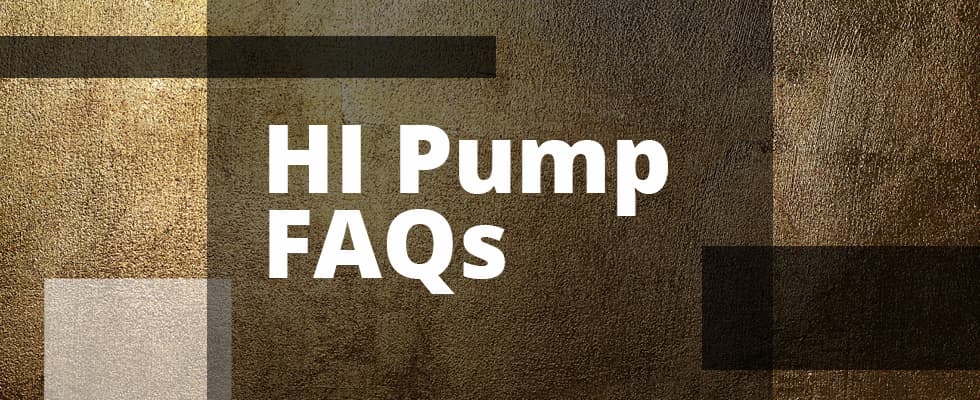
What type of coatings are used to resist wear and corrosion?
Coatings to resist wear and corrosion are extensively used for pump parts requiring greater wear and corrosion resistance than can be obtained from an economic base material. When coating for corrosion resistance, it is important that the coating system is free of porosity. Some commonly used coating systems for wear and corrosion resistance are discussed below.
Cobalt-chromium-tungsten alloy material is one of the first wear- and corrosion-resistant coatings to be widely used for pump parts subject to wear, such as sleeves, wearing rings, plungers, piston rods and valves. These coatings usually provide excellent wear resistance, galling resistance and corrosion resistance to most products. The coatings are often applied to carbon-steel or stainless-steel base metals.
Nickel or cobalt-chromium boron alloy coating material is available in many alloys with different wear and corrosion-resisting characteristics. Some may be applied by spray welding, while others require oxyacetylene or arc welding and are successfully employed on such parts as wearing rings, sleeves, shafts, piston rods and plungers.
Chromium coatings are normally applied by electroplating. This tends to produce porosity in the coating. It is preferable to use a base metal that is resistant to the liquid being pumped. Chromium coatings have strong corrosion resistance to many media, including caustics and compounds of nitrogen. They are usually not suitable for compounds of sulfur and chlorine.
This plating provides a hard, wear resistant, low-friction surface. For reciprocating or rotating parts, these are favorable factors both from the standpoint of wear of the plated parts and service life of the packing. Plungers, liners, piston rods, sleeves and shafts are generally chrome-plated.
Ceramic coatings have been employed for special services; however, these coatings are usually quite porous, which limits their application on sliding surfaces in pump applications, even though a sealer may be used to seal the porosity. Further development may permit more general use of these coatings. It is preferable to use a base metal that is resistant to corrosion by the liquid being pumped. Flame-sprayed carbide or oxide coatings provide high wear resistance but are relatively expensive.
For more information on pump materials of construction and pump coatings, refer to ANSI/HI 9.1-9.5 Pumps—General Guidelines for Materials of Construction, Measurement of Airborne Sound, and Decontamination of Returned Products at www.pumps.org.
Can coatings be applied to increase the efficiency of a pump?
Due to friction loss, the surface roughness of a pump’s hydraulic passages can have a significant influence on pump efficiency. For this reason, considering the casting process, type and quality of the material, post-process finishing and grinding, and application of specialty coatings may be beneficial.
However, the amount of efficiency gain that can be expected is dependent on the pump specific speed (Ns) and size, with smaller and lower Ns pumps seeing greater increases relative to surface finish improvements.
As a point of reference, a low Ns pump (Ns = 500, U.S. units) with a surface finish upgrade from 500 roughness average (Ra) to 200 Ra microinch finish, would have an estimated efficiency gain of 5 percent at the best efficiency point (BEP). A higher Ns pump (Ns = 2,500) with the same surface finish upgrade has an estimated efficiency gain of less than 1 percent.
For more information on rotodynamic pump efficiency, refer to HI 20.3 Guideline for Rotodynamic Pump Efficiency Prediction at www.pumps.org.