This equipment eliminated a SAG copper mill gearbox’s maintenance issues resulting from contact lip seals that had a short and unreliable service life.
03/24/2014
When a representative from a local distributor noticed a large amount of oil leaking from a semi-autogenous grinding (SAG) mill gearbox at a copper mill, he decided that a permanent solution to the maintenance issues caused by inefficient sealing methods was needed.
The Unacknowledged Problem
The distributor repeatedly noticed the leak on his regular visits to the site, a large copper mining and mill operation in the Southwestern U.S. The gearbox had been plagued with leak-related issues during the 10 years that he had called on the mill. Like many gearboxes, it included contact lip seals that tend to have a short and unreliable service life. Because of the contact with the shaft to retain lubrication, they eventually wear at the point of contact or groove the shaft. As they lose contact, lubricant leaks at the point where the shaft enters the gearbox. With this gearbox, an operational flood in the bearing housing compounded the difficulty. Unlike most gearboxes that splash oil into the bearings, the gearbox operating in this process included an oil pump that pumped oil into the center of the double row spherical roller bearings. This ensured continuous lubrication to the bearings, but also tended to throw oil toward the lip seal. Oil that was attempting to flow back through the bearings to return to the sump was impeded, creating an operational flood. The operational flood placed additional pressure on the lip seal which increased the failure rate of the seals. The sealing solution for the mill needed to be able to perform in an operational flood and be installed onsite without decoupling equipment.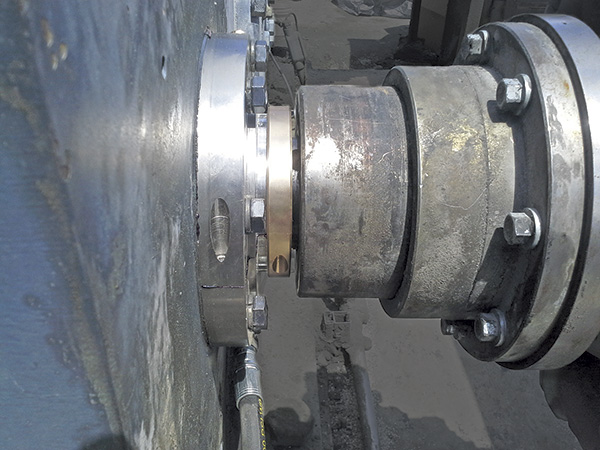
- It could only be performed during scheduled downtime.
- Three personnel members were required for the replacement.
- The process took three to four hours to complete.
The Solution
High oil levels and oil splash make gearboxes notoriously difficult to seal, especially in industrial rotating applications. The lip seals commonly used to seal gearboxes have high failure rates and a short life expectancy, making them ill-suited for applications such as those at the mill. A custom-engineered solution was the key to creating a permanent sealing answer to the mill’s sealing problem. A sealing/bearing isolator company’s design team was tasked with engineering the solution. The team had the experience to consider critical factors that included:- Size restrictions
- Lubrication type
- Bearing type
- Flooded applications