The power generation sector, like many others, is under constant pressure to minimize downtime and maximize productivity. For this reason, end users expect pump equipment to run for longer periods with reduced maintenance intervals. When repairs are needed, they have to be completed within tight deadlines to comply with ever-shorter maintenance windows. With such a wide variety of pumping processes on-site, finding a repair provider with the necessary skills and experience to deliver full turnkey service is a challenge. A great deal of the rotating equipment used in the power generation sector has been in place for many years. Pump equipment has been rigorously maintained and serviced in order to ensure reliable performance. As service and maintenance intervals increase, the attention given to maintenance procedures has become more focused. Employing a properly structured and managed program can enable large sites that are equipped with vast numbers of assets to achieve high productivity levels while maintaining the plant’s long-term reliability.
Plant Requirements
Successful asset maintenance requires an understanding of the needs of each piece of equipment, the overall production process and the implications of taking assets offline. In most cases, assets will have standby systems that can keep a process operational, even at a lower productivity rate. The experience and knowledge of on-site maintenance engineers provides the most useful information. By working closely with a repair provider, a facility can develop an efficient maintenance schedule. The diversity of pump design and technology used within the power generation sector means that finding a repair partner can be a daunting task. The original equipment manufacturer (OEM) might seem to be the obvious choice to complete repairs. However, the presence of a wide range of pump designs across an entire facility would mean coordinating a maintenance program with a large number of third-party organizations. This requires significant administration efforts and site coordination. As a result, selecting the most appropriate partner that delivers both OEM technology and the ability to support equipment of multiple manufacturers is key to achieving the maintenance goals of the business.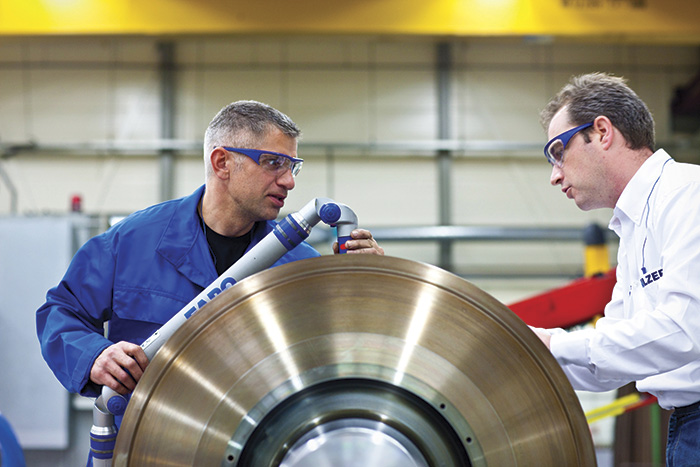
Service Delivery
Assessing the skills and capabilities of a maintenance provider is crucial for determining the overall level of service that can be delivered. Providing preventive maintenance services is important, but when a component fails, the priority must be to deliver a fast turnaround and get the equipment back into service.Today’s number of complex pump designs in service has led to a demand for a single-source solution that has the capability to repair, re-engineer or remanufacture damaged components using in-house resources. The alternative—using providers that subcontract repairs to compensate for a lack of in-house facilities—can increase the complexity of the project, degrade the communication process and lead to less dependable repairs. Those with experienced design capabilities can also integrate improvements into component design, enabling end users to benefit from the latest manufacturing technologies and improve both efficiency and reliability. Note that for some power providers and first-tier contractors, the requisite combination of skills and facilities must be available to a combination of fuel sources from natural gas and fossil fuels to nuclear and renewables anywhere in the world, since power generation is often a global business.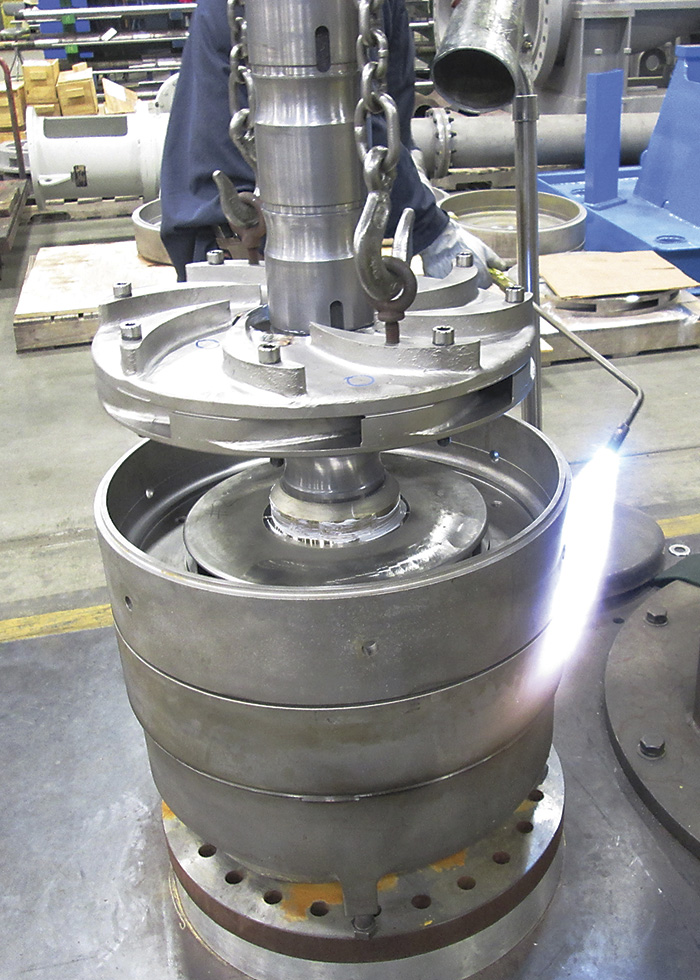
