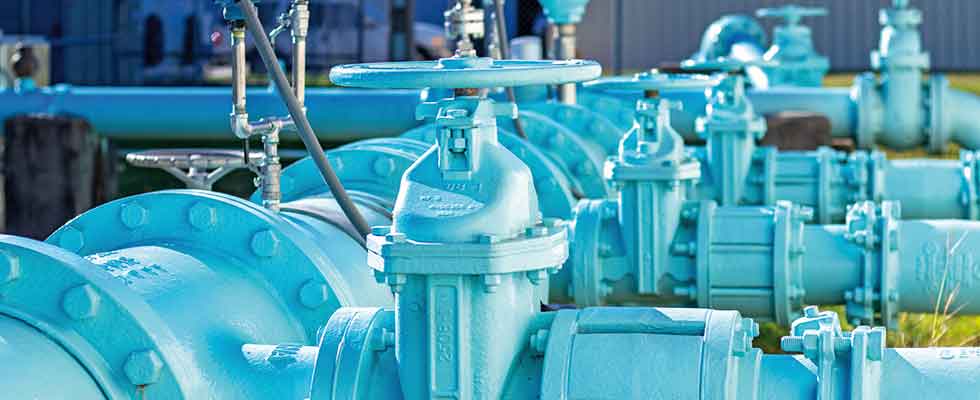
Houston Public Works provides drinking water to its communities through six public water systems. One of the systems, the Willowchase system, provides water to approximately 13,500 people and relies solely on groundwater. Four facilities in the system—Willowchase, Centerfield District 254, Willowbrook District 159 and Willowbrook West District 237—provide an average of 2.1 million gallons per day to customers. Originally, these groundwater facilities, which were constructed more than three decades ago, were operated by municipal utility districts. Later, ownership and operations of these facilities were transferred to Houston Public Works.
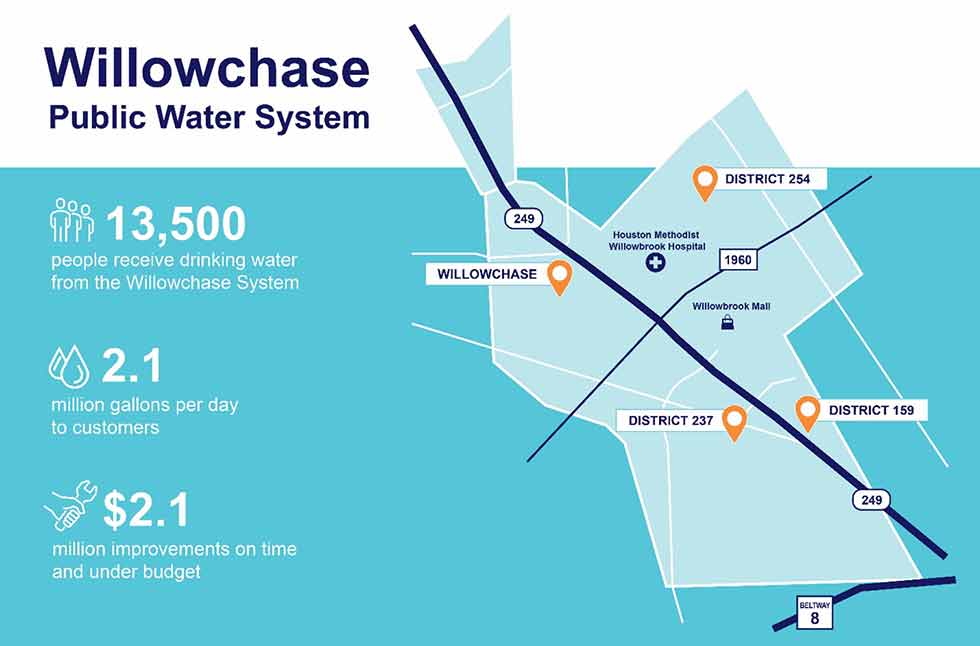
In June 2014, Houston Public Works began implementation of improvements to 11 drinking water facilities, including the four in the Willowchase system, to optimize operations, streamline maintenance activities and replace worn-out and obsolete equipment. A national planning, engineering and program management firm was hired to design these improvements. Specifically, the improvements included replacement/rehabilitation of booster pumps, isolation and control valves, aboveground piping and related appurtenances, as well as electrical and supervisory control and data acquisition (SCADA) components.
To start, the engineering firm performed a comprehensive evaluation of all the facilities in the Willowchase system. The project team reviewed available record drawings, took photos, collected data, carried out site investigations, tested the equipment and performed engineering analyses. In certain cases, the record drawings did not match the site observations. To reconcile the differences, the project team created sketches and computer-aided design (CAD) drawings to develop a basis for the design. The project team also held discussions with Houston Public Works’ operations staff, listened to their concerns, and added the improvements needed at various sites. These included replacing motor control centers to improve reliability, adding butterfly valves to minimize impacts of water line shutdowns, making SCADA changes to meet current standards, and upgrading the drainage at one facility.
