7 answers about this wastewater treatment technology.
JWC Environmental
09/18/2018
Two-shafted grinders have been a fixture within sludge treatment systems of wastewater treatment plants since their invention in 1973. The industry has undergone significant changes since then, but the need for grinders has persisted and evolved with the requirements of plant operators and engineers. Here are common questions about the use of grinder technology in sludge systems and some important things to consider when selecting sludge grinders.
1. Why were grinders first used within a treatment plant’s sludge system?
The number one reason grinders have become a staple in treatment plants around the world is their ability to protect sludge pumping equipment. Due to the viscous nature of sludge, several kinds of pumping technologies are typically employed to move the thickened materials. Some of these, like progressive cavity pumps and rotary lobe pumps, rely on elements with close tolerances. These pumps can be damaged by harder debris and fouled by rags or other stringy materials in the sludge. The grinders are used to shred the materials small enough so the pumps can do their job efficiently.2. What makes grinders a good option for protecting sludge systems?
The cutting shafts on most two-shafted grinders operate at a low rotational speed but with a high torque for tearing through tough solids. This is important because one thing that is certain in wastewater systems is that the operator will encounter the unexpected. While most sludge is consistent and benign, it only takes one rag ball or piece of clothing to shut down sludge handling equipment.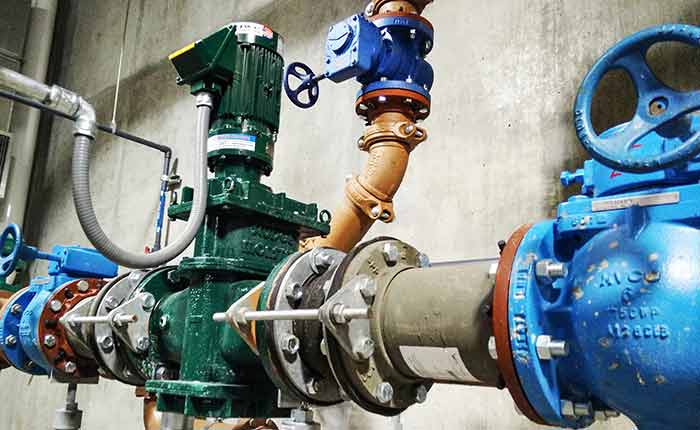
3. What has changed in the applications for grinders in sludge systems?
Protecting pumps remains the top role for grinders in sludge systems, but the sophistication of biosolids processing in treatment plants has seen significant advancements during the last 45 years. These changes have exposed new areas where grinders are needed to help overall plant efficiency. Grinders are now routinely installed to protect centrifuges and heat exchangers from debris that can put those systems out of commission. The cost of a grinder is a small insurance policy compared to a significant repair on a centrifuge or other expensive piece of capital equipment.4. With the improvements in primary treatment, especially headworks fine screening, is there less debris in sludge today?
The short answer is “yes” for plants with perforated plate fine screening systems. Some of the largest items that would have historically been found in a plant’s treatment systems are now pulled out at the headworks. That said, smaller debris like hair, bits of rag materials, and other inorganics still make their way into the plant and the digestion systems, driving the need for grinders. Another common entry point for unwanted trash is through secondary sources like trucked-in septage or sludge from remote facilities that is not passed through the headworks fine screens. This small debris has an amazing ability to come together in the digester and form hair balls, wipes ropes and other tougher solid masses. When sludge is drawn off the bottom of tanks or passes through a recirculation loop, the solids will quickly shut down pumps.5. What has changed in sludge grinder technology?
It has been an interesting journey with sludge grinder technologies coming and going through the years only for some to return again. Macerator technologies are again gaining traction in the North American market for sludge pump protection. Macerators, which use a high-speed blade rotating against an orifice plate, were tried in the 1980s and are on the rise today. Tougher solids such as rags, hair and other stringy materials need tough equipment to avoid them causing shutdowns. New technology advancements including serrated cutters are specifically designed to take on disposable wipes and rags. One such cutter first saw overwhelming success in protecting lift station pumps within collection system networks where wipes problems are the worst. More recently, treatment plants have been using the technology for their inline sludge grinders. Users report better performance in cutting through rags and hair within recirculation loops and waste activated sludge (WAS) lines.