Today’s federal requirements dictate the minimum efficiency of an electric motor, but they do not have any impact on the efficiency of a centrifugal pump. A 10-horsepower, 1,800-rpm motor must meet a minimum efficiency of 90.2 percent, but no such restrictions exist for a 10-horsepower pump—and that is a good thing. Lower efficiency pumps can actually reduce the total operating costs in some instances. Vortex sewage pumps are a good example. In most applications, however, high efficiency pumps should be selected because they can drastically reduce electric power costs.
If I did not know better, I would think that the total efficiency of a pump and motor would be the average of the two individual efficiencies. If a motor is 90-percent efficient and the pump is 78-percent efficient, the average would be 84 percent. That would be ideal. Unfortunately, the total efficiency of a motor and pump when operating together is the product of their individual efficiencies, and that product reduces the total efficiency value to well below the average.
Sometimes, this is hard to comprehend because so many units of measure are involved. To make it easier, I like to use a very simple energy unit—a bag of energy. Figure 1 illustrates this concept. If 10 bags of energy enter the motor and seven bags exit the pump, the total efficiency is 70 percent. If 10 bags enter the motor and nine bags exit the motor, the motor efficiency is 90 percent. If nine bags enter the pump and seven exit the pump, its efficiency is 78 percent. The only way to calculate a total efficiency of 70 percent is to multiply 90 percent by 78 percent.
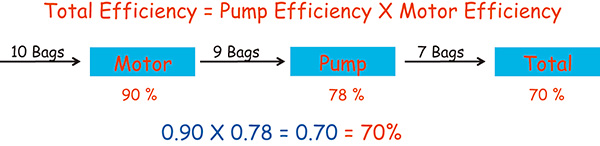
This total, or wire-to-water, efficiency is a major factor when calculating the power cost for pumping some amount of water. One of the more common cost units is the cost per thousand gallons pumped and is calculated using Equation 1.
Cost/1,000 gallons = (0.189 x Cost/kWh x Head) / (Pump eff x Motor eff x 60)
Equation 1
The power cost per thousand gallons is directly proportional to the cost per kilowatt hour (kWh) and pump head while inversely proportional to pump and motor efficiency. Let’s compare the electrical costs for two different pumps.
Figures 2 and 3 show the power cost per thousand gallons pumped for two pumps. Both are real pumps and are popular in several water markets. The best efficiency point (BEP) for both pumps is 1,000 gallons per minute at 127 feet, and the power cost is 10 cents per kilowatt hour.
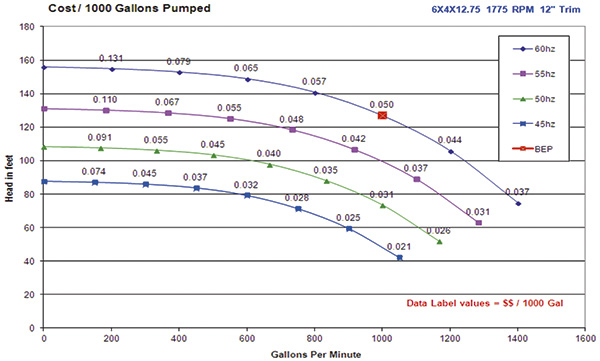
Figure 2 shows the cost per thousand gallons pumped for a pump with a BEP efficiency of 85 percent driven by a motor with an efficiency of 93 percent. The wire-to-water efficiency is 79 percent. At 60 hertz (Hz), the power cost at the BEP is 5 cents per thousand. Because the cost per thousand gallons is also directly proportional to head, the cost drops to 4.2 cents at 55 Hz, 3.5 cents at 50 Hz and 2.8 cents at 45 Hz. If this pump runs eight hours per day at 60 Hz, the annual electrical cost will be $8,760.
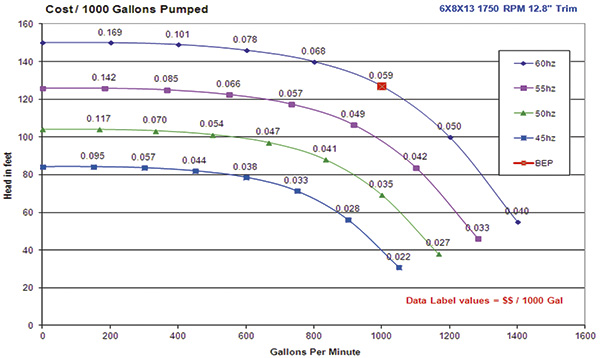
Figure 3 shows the cost per thousand gallons pumped for a pump with a BEP efficiency of 73 percent driven by a motor with a 93-percent efficiency. The wire-to-water efficiency is 68 percent. At 60 Hz, the cost at the BEP is 5.9 cents per thousand. As with the previous pump, reduced speed also results in a lower cost. Operation for eight hours per day at 60 Hz will result in an annual electrical cost of $10,337. In this comparison, an 11-percent reduction in wire-to-water efficiency results in an 18-percent increase in power cost.
The U.S. Energy Information Agency reports that the July 2013 average cost per kilowatt hour across the U.S. was 10.71 cents. This represents a 3.9 percent increase from July 2012. Residential averages were highest at 12.61 cents and industrial averages were lowest at 7.32 cents. Energy cost also varied greatly by region. The highest average rate was Hawaii and Alaska at 27.2 cents. New England was second at 14.3 cents and the Middle Atlantic states were third at 12.74 cents. The lowest was the West South Central states (Texas, Louisiana, Arkansas and Oklahoma) at 8.12 cents. The remainder ranged from 8.48 to 11.17 cents. Energy costs will continue to rise, so end users should ensure that their pumps operate at maximum efficiency.