Developing a Plan
When partnering with a maintenance provider, facilities must develop a program of planned actions and make contingency plans for unexpected failures. By implementing a carefully organized plan, these plants can increase reliability and maximize productivity by incorporating a range of techniques and facilities. At the most basic level, condition monitoring is a vital tool that can use vibration, pressure and temperature monitoring equipment, plus manual thermal imaging cameras, to provide important information and detect early signs of impending failure. Both of these predictive maintenance methods do not require stopping the equipment, and they can provide regular data for a preventive maintenance program. These steps form the basis of a planned maintenance scheme that should be supported by additional information such as pump performance data, which can also reveal early indications of a performance issue. Collectively, this information enables the on-site maintenance team to schedule repairs during planned shutdown periods, minimizing the impact on productivity. Despite these proactive steps, however, component failures will still occur. The ability of the repair partner to react quickly and deliver a solution will determine the long-term viability of any maintenance agreement. One way to facilitate this partnership is to incorporate an internal communication structure that allows a local service center to deliver the full range of technical services to end users, while drawing on the service provider’s engineering and logistics resources.Tight Deadlines
One example involves a major energy provider that required a 21-day turnaround on two high-speed boiler feed pumps. The equipment owner presented a detailed repair specification that was to be followed precisely. This particular style of pump required developing clear and precise inspection templates, instructing and reviewing with the shop personnel where and how to inspect the critical fits, and recording the required information to meet the energy provider’s criteria for initial inspection. One of the first requirements was a special cleaning procedure the service center managing the repair was not equipped to do. By using the service provider’s other facilities located nearby to accommodate the demand, however, the cleaning procedure was quickly completed without incurring any delays. Once complete, the pumps were returned to the original service site to begin disassembly. Inspection of the individual components determined that some of the impellers were damaged and were deemed irreparable. The hub side plates on at least half of the series impellers were cracked and required replacement. The facility had not planned for this level of damage, and replacement components are not typically stored by either the user or the manufacturer.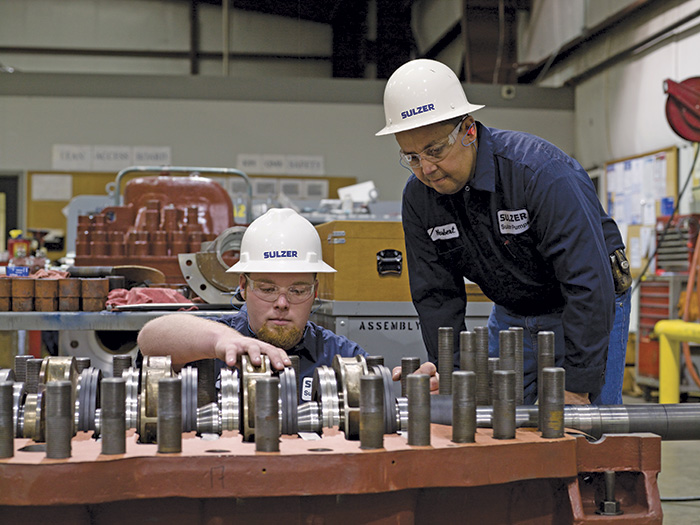