In municipal applications, operators must understand which technology will best meet their needs.
Cornell Pump Company
10/05/2016
.jpg)
Changing Composition
For more than 100 years of municipal wastewater pumping history, solids-handling capabilities had been based on passing a spherical solid of a specified diameter. In an often-replicated show of a pump’s ability, an original equipment manufacturer (OEM) would demonstrate passing a baseball or other similarly sized object through a pump to visually indicate how that particular type of equipment could handle 3-inch solids. Today, wipes, rags, greases and other materials rope together, creating 6-foot-long (in some instances, much longer) masses wound into a clot of fibrous rags. These rag ropes can bind around an impeller or plug before a suction, making it impossible for them to pass through a wastewater design that may have worked successfully for generations. Increasing clogging problems make it apparent that typical non-clog pumps are no longer the solution in many cases. In numerous applications where the pump suction inlet is greater than 10 inches or where the waste stream is relatively free of wipe products, centrifugal solids-handling pumps remain a viable choice. But in more aggressive applications—which are becoming increasingly common—it is necessary to reduce the size of the solids entering the pump through some form of chopping, cutting or grinding.Pump Options
A number of equipment options can manage these tougher applications. These options include pumps designed to chop up harder solids, cut or shear stringy materials, or grind sewage in the primary stages of the system. The following pump types are commonly used in these aggressive solids-handling applications. Chopper Pumps Chopper pumps are centrifugal pumps typically fitted with a fixed set of cutting bars and a rotating cutting element mounted externally at the pump suction. This configuration breaks up solids to a manageable size, allowing the materials to pass through a standard solids-handling impeller. The chopper blades break up solids as they pass across the bars before entering the pump suction. This is an effective design for solids reduction, although the external element can affect the pump’s net positive suction head required (NPSHR) capabilities and efficiency. Chopper pumps have proven to be effective in handling heavier and harder solids because of their robust design. Cutter Pumps Cutter pumps are designed to achieve the same goal of solid size reduction. In cutter pumps, the impeller is the device that drives the rotating cutting action, while the stationary element is mounted at the pump’s suction inlet. The stationary cutter is often a fixed ring with cutting teeth or a knife-like blade that shears materials entering the impeller eye, allowing ragging components to pass directly into the pump. There is less restriction at the inlet of the cutter pump compared with a chopper pump. Cutter pump NPSHR and efficiency generally are better than that of chopper pumps because of the pump design, but the trade-off is that cutter pumps do not handle larger, harder solids as easily as chopper pumps. Cutter pumps have proven to perform well in applications where long, stringy materials are present, and the pumps are hydraulically efficient. Grinder Pumps Grinder pumps also use an impeller designed with a rotating cutting device that macerates materials at the pump inlet. This pump type typically is found in lower-flow applications. Many grinder pumps are a submersible design, run at higher speeds and mainly are installed at the source of supply to the main sewage system (for example, commercial buildings, hotels, hospitals and other institutions). Smaller grinder pumps can break down materials, reducing maintenance costs for building owners at the source of supply.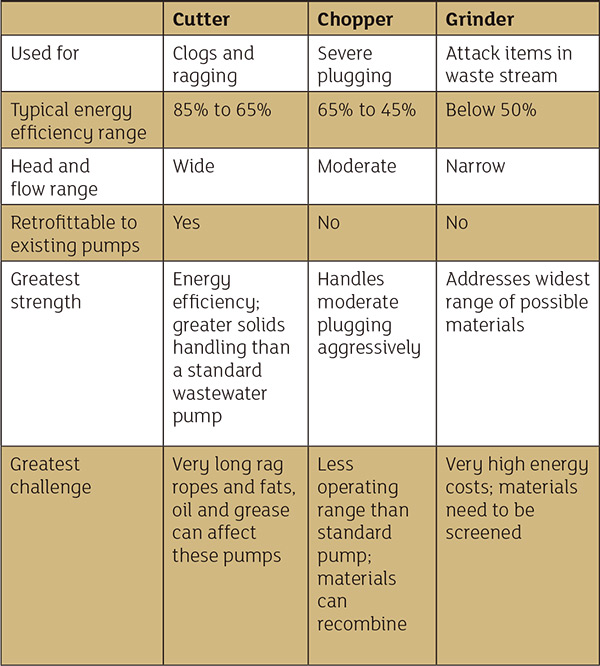
System Efficiency vs. Pump Efficiency
End users must ask several questions when selecting a solids-handling pump:- What is the net positive suction head available (NPSHA)?
- Will a variable frequency drive (VFD) be used?
- What is the system being designed for?
- How heavy is the solids concentration?