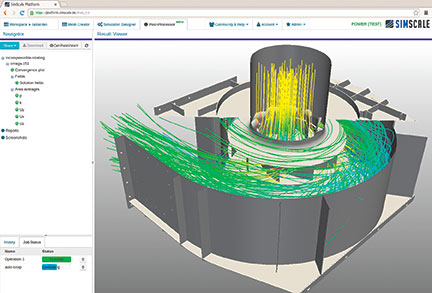
Design Changes & Simulation
The main objective of the design changes was to increase the volume flux through the fan. However, this increase had to respect the fan’s power consumption limits and minimum pressure increase. The engineer uploaded the computer-aided design (CAD) model of the new design and created a fluid flow simulation (see Figure 1). The computation was carried out on multiple 16-core machines. The rotating domain in the middle of the design and the relatively large simulation model required considerable computing power. The availability of large computing instances allowed the results to be analyzed after only one hour per simulation. The integrated post-processing environment of the software then allowed direct 3-D access to the simulation results. Figure 2 shows a streamline visualization of the velocity field within the fan housing.Results
Using data on the new design’s pressure increase and power consumptions, end users were able to accurately predict the fan’s performance. Engineers could wait to manufacture a physical prototype until a later design phase, decreasing the risk of expensive and time-consuming changes later in the process.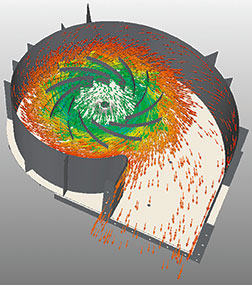
Industry Impact
By outsourcing IT infrastructure and management, pump manufacturers can focus on actual engineering work instead of the installation and maintenance of high-performance computing systems or license servers. Smart Web technologies and modern cloud-computing approaches have become more popular among users in a variety of fields.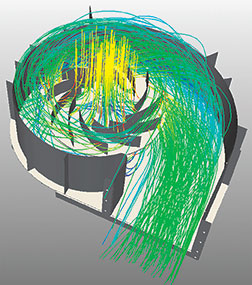