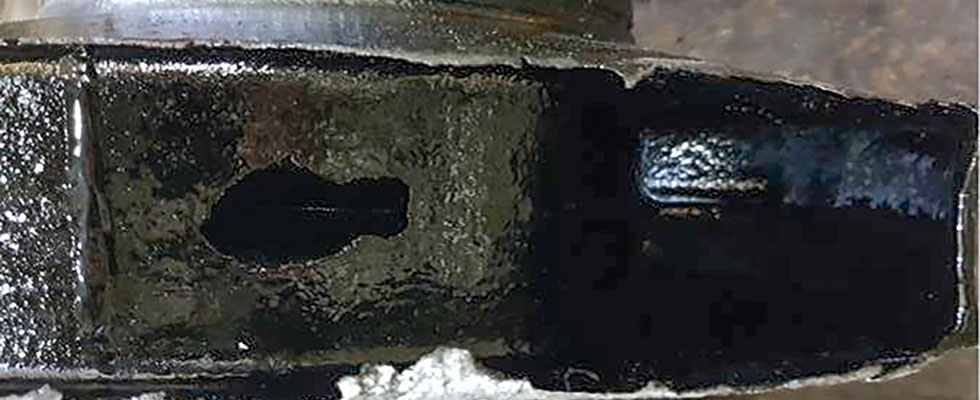
A refinery crude processing plant has had a crude vacuum unit in operation since 2014. Each processing train has two 460-kilowatt (kW) bottom vacuum residue pumps. The pump is a single-stage with a rated flow of 638 cubic meters per hour (m3/h), differential head of 205 m and an operating temperature around 360 C.
This service is challenging considering the high temperature and crude containments environments. The subject pump suffered from vibration problems and reparative failures since commissioning in 2014. Field operation reported a recent pump outage, which took one of the operating pumps out of service due to high vibration.
Comprehensive review and troubleshooting were conducted and revealed design and operations flaws were affecting the pump’s reliability.
Operations
Pump operation trends were reviewed and compared with the manufacturer’s curve. The analysis of pump operation revealed that all of the pumps of the same design were operating at lower flow than rated, almost 50% of best efficiency point (BEP). This low flow operation highlighted an equipment oversizing issue, which contributed to the low reliability of the pumps. In addition, overall vibration trends showed a gradual increase in casing vibration since commissioning.
Dismantled Inspection
The pumps were dismantled to have a closer look at the failed components. The following findings were made:
Erosion in the suction and discharge side was found on the impeller due to suction and discharge low flow recirculation.
There was severe corrosion on the impeller.
Impeller material was checked and found to be American Society for Testing and Materials (ASTM) A439 austenitic nodular cast iron.
Drive end impeller wear ring was seized with the casing wear ring.
The non-drive end impeller wear ring was missing.
Pump casing, made of A487 CA6NM, was in good condition no signs of corrosion or erosion were found.
Analysis
The pump’s operation at low flow, away from the BEP, created stresses on the pumps and introduced suction and discharge recirculation as manifested in the impeller’s inspections findings.
Additionally, the pump material of construction was under question due to the corrosion found on the impeller. The impeller is made of ASTM 439 cast iron material; the pumped service is crude oil in a vacuum unit that contains elemental sulfur that can cause corrosion at high temperatures. The amount of total sulfur in a crude oil depends on the oil field and varies from 0.05% to 14%. Sulfur values as low as 0.2% are enough to create sulfidation corrosion in plain steels and low alloy steels.1
ASTM 439 contains 1.75% to 2.75% chromium, as per the Modified McConomy curves below the anticipated corrosion rate at an operating temperature of 360 C, exceeding 0.1 millimeters(mm)/year without considering any other factors such as fluid velocity and erosive particles in the services. All of the above created and accelerated a corrosive environment.
Recommendations
The first suggestion is to improve pump operating conditions to be operated closer to the design parameters. Second, the impeller material should be upgraded to at least A487 grade CA6NM with a higher chromium percentage (11% to 14%), which will have better corrosion resistance and eliminate material deficiency.