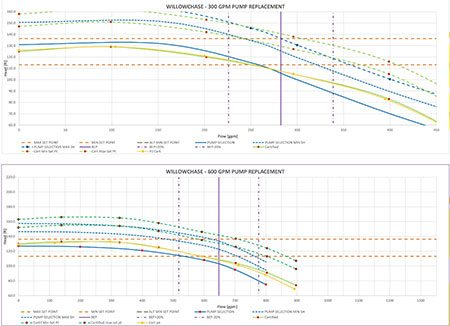
Project Challenges
Once the project got underway, the engineer and the contractor faced numerous challenges. Chief among them was identifying and selecting the right pumps for Houston Public Works’ operating conditions. Typically, newer facilities are designed with expansion in mind and equipment space is provided for future work. But, given the age of these four facilities, engineers had to consider the limited space requirements available. Also, Houston Public Works wanted to replace pumps in-kind, which was not easy given the industry changes that have happened over the last three decades. Specifically, many of the existing installations did not meet current Hydraulic Institute standards for suction inlet piping, requiring piping modifications if space allowed. Also, many of the original installed pump models were no longer available. Most importantly, the pumps for each facility were originally designed to pump water to a distribution system for a specific area of the neighborhood at a specific head condition or pressure plane. Now, the once independent facilities were required to work as part of an integrated system on a common pressure plane.
To satisfy these requirements, the project team modeled the facilities to understand their hydraulic relationship with each other. They also evaluated historical SCADA data to determine the head and flow conditions needed for the pumps. After plotting and analyzing the pump performance curves, the project team recommended against using in-kind pumps and provided pump specifications with the optimum head and flow range.
After installing the pumps on-site, the contractor observed that they were not operating as anticipated. The project team discovered that the Texas Department of Transportation had made roadway and associated water line improvements in an area that Houston Public Works did not know about. Consequently, the flow conditions were different than the ones specified during design. The pumps in one facility were fighting against the pumps in another facility and were not producing the required flows. To resolve the issue, the project team performed controlled field tests under different conditions for several days. During each test, the engineers recorded the flow and pressure data. First, the pumps were tested under lower flows, then a valve on the discharge header was opened to produce more flow. This process was repeated for each pump individually until the pumps delivered the optimum hydraulic performance to work in tandem with each other.
Another challenge was determining the construction sequence so Houston Public Works could continue serving customers when facilities are out of service, while keeping the construction costs low. Houston Public Works serves major customers such as the Houston Methodist Willowbrook Hospital and Willowbrook Mall. As such, Houston Public Works stipulated that no more than one facility in the Willowchase area could be shut down to meet system demands. Also, two of the groundwater facilities are located north of FM 1960 (a major highway) and two are located to the south. Houston Public Works required that at least one of these facilities, either north or south of FM 1960, always remain in operation. Considering these requirements, the engineering firm provided the contractor two construction schedules to complete the work on all four facilities. The schedules took into account winter periods, lag time to avoid shutdowns during summer months when demand is typically high, as well as potential setbacks such as delays in equipment, procurement, inspections, SCADA troubleshooting and training.
The ensuing COVID-19 pandemic added another complication during construction. High water pressure due to closed businesses led to false test results. To reduce system water pressure, another facility was shut down.
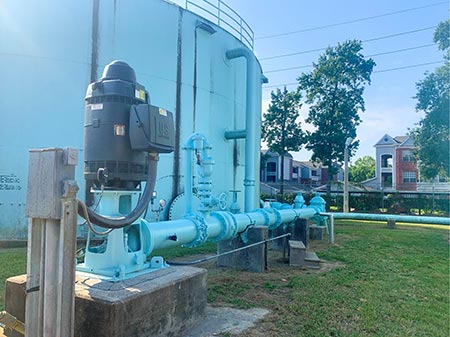
Lessons Learned
One of the keys to the project’s success to-date has been the collaboration with the operations staff. In addition to working with Houston Public Works’ engineering group, which is responsible for implementing the project, design engineers held meetings with staff who run the facilities’ mechanical, electrical, civil and SCADA operations.
During these meetings, the project engineers realized that the operations staff had varying needs. With staff having limited time to review design drawings, mini workshops were held to get input at different stages of the design. This helped the design team deliver the end product to everyone’s satisfaction.
Communication was another critical factor. The Willowchase system improvements were part of a group of projects that Houston Public Works was implementing at the same time. As such, documenting and communicating the decisions made at various stages of the project was important to maximize the time during reviews.